Are you looking for a reliable universal hardness tester that provides excellent material testing functionality? You have a lot of options to choose from, and one of your best choices is NextGen’sdigital universal hardness testing machine designed for different material testing applications.
NextGen Material Testing is a leading supplier of testing machines offering lifetime customer support and high-quality consumables and spares designed to support all your testing needs. Whether your requirement is Vickers, Rockwell, or Brinell tests, NextGen has all the spares and consumables for any of these types of material tests.
NextGen also supplies testing machines that conform to industry standards defined by the ISO and ASTM.
ASTM, ISO standards for the universal hardness testing machine
The universal hardness tester is easy to use so that you will not waste a lot of time, energy, and money training your technical staff in order to learn how to properly use it.
Below are specific ASTM and ISO standards satisfied by NextGen’s universal testing machines and the specific provisions for each.
The ISO 6506 outlines the method for Brinell hardness tests for metallic specimens. The test applies to portable and fixed Brinell hardness testing machines.
The testing machine should be able to apply a test force between 9,807 N and 29.42 KN, and the indenter ball must be made of a tungsten carbide composite.
The Brinell test must be carried out on an even and smooth surface free from foreign matters. The test specimen must have a thickness that is at least eight times the deepness of the indentation.
This method covers the determination of hardness tests of metallic materials via the Brinell hardness test principle. This standard provides the criteria for Brinell testing machines and the correct procedure for performing Brinell hardness tests.
Most commonly, the Brinell method is used to test materials with coarse surfaces with the coarseness that is too rough to be tested using another method. Examples of these materials are forgings and castings.
