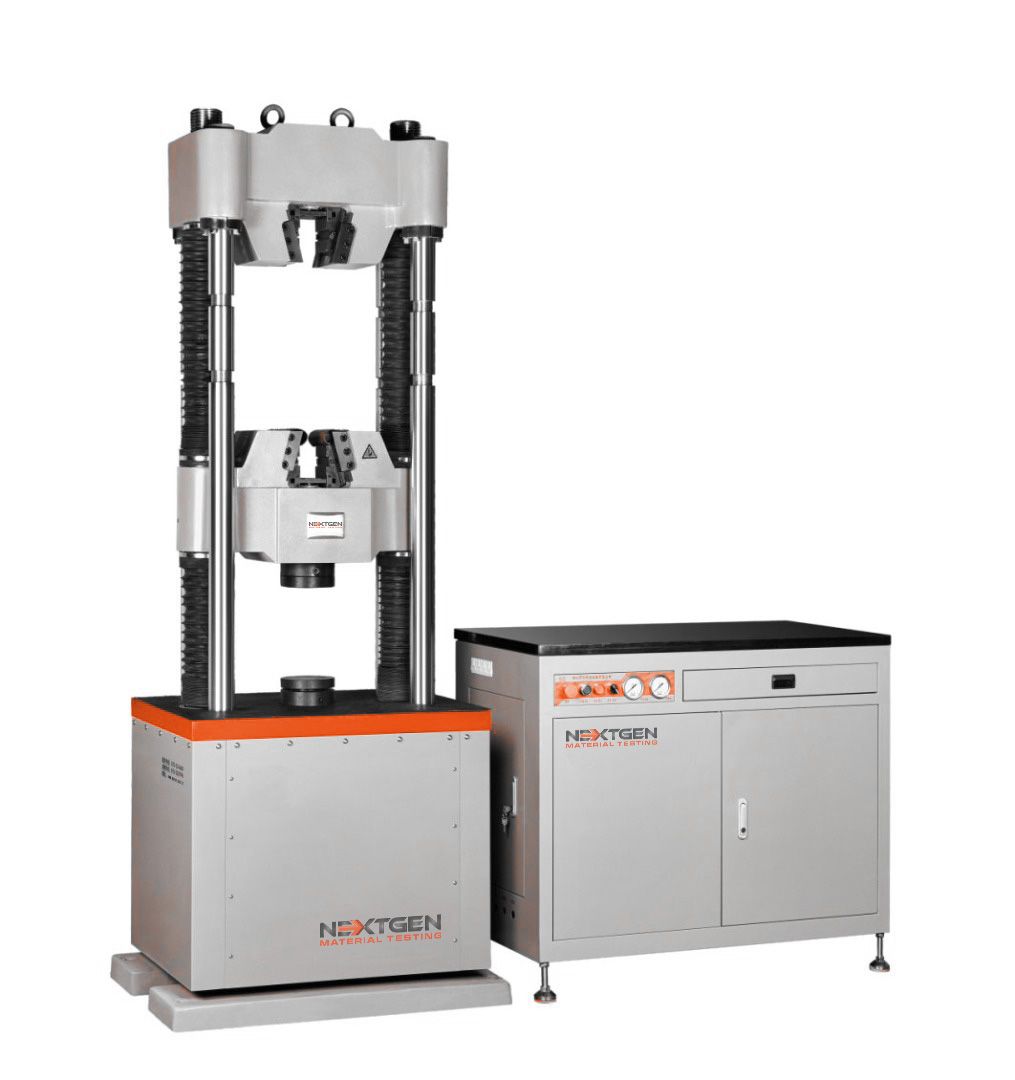
NextGen Material Testing provides you with a complete range of Universal Testing Machines, also known as a tensile tester. A universal testing machine is used to test different materials for tensile stress, compression strength, bending and other mechanical properties of a wide range of materials. Our systems can come equipped with a wide range of fixtures to meet all your testing needs. We supply grips and fixtures according to almost every ASTM and international standard in the industry.
Based on your application and capacity requirements, you can select between a force stand, an electromechanical testing machine or a servo hydraulic universal tester for your high capacity testing needs. These machines each have their own advantages which are target towards different applications. Feel free to click on one of the testers below for more information.
