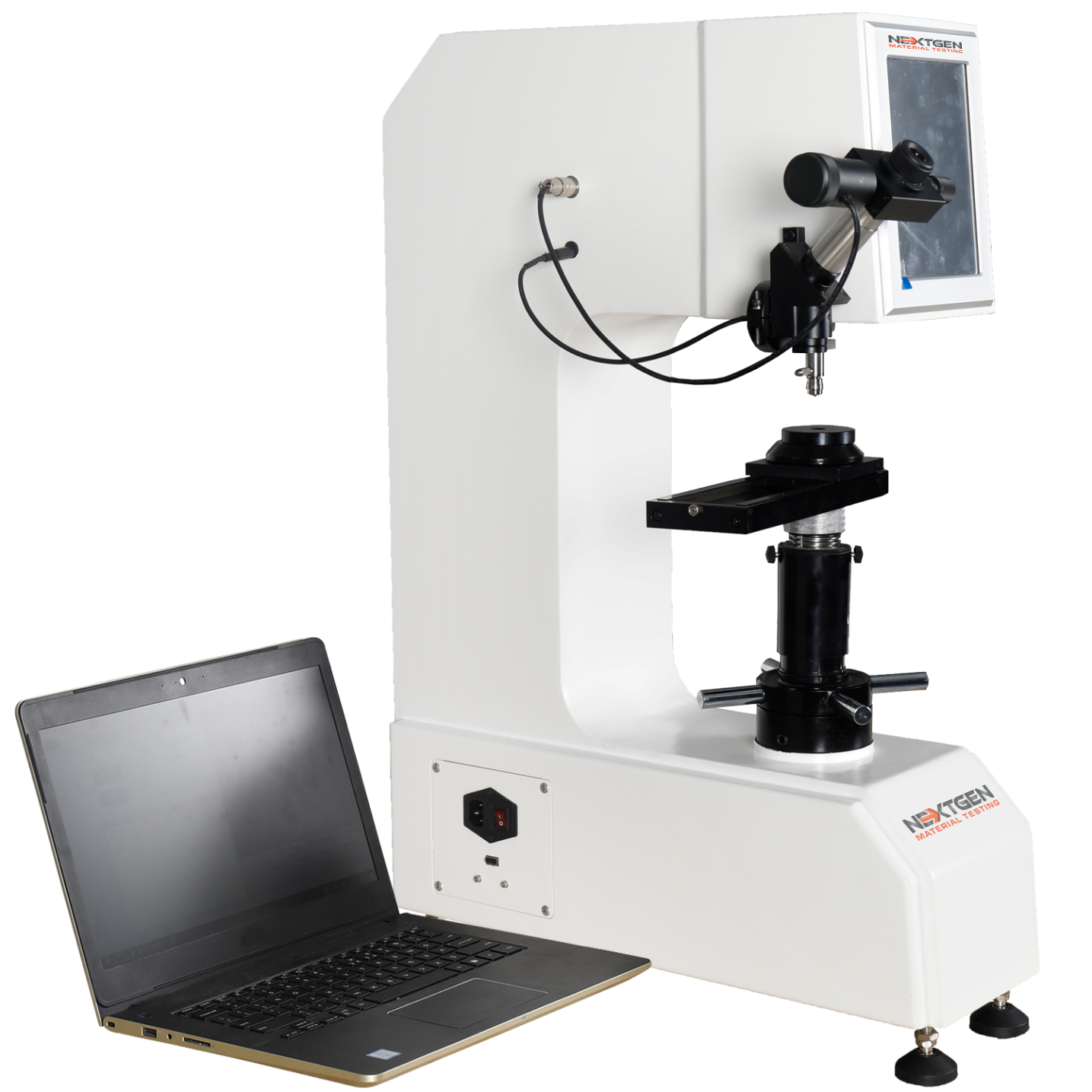
EN ISO 6508, ISO 6506, ASTM E92, ISO 6507, ASTM E-18, JIS Z2245, GB/T 230.2, ASTM E10-12, JIS Z2243, GB/T 231.2, JIS Z2244, GB/T 4340.2
NextGen's UniGen is a versatile all-in-one Universal Hardness Testing System. The unit is specifically designed to offer industry leading user-friendliness combined with a robust built for accurate and repeatable Vickers/Knoop, Rockwell and Brinell Hardness testing measurement results. The unit comes standard with an 8" LCD touch screen, CCD Camera, state-of-art automatic measuring software, and the full scope of NIST Certified consumables for all 3 testing methods, providing the ultimate Turnkey Solution for your facilities hardness testing requirements. Read more in our MEGA BLOG!
