At NextGen Material Testing, we offer a comprehensive selection of certified metal testing machines that are engineered to guarantee precision, repeatability, and adherence to international standards such as ASTM, ISO, and DIN. Our material testing systems are capable of supporting a diverse array of applications, including advanced analysis in research laboratories and quality control on the factory floor.
NextGen provides fully integrated solutions that are customized to meet your operational needs, including hardness testing systems, universal testing machines (UTMs), impact testers, metallography preparation tools, and tensile specimen milling equipment.
Types of Metal Testing and Available Equipment
Different types of metal testing serve different purposes—some focus on surface hardness, others on structural strength, impact resistance, or sample integrity. That’s why selecting the right equipment depends on the specific property you’re testing and the industry standards you need to follow.
NextGen offers a full suite of testing systems to cover every stage of metal evaluation, from initial sample preparation to advanced mechanical testing. Whether you're checking the tensile strength of steel, verifying the hardness of treated surfaces, or analyzing fracture behavior, our equipment is designed to deliver consistent, standards-compliant results.
Metal Hardness Testing Equipment
Hardness testing is one of the most common methods used to evaluate the surface properties of metallic materials. It measures a material’s resistance to deformation when subjected to a controlled force through an indenter. At NextGen, we provide a complete range of bench-top and portable metal hardness testers capable of performing various test methods, including micro, macro, and standard-scale testing.
Our systems support Rockwell, Brinell, Vickers, and Knoop methods, each suitable for different materials, geometries, and surface conditions. Whether you're testing thin coatings, case-hardened parts, or non-uniform castings, we offer the right equipment for accurate and repeatable results.
Common Standards Supported:
- ASTM E18 – Rockwell hardness testing using depth-of-penetration methods
- ASTM E10 – Brinell hardness testing using ball indenters and larger loads
- ASTM E384 – Microhardness testing for Vickers and Knoop methods
- ISO 6506 / ISO 6507 / ISO 4545 – International standards for Brinell, Vickers, and Knoop hardness testing, covering machine verification, procedure, and result interpretation
Universal Testing Machines (UTMs)
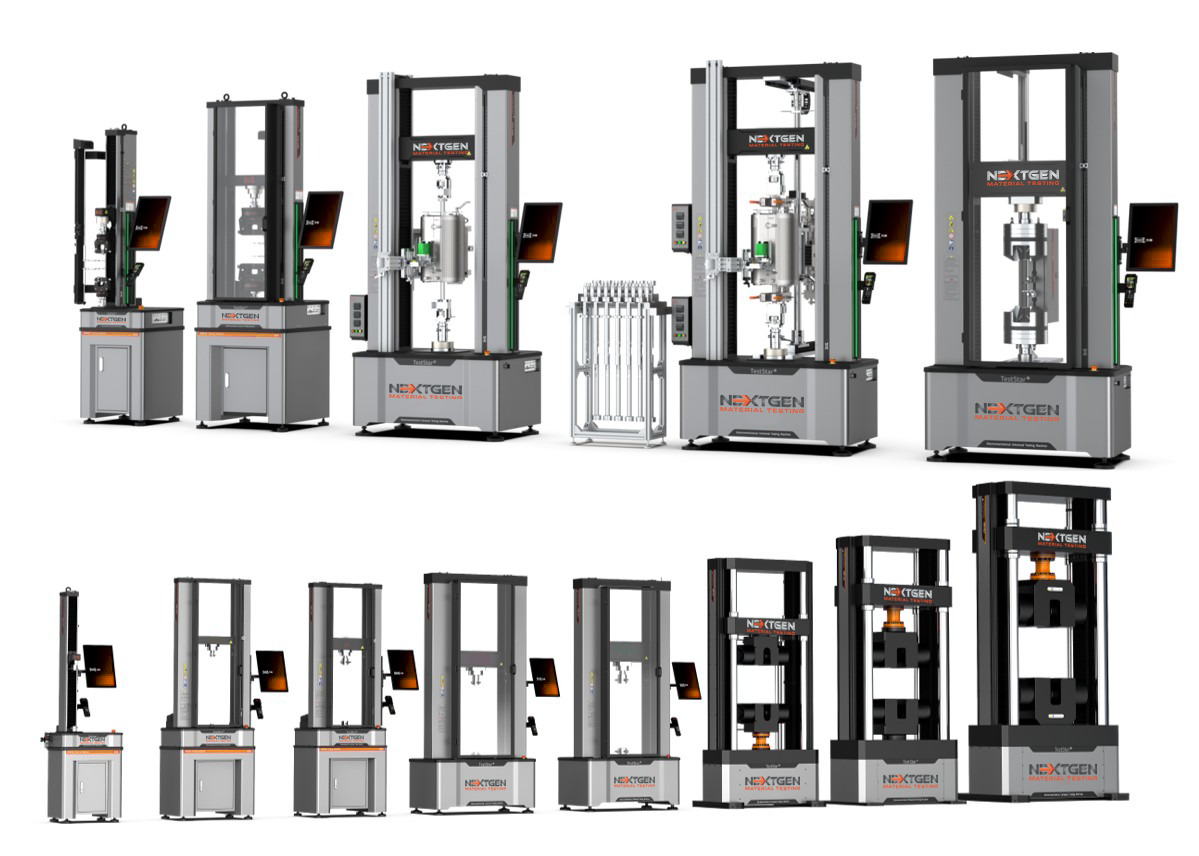
Universal Testing Machines are the backbone of mechanical testing for metals. These systems apply tensile, compressive, flexural, and shear forces to evaluate the strength, elasticity, ductility, and failure behavior of test specimens. We offer both electromechanical and servo-hydraulic UTMs, designed for precise and reliable testing under static load conditions.