The NextGen testing frames incorporate precision electromechanical load frame equipment to meet all of your testing needs. Built according to industry standards, the NextGen EML line features or latest Gentest software which comes pre-programmed with some of the latest testing methods.
The NextGen testing frames provide a solution for high-capacity applications for a wide range of high-strength materials to meet all of your testing needs. Built according to industry standards, the NextGen SHM line features or latest Gentest software which comes pre-programmed with some of the latest testing methods.
NextGen Material Testing’s Alignment Device is a precision-engineered fixture designed to ensure perfect axial alignment in universal testing machines.
There are a number of benefits of purchasing your ideal universal tensile tester from NextGen:
User-Friendliness:
NextGen stands behind the optimal solutions designed to bring our clients the simplest and most effective systems in the market. Our Tensile Testing systems are easy to operate and maintain. They are developed with the end-user in mind.
Force Resolution:
Accuracy and repeatability is extremely important for the Tensile Testing process. NextGen’s tensile testers offer a minimum force resolution of 1/500,000.
This means that if you are testing 100kN system your force resolution will be exceptional down to 0.2N with 0.2% force accuracy. (100,000N / 500,000FS = 0.2N / FS).
Should you require larger load cells, such as 300kN or higher, an additional sub load cell can be purchased to enhance your force resolution for lower testing capacities even further.
Learn more by contacting us today.
Full Scope of Grips and Fixtures
NextGen offers the full scope of standard and customer grips and fixtures for your universal tensile testing needs. We have you covered for pulling, bending, shearing, compression, and much more.
Though custom grips may take 1-4 weeks to manufacture, most all standard grips are readily available in stock.
Learn more by contacting us today.
Price:
Due to high sales volumes, are pricing are typically tremendously lower than our major competitors.
The quotation always comes standard with all of your desired grips and fixtures included in the price of the main unit. Your units will also come standard with our state-of-the-art tensile testing software, controller, remote control handset, and much more.
Simply confirm your technical needs and ask for quotation today and let NextGen impress you.
Customer Service and Support
NextGen Material Testing's philosophy is to provide the highest quality customer service combined with the best available products and services. This is the reason why thousands of manufacturers, educational facilities, government bodies, N DT facilities, laboratories, etc. utilize NextGen equipment for their most important quality control requirements. NextGen continues to provide high end services in relation to delivering material testing equipment in the market for over 18 years.
Warranty
We are confident in our products, and with our 12-month plus extensive warranty coverage, we know that you will be too. All NextGen machines are backed by a life-time service and support guarantee. This means that as long as you are operating one of our machines, our engineers are always available to help answer your questions, trouble shoot any issues and provide you with the required solutions in the shortest possible amount of time. Whether you are within your warranty terms or outside, NextGen Material Testing, Inc. has got you covered. Our extensive global network of partners offers the option to have a qualified engineer visit your facility virtually anywhere you are. We are only a call or an e-mail away.
Both of our static and the dynamic Tensile Testing systems can have the furnace and the cooling chambers be added at a later time.
We do ask that our clients let us know of their future intentions of purchasing either a furnace or a cooling chamber for their tensile tester so that we can supply the necessary bracket for the job.
NOTE: Adding the furnace or the cooling chamber to the system in a single order is a simpler process than adding them at a later time.
Contact our qualified consultants today to learn more.
Absolutely!
Simply let us know what unit you would like to purchase and how long would you wish the warranty period to be. Our qualified consultants will quote you accordingly.
Due to the simplicity of the Class A, B and C Tensile Testing systems, the training and installation on these units is not mandatory. All you need are the correct cables. We will provide you a clear set of instructions to be able to perform the set up yourself.
Should you require additional support, we would be happy to have one of our engineers offer a remote session for you via an on-line platform. This will help you save on cost and achieve favourable results.
Learn more by contacting us to today.
Different materials can be subjected to the fatigue test, depending on the purpose in which they are intended for. Metals and composites are commonly subjected to fatigue tests because these materials are commonly used in applications where components are repetitively subjected to forces that can either bend or break them. Making sure that these materials have a high fatigue limit is essential for these applications, so they are commonly subjected to such tests. Other materials such as polymers, wood, and ceramics may also be fatigue tested to determine their suitability for specific applications.