Universal Hardness Testing System - UniGen Series | |
---|---|
Brinell Scale | HBW1/5, HBW2.5/6.25, HBW1/10, HBW2.5/15.625, HBW1/30, HBW2.5/31.25, HBW2.5/62.5, HBW10/100, HBW5/125, HBW2.5/187.5 |
Rockwell Scales | HRA, HRB, HRC, HRD, HRE, HRF, HRG, HRH, HRK, HRL, HRM, HRP, HRR, HRS, HRV |
Vickers Scale | HV5, HV10, HV20, HV30, HV40, HV50, HV60, HV80, HV100, HV120 |
Test force | Rockwell: 60kgf(588N), 100kgf(980N), 150kgf(1471N); Initial test force:10kgf(98N); Brinell: 5kgf(49N), 6.25kgf(61.25N), 10kgf(98N), 15.625kgf(153.125N), 30kgf(294N), 31.25kgf(306.25N), 62.5kgf(612.5N), 100kgf(980N), 125kgf(1225N), 187.5kgf(1837.5N) Vickers: 5kgf(49N), 10kgf(98N), 20kgf(196N), 30kgf(294N), 40kgf(392N), 50kgf(490N), 60kgf(588N), 80kgf(784N), 100kgf(980N), 120kgf(1176N) |
Indication accuracy | Brinell: 8-650HB (δ/%):±2.5; Rockwell: ±0.1HR; Vickers: ±2 |
Repeatability | Brinell: 8-650HB (Hcf/%):≤3.0; Rockwell: 0.5HR; Vickers: ≤2.5 |
Hardness range | Brinell: 8-650HBW; Rockwell: 20-100HR; Vickers: 8-2900HV |
Force error | <0.5% |
Holding Time | 0-60s |
Minimum measuring unit | 0.1μm |
Allowed maximum sample size (test space) | Vertical: 220mm (for Rockwell); 150mm (for Vickers & Brinell test mode); Horizontal: 200mm |
Magnification | Eyepiece: 15X, 2.5X (for Brinell), 5X (for Vickers) (10X, 20X for optional) Total magnification: 37.5X, 75X |
Hardness read | Touch Screen LCD display, USB Flash Disk |
Power supply | AC220V, 50-60Hz |
Implementation of the standards | ISO 6508,ASTM E-18,JIS Z2245,GB/T 230.2 ISO 6506,ASTM E10-12,JIS Z2243,GB/T 231.2 ISO 6507,ASTM E92,JIS Z2244,GB/T 4340.2 |
Dimensions | Machine size: 22x13.8x31.5-inches / 560x350x800mm Packing size: 28.75x17.7x35.8-inches / 730x450x910mm |
Weight | N/W: 155lbs / 70kg G/W: 219lbs / 99kg |
Part Name | Quantity | Name | Quantity |
15X eyepiece | 1 | Brinell indenter diameter of 2.5mm, 5mm, carbide ball | 1 each |
Vickers Indenter | 1 | Rockwell 1.588 carbide ball indenter | 1 |
Rockwell Diamond indenter (NIST Certified) | 1 | Objective Lens 2.5 x, 5x | 1 each |
Hardness block Vickers x1, Rockwell x3, and Brinell x2 |
5pcs | Exterior lighting | 1 |
Power line | 1 | Large, medium, V-test sets | 1 each |
Sliding test sets | 1 | U disk (with an operations manual) | 1 |
Fuse 2A | 2 | Adjustable level screws | 4 |
Dust proof cover | 1 | Accessory Box | 1 |
Data protection is crucial because it shields an organization's information against fraud, hacking, phishing, and identity theft. Any firm that wants to operate efficiently must create a data protection plan to secure the security of its information. The significance of data protection grows along with the amount of data being created and stored. Cyberattacks and data breaches can have catastrophic consequences. Organizations must proactively safeguard their data and frequently upgrade their security protocols.
In the end, securing and protecting data from various risks and under various conditions is the fundamental premise and significance of data protection.
The preservation and accessibility of data are the guiding principles of data protection. Both the operational backup of data and business continuity/disaster recovery is referred to as data protection (BCDR)
NextGen’s Universal Hardness Tester for Vickers / Knoop, Rockwell and Brinell has Password protection for setup parameters which allows you to keep your information safe.
You can click here if you'd like to obtain a personal quote.
As in almost everything in this world, there are advantages and disadvantages of things. For example, in the Brinell test, there are the following disadvantages:
There is also Allowed maximum sample size (test space), which is Vertical: 220mm (for Rockwell); 150mm (for Vickers & Brinell test mode); Horizontal: 200mm for NextGen’s Universal Hardness Tester for Vickers / Knoop, Rockwell and Brinell.