UTMs are useful for the determination of properties such as yield strength, elongation, ultimate tensile strength, and fracture load. Our machines are capable of handling an array of sample sizes and materials, as they are configurable for a number of fixtures and extensometers.
Common Standards Supported:
- ASTM E8 / E8M – Tensile testing of metallic materials (flat and round specimens)
- ASTM A370 – Mechanical testing of steel products
- ISO 6892-1 – International method for tensile testing under ambient temperature
- EN ISO 527 – Tensile properties of plastics and polymers (for multi-material applications)
- ISO 7500-1 – Verification of UTM force accuracy and calibration
Metallography Sample Preparation Equipment
Metallography plays a critical role in understanding the internal structure and grain behavior of metals. Before any microstructural analysis or surface testing can take place, samples must be properly prepared. NextGen offers a complete suite of metallographic preparation equipment, including abrasive and precision cutters, automatic grinders and polishers, mounting presses, and etching stations.
These tools are used to reveal surface features and prepare cross-sections for hardness testing, microscopy, or failure analysis. Consistency, safety, and compatibility with a diverse array of specimen types and sizes are the primary objectives of our systems.
Relevant Standards:
- ASTM E3 – Guide for metallographic sample preparation
- ASTM E407 – Microetching techniques to reveal grain boundaries and phases
- ISO 6507 – Vickers hardness testing of prepared metallographic surfaces
- ISO 4287 – Surface texture and roughness evaluation
Tensile Sample Preparation Equipment
Proper specimen preparation directly affects the reliability of tensile test results. Deviations in specimen dimensions or surface finish can result in misleading data and failed certifications. At NextGen, we supply advanced flat and round tensile sample preparation machines tailored to meet key geometric tolerances and finish requirements for metals.
Our equipment supports rapid and precise machining of standardized samples used in UTMs, minimizing operator error and improving test repeatability. Custom fixtures and inserts are available to support various material types, including aluminum, steel, and Inconel.
Common Standards Supported:
- ASTM E8 / E8M – Geometry and machining requirements for tensile specimens
- ASTM A370 – Preparation and testing of steel and other metallic products
- ISO 6892-1 – Tensile testing method including sample prep standards
- DIN 50125 – Standard dimensions for metallic tensile specimens in Europe
Impact Testing Equipment (Charpy and Izod Systems)
Impact testing is used to measure how materials respond to fast, high-energy loading conditions. It’s a vital method for assessing toughness, ductility, and the tendency of a material to fail in brittle or ductile modes—particularly in safety-critical applications. NextGen provides high-performance Charpy and Izod pendulum impact testing systems with manual and fully automated options.