There are multiple forms of fatigue testing, but the two most common ones being used in most industries are the load controlled high cycle and the strain controlled low cycle. High cycle testing is usually used to determine an object's ability to withstand elastic forces, while low cycle testing is usually used to determine an object's ability to withstand plastic forces.
The fatigue test is important for nearly all materials testers as performance in this test provide important information on the material's long-term durability for a specific application. Different data from the material can be extracted from these tests, such as fatigue strength, crack resistance, and overall durability. Fatigue life, or is the number of cycles a material can be exposed to before breaking, is also obtained using the fatigue test. Aside from the number of cycles, the amount of force that the object can withstand is also recorded. In contrast to bend tests and compression/tension tests, the object is subjected to fluctuating forces rather than a singular application of force.
A fatigue test is done to determine an object's ability to resist cyclic fatigue loading conditions. In this test, repeated loading and unloading forces are applied into the material, often at least matching the level of forces being applied to the object on where it's planned to be used. The forces can be in the form of tension, torsion, compression, bending, or even a combination of these forces as deemed appropriate. The most common forces applied in fatigue tests is alternating tension and compression. To perform the fatigue test, the material is placed in the testing machine, and then subjected to cycles of loading and unloading, often up to failure is reached.
There are 4 different types of bend tests that is commonly used in most industries. A guided bend test is where the material is placed horizontally in between 2 supports and then the force is applied right in the middle, ideally bending it into a U shape. A semi-guided bend test is done by bending the material to a specific angle or radius. A free bend test is where the ends of the material are pushed towards each other, but no force is applied to the middle. A common fracture toughness test uses a material that is pre-fractured, and then the bending force is applied at the opposite face from the fracture. Any of these tests can be used strategically to obtain specific data about a material's bending characteristics.
The bend test is performed to determine how much a material can bend without breaking and subsequently how much force it would take to bend it to a certain angle. Multiple data about the material can be obtained from the bend test, including ductility, bend strength, fracture strength, and fracture resistance. Conversely, if a material actually breaks during the bend test, the odds are great that such a material may not be the optimal choice for an application where strong bending forces are applied. As such, the information obtained from the bend test is potentially vital for safety reasons.
A bend test is a procedure wherein the force is placed right at the middle of the test material to bend it. The test is usually performed in increasing increments of force until the object finally breaks. In comparison to a flexure test where the goal is to actually break the material, the main objective of doing the bend test is to see how much force is needed to bend a material to a certain shape. The test sample is placed in the machine in such a way that a concave object can be created out of it when a force at midpoint is applied. A specific radius of curvature is set, and the material is bent to that radius if possible by applying force.
There are different variations of the compression test that will help testers get the data they need for specific purposes. The most common version of this test involves the application of 2 opposing forces into the material to create a compressive force. However, different variables can be altered to test different aspects of the material’s overall durability. The most common variation of the compression test is where the compressive forces are placed on multiple axes. The compression test can also be performed in extreme temperatures. These variations allow testers to better understand the characteristics of the material, especially when subjected to extreme compressive force.
A compression test is done to determine the compressive strength of a material, in addition to other material properties related to its ability to withstand compressive forces. With the help of this test, you can determine how a material responds to compressive forces, as well as the properties that explains its behavior in the presence of such forces. With the help of the data obtained from such tests, one can determine if a specific material is optimal to be used for applications where compressive forces are applied.
The compression test is a procedure that tests a number of a material's compressive strength, as well as other properties such as yield strength, ultimate strength, elastic limit, and elastic modulus. To perform this test, the material is subjected to compressive forces that push inward into the material. This force aims to crush, flatten, or squash the material. To perform this test, the material is placed in between 2 plates. The plates then apply increasing force into the material, which aims to flatten the object. The compression test is technically the opposite of the tension test. Because of the compression forces, the object gets shortened on the direction of the forced and stretched at the direction perpendicular to the force.
Compatibility is a must to ensure that testing machines can stay relevant for years. NextGen understands that purchasing testing machines can be a significant investment for any company, and keeping these machines up-to-date for as long as possible is essential for optimal return of investment. NextGen guarantees that all future accessories will be compatible for use with older machines. When designing their products and accessories, they see to it that they can be compatible not just with their new equipment, but also with most of their older machines.