You can click here if you'd like to obtain a personal quote.
The size of the indentation of the indenter leaves is measured in the optical Brinell hardness test. The Brinell method uses a spherical indenter, in contrast to the similarly optical Vickers method, which presses a pyramid-shaped indenter into a specimen.
The Brinell indenter, using a predetermined ball diameter and a defined test force, leaves an indentation in the surface of a workpiece (specimen), and the greater the indentation, the softer the material being tested.
According to ISO 6506, a spherical, hard metal (tungsten carbide) indenter is pressed into a specimen (workpiece) with a specified test load to determine the Brinell hardness (HBW) (between 1 kgf and 3000 kgf).
The surface area of the residual indent on the specimen (the projection of the indent) after the test force is withdrawn the Brinell hardness (HBW), which is determined by the product of the applied test force (F in newtons (N)) and the surface area (see formula below). Because the base area of Brinell indents is frequently not perfectly round, the surface area of the residual spherical indentation is calculated using the arithmetic mean (d) of the two perpendicular diagonals (d1 and d2 in mm).
NextGen’s Universal Hardness Tester for Vickers / Knoop, Rockwell and Brinell has the holding / dwell time of 0-60s.
You can click here if you'd like to obtain a personal quote.
Magnification is a significant factor in an optical microscope's performance. What does magnification mean exactly? The ratio between the size of a particular feature of an item or sample as shown in an image created by an optical system and the actual size of the feature on the object itself is a simple definition of magnification. A microscope's ability to produce a picture of an object at a scale that is larger (or even smaller) than its real size is known as magnification.
Only when it is feasible to discern more details of an object in the image than when observing the object with the unaided eye can magnification serve a beneficial purpose. Magnification is currently clearly visible while looking at an image of a sample through a microscope's eyepieces. There are recorded strict international norms for this situation. While many of these guidelines also apply to digital microscopy, where the image is frequently viewed on an electronic monitor, strict definitions and guidelines for the magnification achieved by a digital microscope have just recently been established.
NextGen’s Universal Hardness Tester for Vickers / Knoop, Rockwell and Brinell has the following magnification: Eyepiece: 15X, 2.5X (for Brinell), 5X (for Vickers) (10X, 20X for optional)
Total magnification: 37.5X, 75X.
You can click here if you'd like to obtain a personal quote.
The Vickers test has demonstrated overall respectable performance throughout the past 90 years in a wide range of applications, some of which the creators never even considered. The Vickers hardness test has limits, much like every other test method. The Vickers test has a speed restriction. Most international test procedures have time constraints in place to ensure repeatable results. Additionally, it is usually necessary to prepare the surface in some way so that it is easy to see the diagonal lengths needed to compute the area. Most crucially, the test method's definition requires the operator to "read" the diagonals, which leaves potential for error.
The operator must measure the horizontal and vertical diagonals for each indentation they make. This places the burden of accurate measurement on the measurer. Poor measuring practices will produce poor results, regardless of how accurate the tester is. Numerous attempts have been made to automate the measurement procedure in an effort to reduce the possibility of human mistakes.
NextGen’s Universal Hardness Tester for Vickers / Knoop, Rockwell and Brinell Vickers Repeatability is ≤2.5
You can click here if you'd like to obtain a personal quote.
A GR&R study is a useful indicator of the tester's accuracy and the amount of variation the tester may be introducing into the process when performing Rockwell hardness testing. Even though GR&R evaluations in Rockwell testing are not always possible, once these issues are recognized and taken into account, GR&R assessment offers helpful process information. It is relatively simple and error-free to assess the GR&R performance of many different types of gauges, such as micrometres and callipers (using a gauge block of a known value to make repeated measurements on the same block and calculating the repeatability).
A GR&R examination on a Rockwell tester, however, presents unique challenges. For instance, a major barrier is the variance in the test sample because a Rockwell test is never conducted in the same area. As a result, a variation is introduced because no material has hardness that is fully uniform.
NextGen’s Universal Hardness Tester for Vickers / Knoop, Rockwell and Brinell has the Rockwell repeatability of 0.5HR.
You can click here if you'd like to obtain a personal quote.
An empirical indentation hardness test that can reveal important details about metallic materials is the Brinell hardness test. This knowledge could be connected to tensile strength, wear resistance, ductility, and other physical properties of metallic materials, and it could be helpful for material selection and quality control.
An indentation hardness test involves pressing a tungsten carbide ball with a specific diameter into the surface of the material being tested using a piece of reliable equipment. After the force has been released, the diameter of the resulting indentation is measured. The Brinell indentation hardness test operates on a two-step basic premise.