According to this standard, a Brinell test must use high test loads of 3,000 kgf or more. It also uses a 10-mm diameter indenter so that the resulting indentations average out more sub-surface and surface inconsistencies.
Typically, the source of error in Brinell tests is the measurement of the indentation. Results vary even under perfect testing conditions, and in less than perfect conditions, result variations can be very significant. Make sure that the test surface is prepared with a grinder to remove undesirable surface conditions.
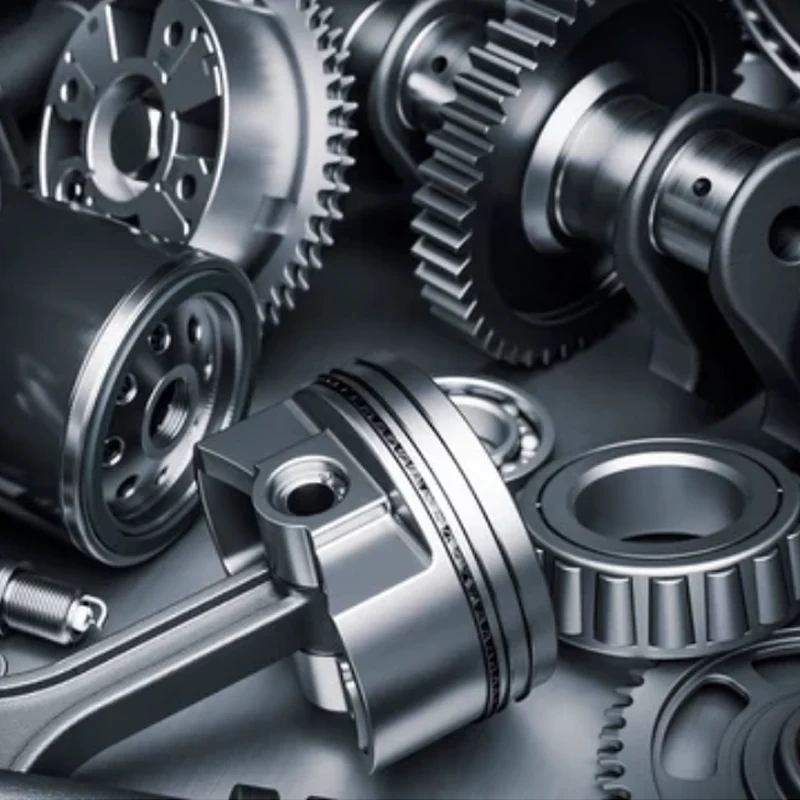
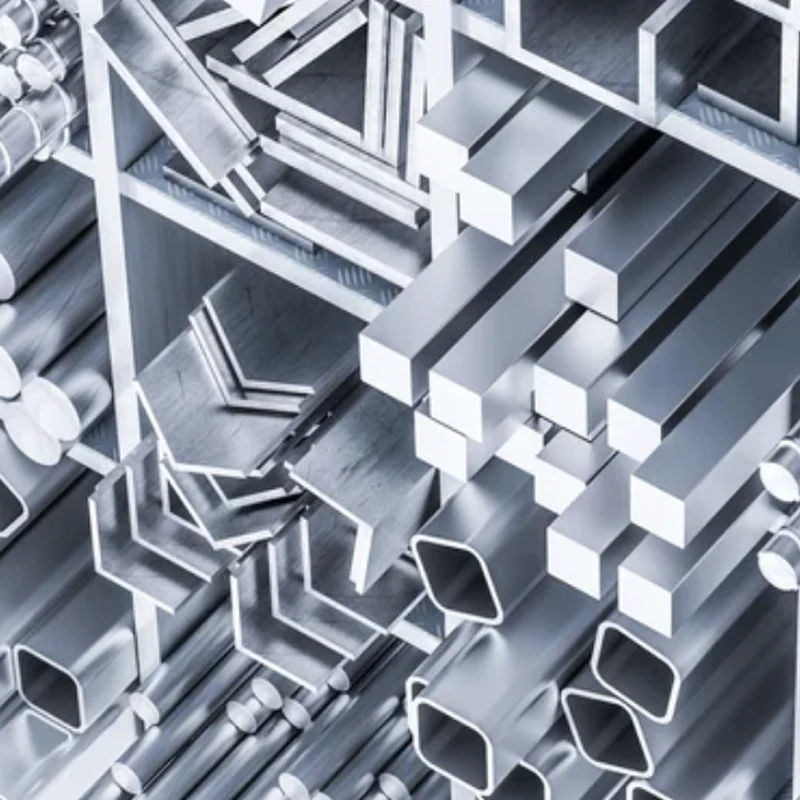
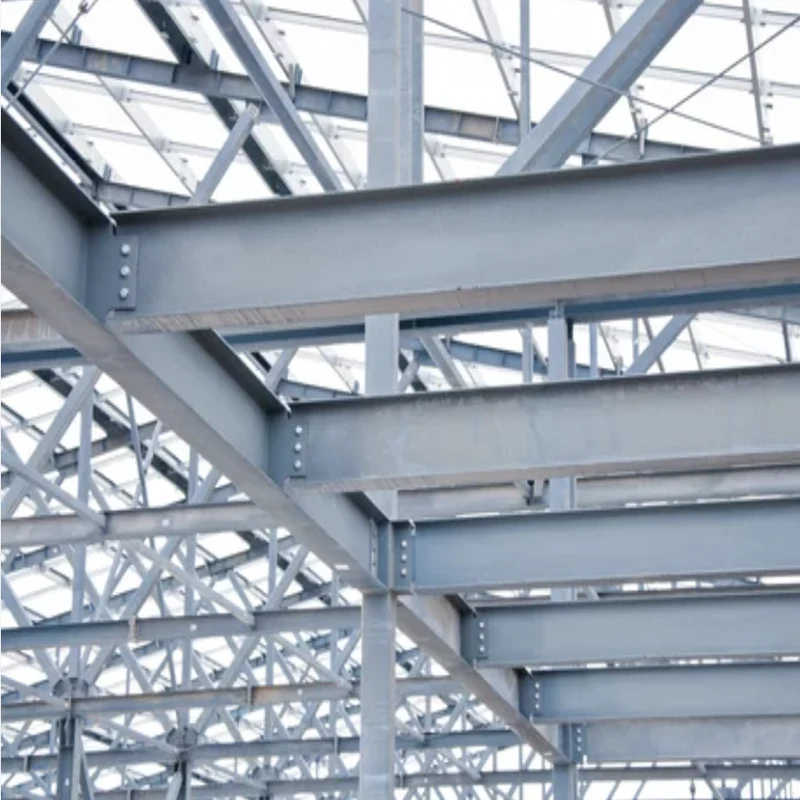
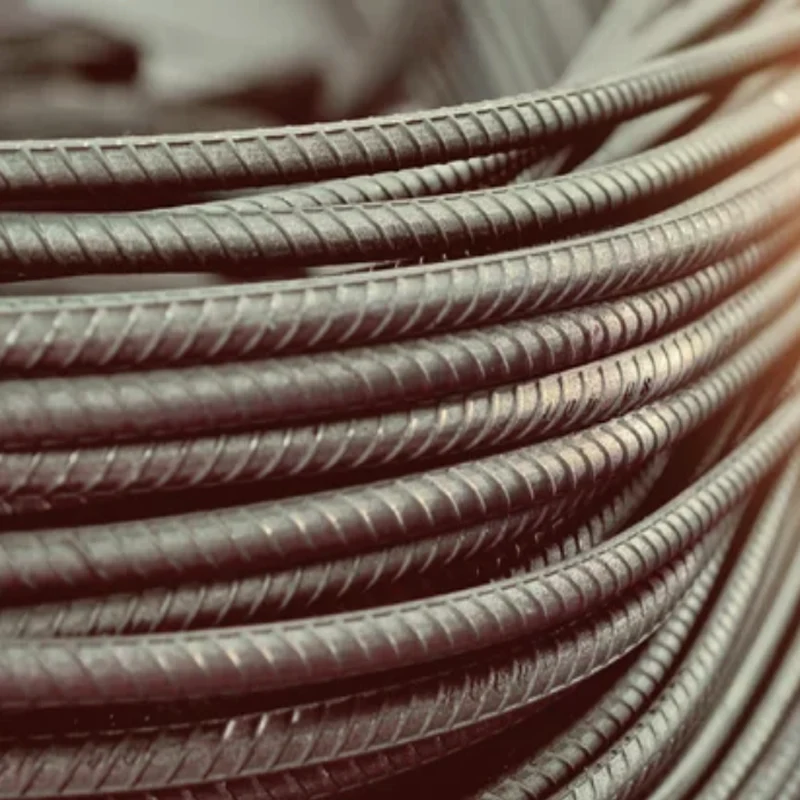
ISO 6507 specifies the conditions for the Vickers hardness tests. Specifically, it requires that indentation diagonals be between 0.020 and 1,400 mm and the indenter should be pyramidal in shape with a square base. If the test piece is a hard metal sample, the layer that must be removed from it must be greater than 0.2 mm.
The ISO 6507 standard also specifies the thickness of the test piece, which should not be lower than 1.5 times the indentation’s diagonal length. The application of the test force must be perpendicular to the test piece and applied without shock, overload, or vibration.
The ASTM E92 standard covers the requirements for the Vickers hardness test and the procedures for performing this test. The standard also applies to the Knoop hardness test.
The Vickers hardness test is a test created to test the hardness of materials with thin sections and small parts. The test uses a diamond indenter and light loads to create an indentation on the sample under testing. The smaller the indentation that is created, the harder is the material.
The Vickers hardness test is used in many industries to know the right type of material to use in their pieces of machinery and operations. The material with the right hardness is chosen based on the intended purpose.