Proper notching of specimens is critical in this process. We also offer sample preparation equipment that ensures accurate notch geometry, surface finish, and alignment for reliable impact results.
Key Standards Supported:
- ASTM E23 – Notched bar impact testing (Charpy and Izod methods)
- ISO 148-1 – Determination of impact energy using Charpy pendulum systems
- EN 10045-1 – European Charpy impact testing standard for metallic materials
Consumables and Accessories for Complete Testing Workflows
NextGen provides an extensive line of precision-matched accessories and certified consumables to guarantee that your metal testing equipment operates at peak efficiency. These parts are made to match each product type, helping your equipment run efficiently while supporting repeatable testing and minimizing wear over time.
We offer certified Brinell indenters, diamond cone Rockwell indenters, and Vickers/Knoop microhardness indenters for hardness testing, as well as traceable hardness test blocks that comply with ASTM and ISO calibration standards.
Also, we offer a diverse array of tensile specimen inserts, gripping fixtures, and cutting inserts for the machining of both flat and round tensile sample preparation. Our consumables have been engineered for various kinds of materials, including soft metals, hardened steels, and superalloys such as Inconel.
Our catalog contains abrasive cutting wheels, mounting resins, diamond suspensions, grinding papers, and polishing cloths for metallographic preparation. These items have been carefully chosen to make sure that they are compatible with a range of sample types and provide consistent surface finishes. Our products guarantee accurate results, no matter whether you are preparing a sample for microstructure analysis or Vickers hardness indentation.
Every item is backed by traceable manufacturing and designed for direct compatibility with NextGen systems and most third-party brands. We maintain a strategic inventory for fast delivery across North America, helping you reduce downtime and stay on schedule.
Industries and Applications for Metal Testing Equipment
NextGen’s metal testing equipment is trusted across industries where material strength, structural performance, and regulatory compliance are mission-critical. Whether used on the production floor or in R&D laboratories, these systems help validate material properties before components go into service.
Aerospace and Defense
Metal testing systems are integral in the aerospace manufacturing industry for the assurance of the hardness, tensile strength, and fatigue resistance of components used in structural frames, fasteners, and landing gear. Brinell and Rockwell testers are often used to confirm heat treatment results, while UTMs validate load-bearing capacity in accordance with international aerospace standards.
Automotive and Mobility
Metal testing equipment supports quality control in automotive production by measuring hardness in drive shafts, brake rotors, and transmission parts, and confirming ductility in welded joints and chassis components. Charpy impact testers are commonly used to assess brittle fracture behavior in high-speed collision scenarios.
Energy and Power Generation
In energy applications—especially in oil & gas, wind, and power infrastructure—hardness and tensile testing are used to confirm the mechanical integrity of pipes, pressure vessels, and turbine blades. These systems help ensure that metallic materials can withstand thermal cycling, corrosion, and high-load conditions over extended service lifespans.
Construction and Infrastructure
Materials testing is necessary in the fabrication of structural steel and civil engineering. Universal Testing Machines and metallography systems are used to assess the strength of reinforcing bars, anchor bolts, and welded joints in bridges, tunnels, and high-rise structures.
Metal Fabrication and Heat Treatment Facilities
Hardness testers and UTMs are used in machine shops and heat treatment plants to confirm compliance with client specifications. They help verify case depth after carburizing, monitor hardness profiles along welded seams, and confirm metal strength after forming or machining.
Research, Education, and Materials Development
Academic institutions and industrial R&D labs use metal testing equipment to develop new alloys, validate treatments, or simulate service conditions. Systems like Vickers/Knoop microhardness testers and metallographic sample prep machines are essential for fine-scale material evaluation and cross-sectional analysis.