The percent range of diameter values of n indentations made on a standard test block as part of a performance verification, relative to the average of the n measured diameter values, is used to estimate the repeatability R in the performance of a Brinell hardness machine at each hardness level, under the specific verification conditions.
NextGen’s Universal Hardness Tester for Vickers / Knoop, Rockwell and Brinell Brinell repeatability is 8-650HB (Hcf/%):≤3.0.
You can click here if you'd like to obtain a personal quote.
The Vickers hardness test, an optical procedure, measures the size of the diagonal impression that the indenter leaves behind. On the other hand, depth measurement techniques measure the depth of indentation created by the indenter (only Rockwell is standardized). According to ISO 6507, the pyramid-shaped indenter (with an interfacial angle of 136°) is pressed into a specimen (workpiece) with a predetermined test load starting at 1 gf in order to ascertain the Vickers hardness (HV).
The surface area of the residual indent on the specimen and the test force (F in newtons N) is divided to get the Vickers hardness (HV) (see formula below). Because the base area of Vickers indents is typically not square, the surface area of the remaining pyramidal indentation is calculated using the average of the two diagonals (d1 and d2 in mm).
The standard contains the suggested Vickers hardness range (ISO 6507). The Vickers hardness value ranges from 1 to 3.000 HV, depending on the test force and specimen material employed.
The Vickers hardness range for NextGen’s Universal Hardness Tester for Vickers / Knoop, Rockwell and Brinell is 8-2900HV.
You can click here if you'd like to obtain a personal quote.
The Rockwell hardness scale is used by all companies that produce steel products in America. No matter if the product is a ball bearing or a knife blade, the RC scale is the industry standard. Two experts in the field recommend Rockwell testing and how to carry them out. Manufacturers of steel products mention:
Rockwell Hardness and Rockwell Superficial Hardness of Metallic Materials: American Standard Test Method (ASTM E 18 Metals)
International Standards Organization - Test Method for the Rockwell Hardness Test, Part 1 (ISO 6508-1 Metallic Materials)The Rockwell hardness scale is used by all steel product makers because it enables standard reporting of test results. The Rockwell hardness scale is widely recognized in the steel industry. They can immediately determine the steel's strength by looking at its Rockwell rating. The Rockwell system is universally accepted as a hardness baseline. That's particularly so in knife blade manufacturing.
The Rockwell hardness range for NextGen’s Universal Hardness Tester for Vickers / Knoop, Rockwell and Brinell is 20-100HR.
You can click here if you'd like to obtain a personal quote.
A common technique to assess a material's resistance to deformation, bending, scratching, abrasion, or cutting is hardness testing. It provides a useful perspective on the capabilities, strength, adaptability, durability, and range of materials and components. They might be anything from unfinished products to raw resources. Hardness testing is one of the materials testing procedures used in the production environment for quality control and component acceptability.
The hardness of a material can currently be tested using a number of conventional methods. They consist of diamond-based surface testing or scratch tests.
Brilliance Hardness It is easier to compute the tensile strength of a material when its calculated Brinell Hardness Number is utilized in conjunction with the constant values used for that material. Since the indentation is seen under a microscope, the findings are exceedingly precise and trustworthy.
NextGen’s Brinell hardness range for Universal Hardness Tester for Vickers / Knoop, Rockwell and Brinell is 8-650HBW.
You can click here if you'd like to obtain a personal quote.
The SI-derived unit for electric potential, electric potential difference (voltage), and electromotive force is the volt (symbol: V). When an electric current of one ampere wastes one watt of power between two locations on a conducting wire, that potential is known as one volt. Equivalently, one joule of energy will be transferred for every coulomb of charge that passes across the difference in potential between two places.
220V is a certain electrical potential from a power source, or to put it another way, and it's the amount of force applied to get electrons to flow through an electrical connection. The common household voltage in a large number of nations is 220V.
NextGen's UniGen is a versatile all-in-one Universal Hardness Testing System. The unit is specifically designed to offer industry-leading user-friendliness combined with a robust built for accurate and repeatable Vickers/Knoop, Rockwell and Brinell Hardness testing measurement results.
Our Universal Hardness Tester for Vickers / Knoop, Rockwell and Brinell has a power supply of AC220V, 50-60Hz.
If you want a personalized quote, you can click here.