This test method makes use of forces ranging from 1 gf to 120 kgf.
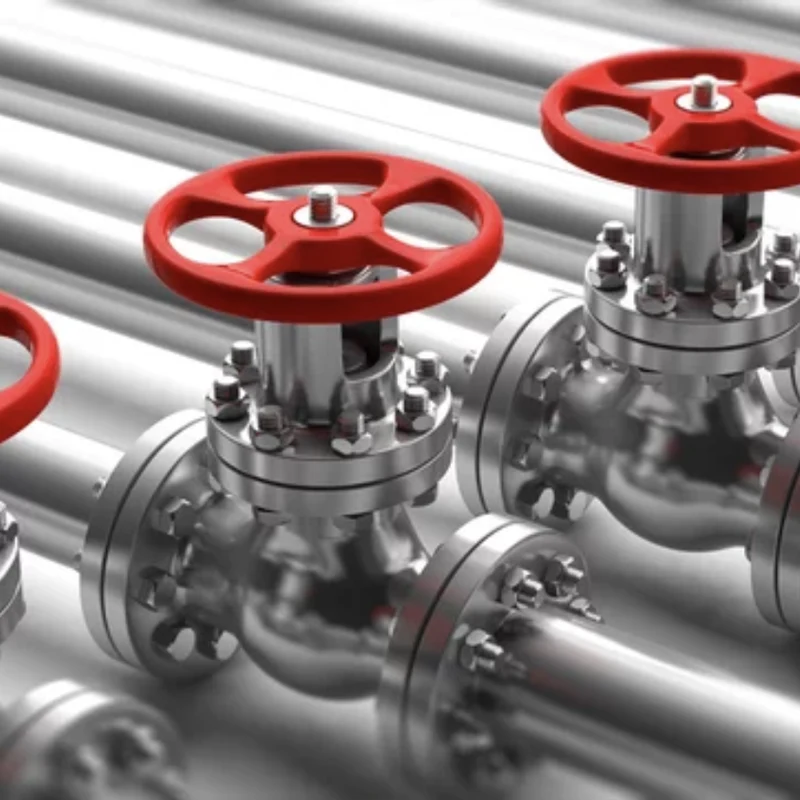
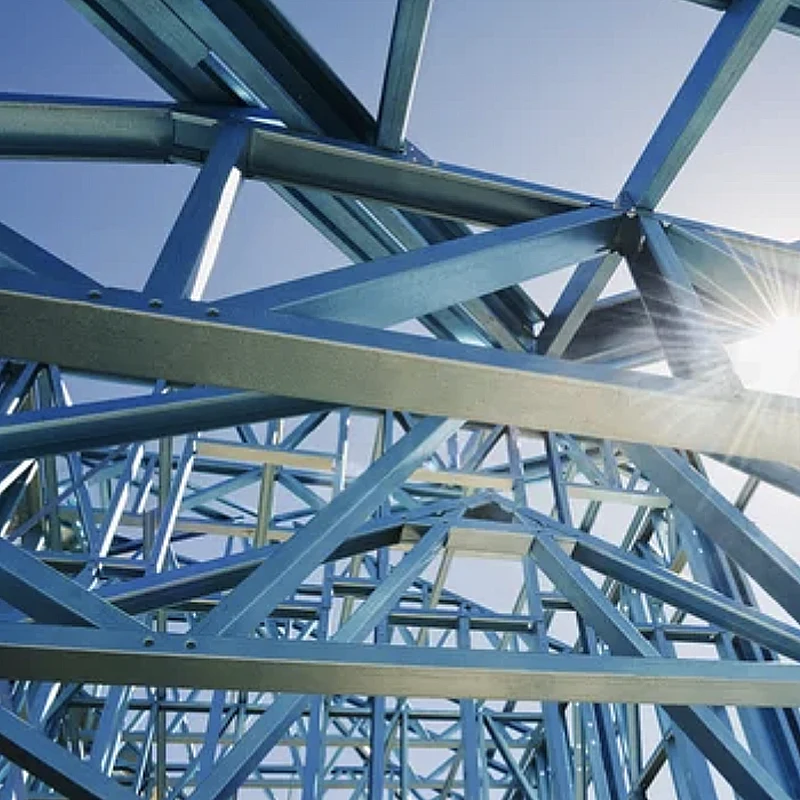
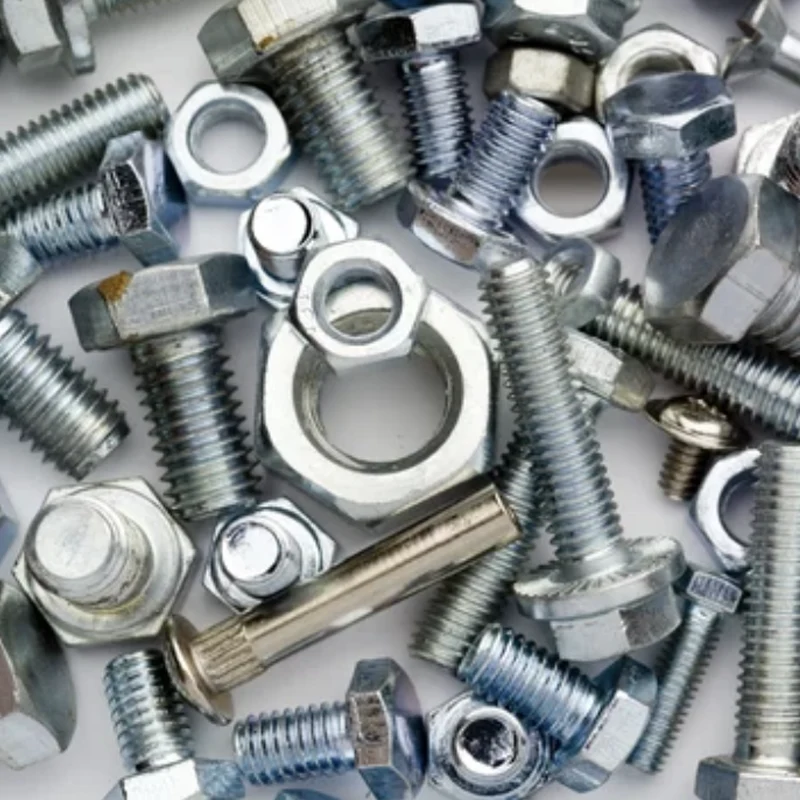
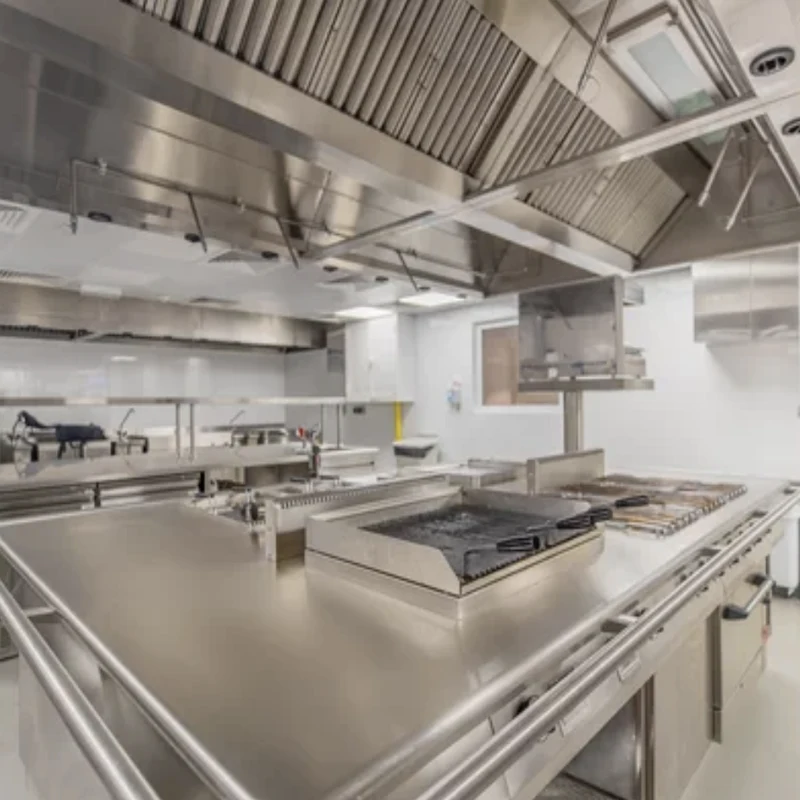
The ISO 6508 standard applies to Rockwell hardness tests. The Rockwell hardness is a scale based on the penetration depth of the indenter under a large load.
Rockwell hardness testing does not provide a direct measurement of performance properties. However, the hardness of materials correlates directly with other properties, such as the material’s wear resistance and strength.
Rockwell hardness testing is used for material evaluation because of its low cost and simplicity. The indenter for this test is shaped like a cone and has a tip that is spherical in shape. The loads used to cause the indentation in Rockwell hardness tests are available in six variations:
- 15 kgf
- 30 kgf
- 45 kgf
- 60 kgf
- 100 kgf
- 150 kgf
ASTM E18 also refers to the standards that govern proper Rockwell hardness tests. According to this standard, the Rockwell test is an indentation hardness test that uses a verified machine to push a diamond sphere-conical indenter or tungsten carbide ball indenter into the surface of metallic materials.
Formerly, the use of steel balls as the indenting component was the standard, but the NSTI changed it into tungsten carbide balls. This change is expected to improve results because steel balls tend to flatten after a long time of being used.
Note that if the device uses a steel ball to test, the result must indicate a hardness value with the inclusion of the letter S. If the indenter is a tungsten carbide ball, the result must be accompanied by the letter W.
Rockwell hardness tests that use these two different types of indenting components produce different results. When using a tungsten carbide ball indenter, the result is always one Rockwell point lower than when a steel ball is used.