All NextGen products are guaranteed to be compliant with all global testing standards. Engineers of this company stay up to date with all the latest industry standards such as ISO, GB, ASTM, and EIN. Being compliant with these global testing standards means that all NextGen equipment are compliant with the global standards for testing. NextGen even has some pre-made templates designed to replicate the most common global standard tests used in your industry.
Fatigue testing is a procedure wherein a relationship between a material's stress range and the number of times it can be applied before failure is established. In this test, the testing machine is used to apply a specific amount of force in a material for multiple cycles. The force can be applied in the form of tension, compression, torsion, and bending forces, among others. A combination of these forces can also be applied to simulate real-world forces that can lead to material fatigue.
The fatigue limit is the maximum value of repeated stress application to a material before it breaks. The higher the fatigue limit of a material is, the better it can withstand prolonged and repeated stress.
Fatigue is defined as the effect of repeated application of stress to the material. Testing for fatigue is important because its development on the material is more insidious. Before a material actually breaks, it may have less obvious signs of damage such as deformations or cracks. While usually not visible to the naked eye, these localized effects of stress and fatigue can grow larger with time, which can lead to the eventual destruction of the material. Fatigue can be influenced by multiple factors, such as the size, shape, and design of the component, and the level of stress it experiences regularly.
Young's Modulus testing is specifically designed for a material's Young's modulus, also known as the modulus of elasticity. It is defined as the change in rate of strain in a material as a function of stress. It can be referred to as the tensile modulus if measured relative to tensile testing.
This test is made to determine a material's behavior when an axial stretching load is applied. Young's modulus is commonly reported as N/mm2 or PSI (force per unit area), which means its value is similar to the amount of pressure applied to the object. Most tensile strength testing machines provide equipment that allow for Young's modulus testing.
Tensile strength is defined as a material's ability to resist forces that can cause it to deform or break. Also termed as "ultimate tensile strength", it is computed by dividing the peak force that the object is able to withstand with the cross sectional area of the material. In other words, the higher the force that an object can withstand with a given cross sectional area, the higher the tensile strength of the material is.
Tensile strength is tested using a machine called the tensile tester. A load cell is used with the materials tester to determine a specific material's tensile strength. During a tensile strength test, you can also test for other parameters such as the Young's modulus of elasticity, elongation, strain, and yield stress.
A materials tester can play such an important role in a number of industries. Getting the right tester is so important as it can make or break the quality of a particular product. In terms of price, there are many variables to consider when determining the possible price of a materials tester.
When shopping for a materials tester, the first question that you should ask yourself is what types of tests would you actually run. Most testers are capable of running different types of tests, so that can help. They can also have features such as data analysis software and preset testing settings that will make your testing life much easier. Most of the testing machines have features and settings that comply with most international standards. However, these machines can still be upgraded (at a cost) to run specific tests using specific materials.
One thing you should consider when getting a materials tester is to get an appropriate grip for the job. The type of grip you need depends on what material you?ll be testing and the types of tests that you will run. A standard grip is usually sufficient for most purposes, but there are some applications where going for a more customized grip is a must. Getting a grip with a purpose-made size, shape, and material is significantly more expensive than using a standard grip.
NextGen offers both Electromechanical and Servo-Hydraulic systems have various classifications. Depending on the tensile testing machine?s class the unit can either be a bench top or floor standing model. The higher the class, the more complex are the testing capabilities.
For example, most all Electromechanical tensile testing systems are plug-n-play units This means that a customer can order the unit and install it themselves upon delivery with the help of our training and installation video and the operational manual. On the other hand, the Servo-hydraulic tensile testing systems and dynamic tensile testing options are more complex solutions that require formal training and installation.
If training is required, there are a number of options for the customer:
Option 1:
Training and Installation Video - the customer may request a training and installation video to follow in order to set up the tensile tester.
Option 2:
Remote Session - customer may request a remote session which will be offered at no additional fee.
Option 3:
Physical training and installation - this is always an option and can be quoted upon request. The prices for training and installation range depending on the number of training days and customer?s location.
NextGen offers a variety of standard and specialty tensile grips and fixtures that can withstand temperatures up to 1050 degrees Celsius. Provided your materials can withstand the assigned temperature, you can rest assured that the grips will provide you with accurate readings every time.
As long as you are purchasing a tensile testing system that is compatible with the high temperature furnace upgrade, you will be able to acquire the furnace at a later date. Our engineering team will be able to help offer physical or remote support to help you with the process.