The UniGen from NextGen is a flexible, all-in-one system for testing universal hardness. Vickers/Knoop, Rockwell, and Brinell Hardness testing measurement findings are accurate and repeatable thanks to the unit's industry-leading user-friendliness and durable construction. The unit includes an 8" LCD touch screen, a CCD camera, cutting-edge automatic measuring software, and all of the consumables necessary for all three testing methods that are NIST Certified, making it the ideal Turnkey Solution for your facility's hardness testing needs.
Features:
NextGen’s Universal Hardness Tester for Vickers / Knoop, Rockwell and Brinell has the following weight and dimensions:
Dimensions |
Machine size: 22x13.8x31.5-inches / 560x350x800mm |
Weight |
N/W: 155lbs / 70kg |
If you want a personalized quote, you can click here.
NextGen’s Universal Hardness Tester for Vickers / Knoop, Rockwell and Brinell comply several different standards: ISO, ASTM, JIS, GB/T. Each one is designed to improve quality of the tester as well as set standard procedures and mechanisms for testing. For example, The ISO creates and disseminates standards for a wide variety of goods, components, and procedures. In the ISO Standards database, which is divided into several categories like healthcare technology, railway engineering, jewellery, clothes, metallurgy, weapons, paint, civil engineering, agricultural, and aircraft, the organization now has around 24,362 standards.
ASTM is an international standards organization called ASTM International, originally known as the American Society for Testing and Materials, creates and disseminates voluntary consensus technical standards for a variety of materials, goods, systems, and services. JIS is applicable to both stationary and portable hardness testing equipment, details the procedure for Rockwell regular hardness and Rockwell superficial hardness tests for metallic materials.
Our Universal Hardness Tester for Vickers / Knoop, Rockwell and Brinell comply the following standards ISO 6508, ASTM E-18,JIS Z2245,GB/T 230.2, ISO 6506,ASTM E10-12,JIS Z2243,GB/T 231.2, ISO 6507,ASTM E92,JIS Z2244,GB/T 4340.2
If you want a personalized quote, you can click here.
This Standard, which is applicable to both stationary and portable hardness testing equipment, details the procedure for Rockwell regular hardness and Rockwell superficial hardness tests for metallic materials. Tables 1 and 2 display the scales and the range of hardness.
Other requirements must be followed for some products and materials, such as hardmetals (for instance, ISO 3738-1 and ISO 4498).
It should be noted that according to ISO 6508-1, steel ball indenters are only permitted to be used in tests that adhere to Annex A and that the standard type of ball indenters for Rockwell regular hardness and Rockwell superficial hardness is tungsten carbide composite (hereafter referred to as hardmetal indenter balls).
At the time of the subsequent revision, this Standard will adopt hardmetal indenter balls as the standard indenter (see Table 1, Table 2, 5.2, 6.3 and Table E.1). Even in this situation, it is planned to conduct the test in accordance with Annex A using steel balls as the standard indenter.
To sum up, NextGen’s Universal Hardness Tester for Vickers / Knoop, Rockwell and Brinell implement JIS Z2245 Standard.
If you want a personalized quote, you can click here.
An international standards organization called ASTM International, originally known as the American Society for Testing and Materials, creates and disseminates voluntary consensus technical standards for a variety of materials, goods, systems, and services. There are currently 12,575 ASTM voluntary consensus standards in use worldwide. It is not the responsibility of ASTM International to demand or enforce adherence to its standards. The standards, however, might become obligatory if they are used in a contract or by a company, government, or other external entity.
The measurement of the amount of bending that happens when tensile and compressive pressures are applied to notched and unnotched test specimens during regular testing in the elastic range is covered by ASTM E1012. These techniques are particularly relevant to the typical tension, compression, creep, and uniaxial fatigue testing force levels. The main goal of this procedure is to measure the amount of bending that a test specimen is subjected to during routine tests by the regular parts that make up a materials testing machine.
Both metallic and nonmetallic testing can be done using this method.
NextGen’s Universal Hardness Tester for Vickers / Knoop, Rockwell and Brinell implement ASTM-E10-12 standard.
If you want a personalized quote, you can click here.
This specification relates to measuring metallic materials' Vickers hardness with an applied force ranging from 1 kgf to 120 kgf. The validation of the Vickers hardness testing devices is applicable to Part B. Furthermore, part C discusses the calibration of standardized test blocks. You can get all requirements from ASTM International.
The Routine test (with routine accuracy) and the Verification, Laboratory, or Referee test are two classes of standardized tests covered by this standard (with a much higher degree of accuracy required). The Referee Test is WMT&R's area of expertise.
A tiny diamond indenter with an apical angle of 136 degrees is used in the Vickers Hardness Test and is pressed into the test material at a specified load. The indentation that results is then gauged along both axes, tip to tip. A formula, or more frequently a chart based on the formula, is used to translate the average of the two axis measurements into a Vickers Hardness value. The largest load that may be applied to the specimen during the test will produce the most accurate findings. A greater indentation with better measurement resolution and, hence, more reliable data is produced by a higher load.