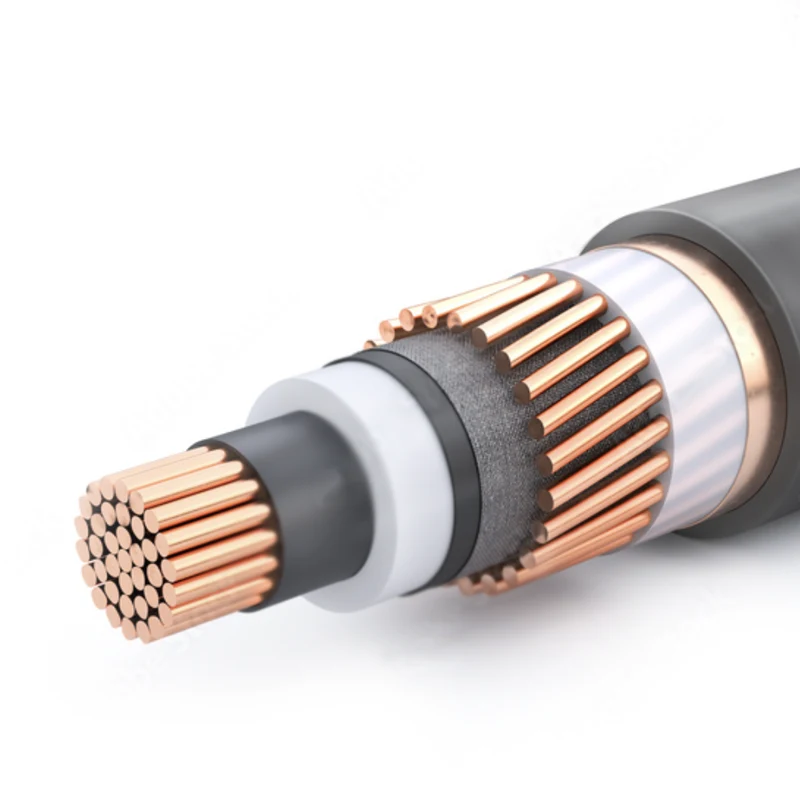
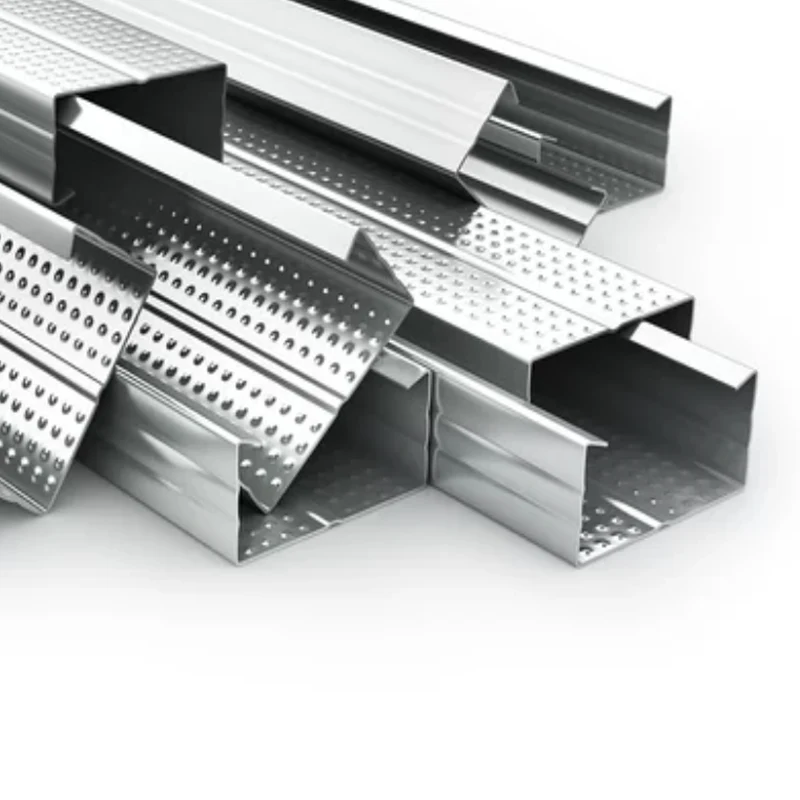
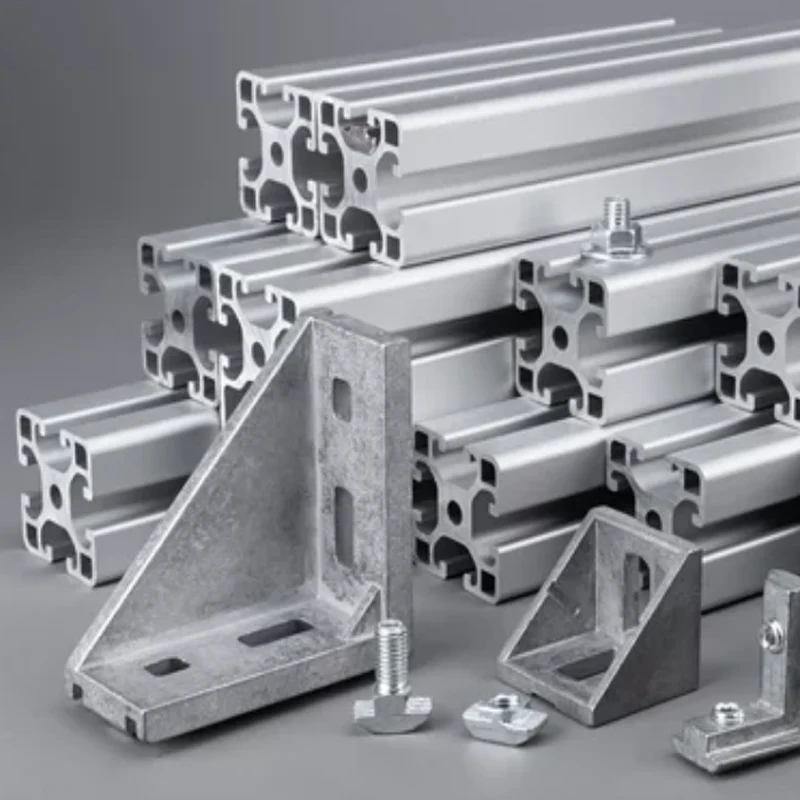
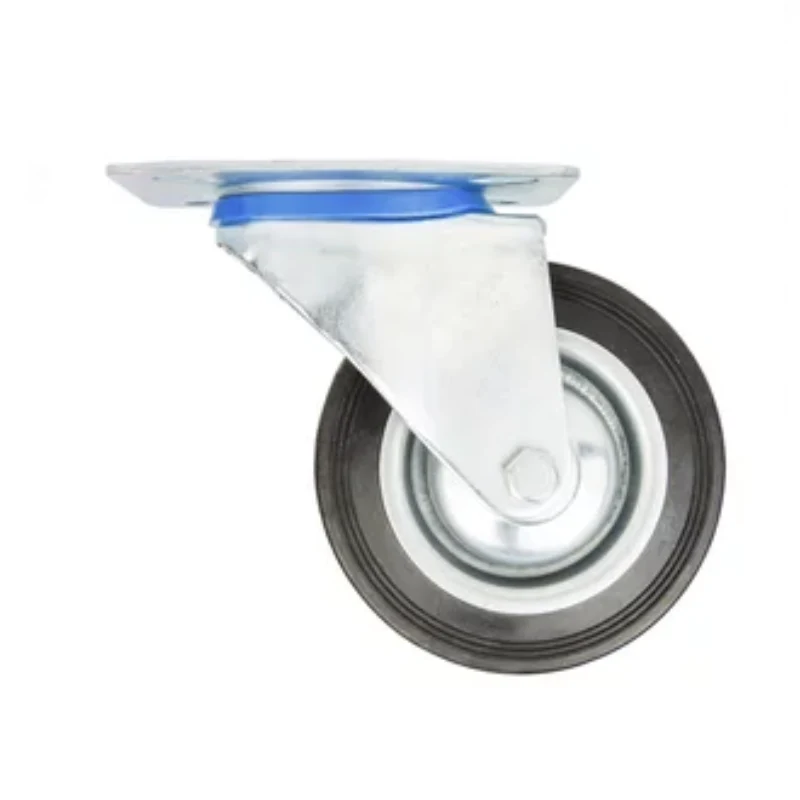
All test standards mentioned in this post do not purport to safety concerns associated with their use. The responsibility of establishing fitting safety and health practices falls on the user of these standards.