NextGen’s universal Hardness Tester for Vickers / Knoop, Rockwell and Brinell comply ASTM-E92 Standard.
If you want a personalized quote, you can click here.
The assessment of metallic materials' Rockwell hardness and Rockwell superficial hardness using the Rockwell indentation hardness principle is covered by ASTM-E18 Standard. The standard outlines the specifications for Rockwell hardness testing equipment as well as the steps to take when conducting these tests. The indenter ball sizes were stated in units of inches, while the force levels were specified in kilograms-force (kgf) (in.).
According to this standard, force is measured in Newtons (N), and length is measured in millimetres in accordance with the International System of Units (SI) (mm). However, force numbers in kgf units and ball diameters in inch units are supplied for information, and much of the discussion in this standard refers to these due to historical precedent and ongoing general usage. The test principles, testing procedures, and verification procedures are essentially identical for both the Rockwell and Rockwell superficial hardness tests.
NextGen's Universal Hardness Tester for Vickers / Knoop, Rockwell and Brinell comply ASTM E-18 Standard.
If you want a personalized quote, you can click here
For scales A, B, C, D, E, F, G, H, K, 15N, 30N, 45N, 15T, 30T, and 45T for metallic materials, ISO 6508 outlines the procedure and is applicable to both stationary and portable hardness testing devices.
Other specialized International Standards are applicable for particular materials and/or products (for instance, ISO 3738 1 and ISO 4498).
Principle: An indenter of specified size, shape, and material is forced into the surface of a test specimen under two force levels using the specific conditions defined in Clause 7. The specified preliminary force is applied, and the initial indentation depth is measured, followed by the application and removal of a specified additional force, returning to the preliminary force. The final indentation depths are then measured, and the Rockwell hardness value is derived from the difference, h, in the final and initial indentation depth and the two constants N and S as Rockwell Hardness = N-(h/s)
To answer your question – yes, NextGen’s Universal Hardness Tester for Vickers / Knoop, Rockwell and Brinell comply ISO 6508 Standard.
If you want a personalized quote, you can click here.
ISO 6507 specifies the Vickers hardness test method for the three different ranges of test force for metallic materials, including hardmetals and other cemented carbides.
Principle: A diamond indenter, in the form of a right pyramid with a square base and with a specified angle between opposite faces at the vertex, is forced into the surface of a test piece, followed by measure
The Vickers hardness is proportional to the quotient obtained by dividing the test force by the area of the sloped surface of indentation, which is assumed to be a right pyramid with a square base and having at the vertex the same angle as the indenter.
NOTE 1 A right pyramid has its apex aligned with the centre of the base.
NOTE 2 As applicable, this document has adopted hardness
To answer your question – yes, NextGen’s Universal Hardness Tester for Vickers / Knoop, Rockwell and Brinell comply ISO 6507 Standard.
If you want a personalized quote, you can click here.
The ISO creates and disseminates standards for a wide variety of goods, components, and procedures. In the ISO Standards database, which is divided into several categories like healthcare technology, railway engineering, jewellery, clothes, metallurgy, weapons, paint, civil engineering, agricultural, and aircraft, the organization now has around 24,362 standards. The ISO also publishes technical reports, technical specifications, publicly available specifications, technical corrigenda, and guides in addition to standards. Experts in related fields from around the world have agreed on the ISO standards. These are individuals—manufacturers, sellers, purchasers, customers, trade groups, users, or regulators—who are aware of the needs of their respective sectors. The Brinell hardness test for metallic materials is outlined in ISO 6506.
It is applicable to both fixed location and portable hardness testing machines.
For some specific materials and/or products, particular International Standards exist (e.g. ISO 4498) and make reference to this International Standard.
NextGen’s Universal Hardness Tester for Vickers / Knoop, Rockwell and Brinell comply ISO 6506 Standard
If you want a personalized quote, you can click here.
Hardness is the measure of a material’s resistance to localised permanent deformation. Permanent deformation is also called plastic deformation. While elastic deformation means that a material changes its shape only during the application of force, a resulting plastic deformation means that the material will not return to its original shape.
Materials behave differently under different types of loading. For example, a metal that can take a huge one time impact extremely well may not act the same during continuous loading.
Hardness testing must be carried out for each case so that a well-informed choice can be made for the application.
The three types of hardness are scratch, rebound, and indentation hardness. Measuring each type of hardness requires a different set of tools. Also, the same material will have different hardness values for each of the above-mentioned types.
The commonly used units for hardness measurement are:
The minimum measuring unit of NextGen’s Universal Hardness Tester for Vickers / Knoop, Rockwell and Brinell is 0.1μm.
If you want a personalized quote, you can click here.
Accuracy, repeatability, and correlation issues with Universal Vickers / Knoop, Rockwell and Brinell Hardness testing may often be divided into three categories and linked to five fundamental causes: the machine, the operator, and the environment, sample preparation, and calibration. It's crucial to clarify the issues before talking about the causes:
Accuracy: The instrument's capacity to read linearly on certified test blocks, which are accepted hardness standards, and its capacity to transfer this accuracy to test specimens.
Repeatability: The instrument's capacity to reproduce its findings when applied to accepted hardness standards.
Correlation: The ability of an instrument to generate results that are comparable to those obtained by another instrument that has been "fully calibrated"; or the capacity of two operators to measure the same impression with the same equipment and produce comparable findings.
The force error of our Universal Hardness Tester for Vickers / Knoop, Rockwell, and Brinell is just <0.5%.
If you want a personalized quote, you can click here.
NextGen's universal Hardness Tester for Vickers / Knoop, Rockwell and Brinell unit comes standard with an 8" LCD touch screen, CCD Camera, state-of-art automatic measuring software, and the full scope of NIST Certified consumables for all 3 testing methods, providing the ultimate Turnkey Solution for your facilities hardness testing requirements.
On top of that, the following accessories are also included as the standard package for our Universal Hardness Tester for Vickers / Knoop, Rockwell and Brinell:
Part Name |
Quantity |
Name |
Quantity |
15X eyepiece |
1 |
Brinell indenter diameter of 2.5mm, 5mm, carbide ball |
1 each |
Vickers Indenter |
1 |
Rockwell 1.588 carbide ball indenter |
1 |
Rockwell Diamond indenter (NIST Certified) |
1 |
Objective Lens 2.5 x, 5x |
1 each |
Hardness block |
5pcs |
Exterior lighting |
1 |
Power line |
1 |
Large, medium, V-test sets |
1 each |
Sliding test sets |
1 |
U disk (with an operations manual) |
1 |
Fuse 2A |
2 |
Adjustable level screws |
4 |
Dust proof cover |
1 |
Accessory Box |
1 |
You can click here if you'd like to obtain a personal quote.
NextGen's UniGen is a versatile all-in-one Universal Hardness Testing System. The unit is specifically designed to offer industry leading user-friendliness combined with a robust built for accurate and repeatable Vickers/Knoop, Rockwell and Brinell Hardness testing measurement results.
The main features of our Universal Hardness Tester for Vickers / Knoop, Rockwell and Brinell are:
If you are looking to obtain a personalised quote, click here.
The Vickers hardness test method entails pressing a diamond indenter in the shape of a right pyramid with a square base and an angle of 136 degrees between opposed faces while applying stress ranging from 1 to 100 kgf on the test material. Typically, the entire load is applied for 10 to 15 seconds. Using a microscope, the two diagonals of the indentation left on the material's surface after the load has been removed are measured, and their average is computed.
Calculations are used to determine the size of the indentation's sloping surface. The result of dividing the kgf weight by the square millimetre area of the indentation is the Vickers hardness. The Vickers machine, a floor-standing instrument that costs more than the Brinell or Rockwell machines, is incredibly versatile and precise for testing the softest and hardest of materials under varied loads.
The following Vickers Test Force can be applied in Universal Hardness Tester for Vickers / Knoop, Rockwell and Brinell: 5kgf(49N), 10kgf(98N), 20kgf(196N), 30kgf(294N), 40kgf(392N), 50kgf(490N), 60kgf(588N), 80kgf(784N), 100kgf(980N), 120kgf(1176N)
You can click here if you'd like to obtain a personal quote.
The following standards define Brinell test procedures: ASTM E10 and ISO 6506. Just so you know, operators have a current copy of the relevant standards because they are frequently changed. To ensure that the metal's plastic flow has stopped, the time under load (dwell) duration is necessary. In some situations, balls with smaller diameters and lower forces are also employed.
The Brinell test uses a single test force, like the Knoop and Vickers tests. Following removal of the load, the recovered round impression is measured using a low-power microscope or an automatic measuring device across the indent at right angles, and the average value is used to determine hardness. Brinell hardness testing is typically used in testing aluminum and copper alloys (at lower forces) and steels and cast irons at the higher force ranges.