12 excellent reasons to buy the universal hardness tester for Vickers, Rockwell and Brinell testing needs
Why should you buy the hardness universal tested from NextGen? Below are compelling reasons why:
1. Combined test methods in one unit
A great advantage for testing labs is the combination of different test methods in just one unit of universal hardness tester. The combined system allows for cost and space savings, user-friendliness, and flexibility.
NextGen offers the best-selling load-cell and closed-loop systems for hardness testers with tests covering Rockwell, Brinell, and Vickers methods. Compared with the dead weight types of hardness testers, the universal hardness tester features a closed-loop system, allowing it to offer unmatched flexibility, stability, and reliability.
The NextGen universal hardness tester is applicable in situations where:
- It is necessary to understand the tendency of your material to resist wear and deformation.
- It is suitable for testing metal, composites, organic solids, plastics, and other solid materials.
- The test needs an indenter that can suitably perform external and internal hardness tests on test pieces, including pipes, rings, gears, and other objects with cavities.
- The laboratory or the manufacturer handles a wide range of materials to test.
While most hardness testers measure only one kind of scale, universal testers cover a wider range of measurement methods and test loads. It is convenient for you because you do not change the setup for simple testing with a different method. It is also cost-effective for your business, as you do not need to purchase many testers and have them all calibrated and maintained.
2. Hardness testing device that conforms to the ASTM and ISO standards
The universal hardness tester by NextGen does not only conform to the ISO and ASTM standards that state the acceptable conditions for testing materials under the different types of testing methods.
This hardness tester also conforms to other standards, namely:
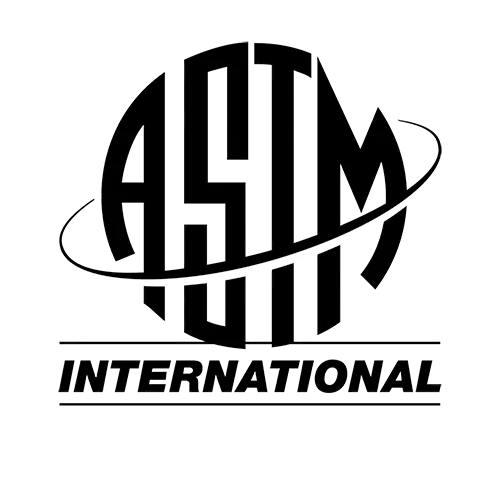
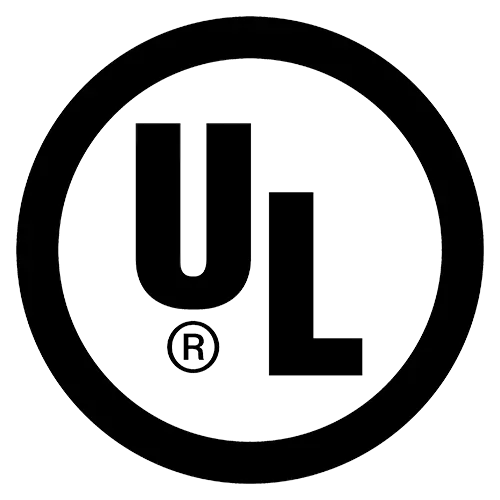
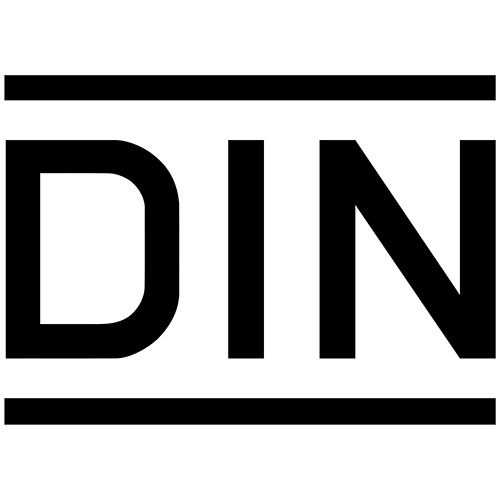
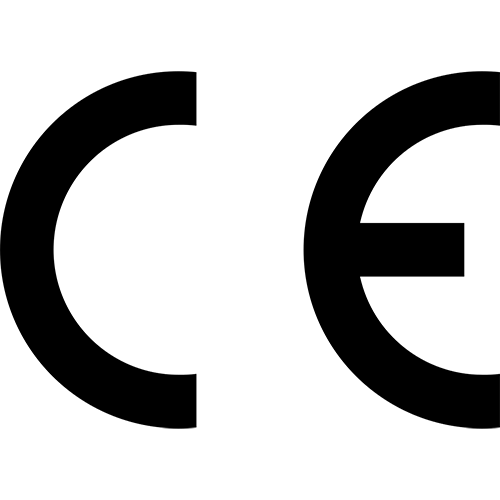
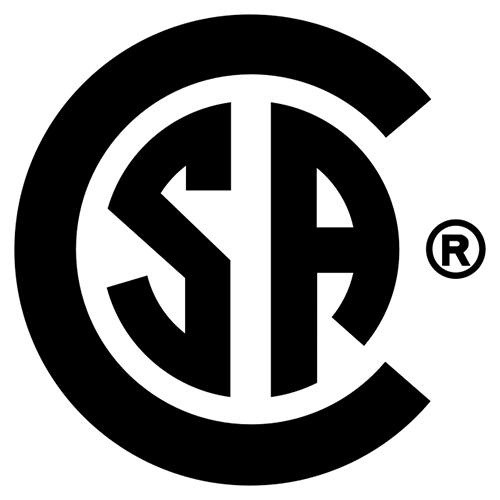
The Japanese Industrial Standards or JIS standards are a set of standards stipulating the requirement for products, including safety, quality, performance, scales, and types.