The following Brinell Test Force can be applied in Universal Hardness Tester for Vickers / Knoop, Rockwell and Brinell: 5kgf(49N), 6.25kgf(61.25N), 10kgf(98N), 15.625kgf(153.125N), 30kgf(294N), 31.25kgf(306.25N), 62.5kgf(612.5N), 100kgf(980N), 125kgf(1225N), 187.5kgf(1837.5N)
You can click here if you'd like to obtain a personal quote.
The Rockwell hardness test method, as properly defined in ASTM E-18 standards, is the most commonly used hardness test method among all the other methods. All metals can be tested using the Rockwell method, with the exception of those where too many changes would result from the test sample structure or surface characteristics, where the indentations might be too large, or where the sample size or shape might preclude its application.
The permanent depth of the indentation caused by a force or load on an indenter is measured using the Rockwell hardness testing method. With the use of a diamond or ball indenter, a preliminary test force (preload or small load) is first given to the sample. In order to lessen the impacts of surface polish, this preload penetrates the surface. It is feasible to determine the baseline depth of indentation by holding this first test force for a predetermined dwell duration.
The following Rockwell Test Force test force can be applied in Universal Hardness Tester for Vickers / Knoop, Rockwell and Brinell: 60kgf(588N), 100kgf(980N), 150kgf(1471N);
Initial test force:10kgf(98N).
You can click here if you'd like to obtain a personal quote.
Since the necessary calculations are independent of the indenter's size and the indenter may be used for any materials regardless of hardness, the Vickers test is frequently simpler to apply than other hardness tests. The fundamental idea, as with all conventional hardness measurements, is to look at a material's resistance to plastic deformation coming from a known source. All metals can be tested with the Vickers test, which also has one of the broadest scales of any hardness test.
The Vickers Pyramid Number (HV) or Diamond Pyramid Hardness is the term for the hardness measurement provided by the test (DPH). Although the hardness value can be expressed in pascals, pressure, which also employs the same units, should not be confused with it. The hardness number is determined by the load over the surface area of the indentation and not the area normal to the force and does therefore not pressure.
The following Vickers Scales are used in Universal Hardness Tester for Vickers / Knoop, Rockwell and Brinell: HV5, HV10, HV20, HV30, HV40, HV50, HV60, HV80, HV100, HV120
Click here if you would like to obtain a personal quote.
The Rockwell scale measures a material's resistance to indentation as a measure of hardness. The Rockwell test gauges how deeply an indenter penetrates a material under a heavy load (major load) in comparison to how deeply a preload penetrates (minor load). Different scales that employ various loads or indenters are identified by a single letter. The outcome is a dimensionless number denoted by the letters HRA, HRB, HRC, etc., where the last letter stands for the appropriate Rockwell scale. A minor load and a major load must be applied to a material in order to determine its Rockwell hardness.
The zero position is established by the minor load. The minor load is kept constant while the big load is applied and removed. A dial that measures the depth of penetration relative to the zero datum uses a harder material to get a lower reading. In other words, the hardness and penetration depth are inversely related. The main benefit of using Rockwell hardness is avoiding the time-consuming calculations required by other hardness assessment systems by simply displaying hardness values.
The following Rockwell Scales are used in Universal Hardness Tester for Vickers / Knoop, Rockwell and Brinell: HRA, HRB, HRC, HRD, HRE, HRF, HRG, HRH, HRK, HRL, HRM, HRP, HRR, HRS, HRV.
Click here if you would like to obtain a personal quote.
By measuring the depth of penetration of an indenter put onto a material test piece, the Brinell scale describes the indentation hardness of materials. In the field of materials science, there are various ways to define hardness. The standard test applies a force of 3,000 kgf (29.42 kN; 6,614 lbf) to a steel ball with a diameter of 10 mm (0.39 in) as the indenter. A smaller force is applied to softer materials, while a tungsten carbide ball is utilized in place of the steel ball for harder materials.
The conditions of the test that was used to determine the Brinell hardness number (BHN, or more often, HB) must be stated when quoting the number. The example "HBW 10/3000" illustrates how tests should be specified using the standard format.
The designation "HBW" denotes the use of a tungsten carbide ball indenter as opposed to "HBS," which denotes the use of a hardened steel ball. In millimetres, the "10" represents the ball's diameter. The number "3000" represents the force in kilograms.
The following Brinell Scales are used in Universal Hardness Tester for Vickers / Knoop, Rockwell and Brinell: HBW1/5, HBW2.5/6.25, HBW1/10, HBW2.5/15.625, HBW1/30, HBW2.5/31.25, HBW2.5/62.5, HBW10/100, HBW5/125, HBW2.5/187.5.
Click here if you would like to obtain a personal quote.