The Ministry of Economy, Trade, and Industry (METI) in Japan has been establishing and revising these standards in response to the changing needs of society.
On the other hand, there are also the GB/T standards that the universal hardness tester also meets. GB/T standards refer to the national standards issued by the Standardization Administration of China.
3. Closed-loop system in hardness testing
The triumphs of engineering skill rest on a chemical foundation – Horace G. Deming
Unlike traditional dead-weight hardness testers, the modern universal hardness tester does not produce erroneous results. The old system of dead-weight testers was marred with unstable application force that resulted in load overshoots and undershoots.
That is because the old system required the use of levers with pivots and guides that produced friction and induced errors.
In contrast, the new closed-loop technology of the modern NextGen universal hardness tester allows the device to constantly check itself to ensure that only correct test forces are applied to the indenting object.
The loop system has a way to measure the force being applied during the test, and then feed the information to the control system. The feedback is then used by the system to adjust the force being applied.
In addition, hardness testers using the new closed-loop technology are available for Brinell, Knoop, Vickers, and Rockwell hardness testers in a wider variety of ranges of test forces. Load cells of these hardness testers typically offer range limitations of 1 to 100.
For example, if the lowest load limit is 10 kg, then the upper limit is 1,000 kg. This wide range of available forces is generally greater than the range offered by the dead-weight models.
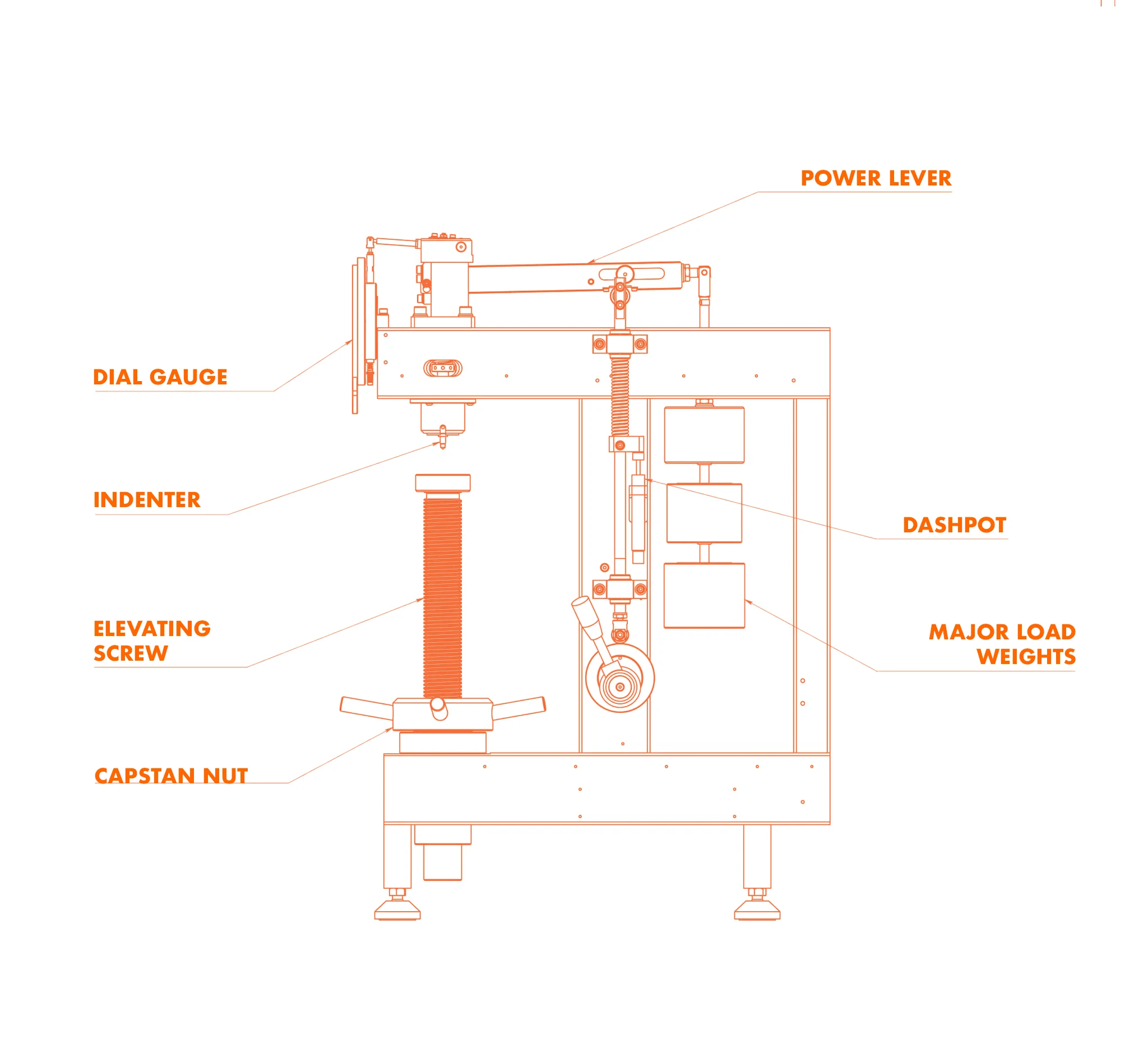
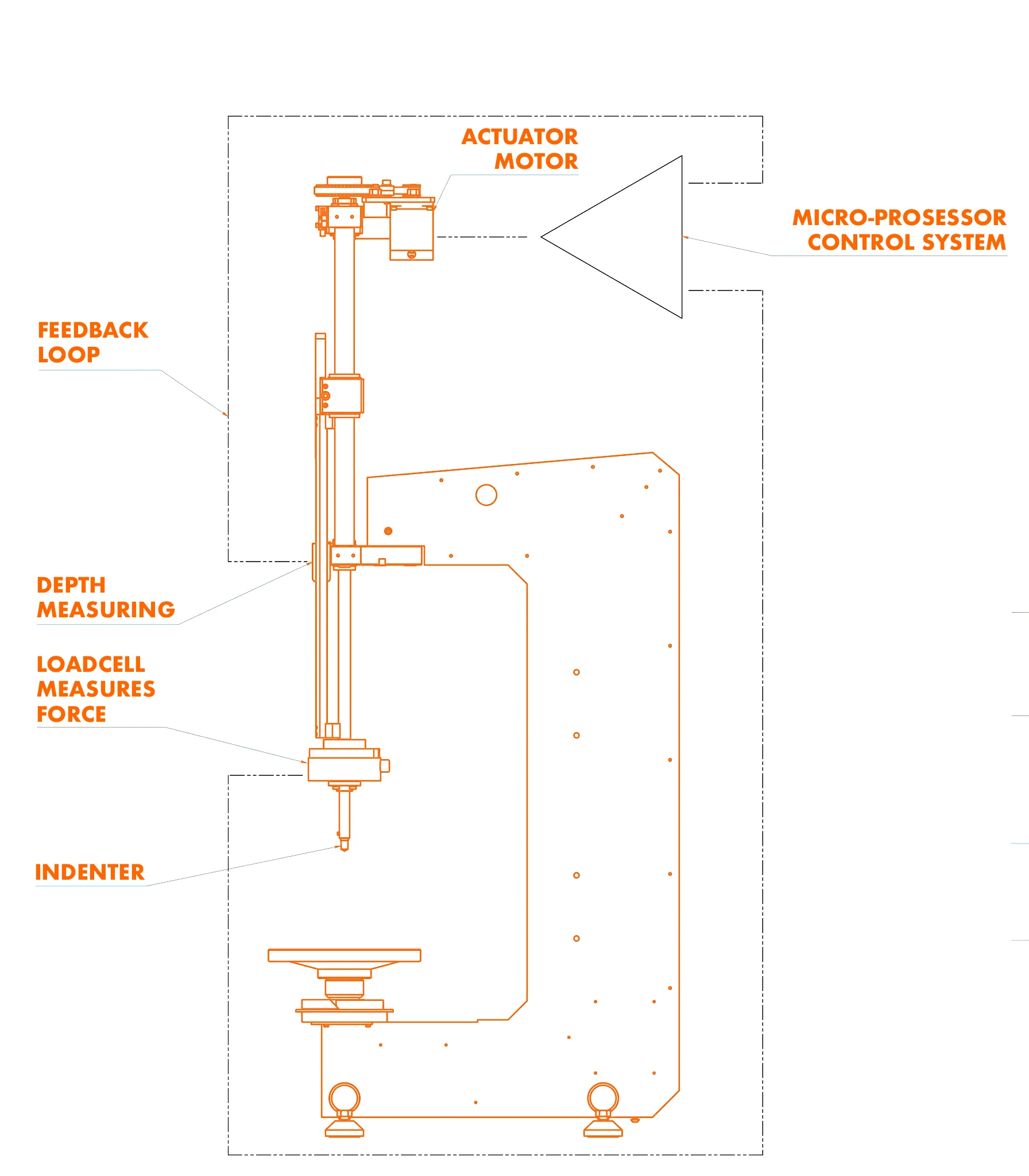
4. Simple mechanical structure
Before the introduction of closed-loop systems in hardness testers, traditional testers came with complex mechanical structures loaded with many parts and complex weight stacks. The newer models now have gotten rid of the complicated setup of earlier models.
This advantage is obvious. While the new universal testers are usually a more expensive device, you can still take advantage of their simplicity. Because it has a simple structure, such a device can easily be calibrated and maintained. Also, the device is cost-effective in terms of after-sales service.
The new technology of the closed-loop universal hardness testers also offers a wide range of test forces that further increases value for the user. The available range of test forces supersedes single-scale testers that require additional expense for the need to add more devices to cover differing testing needs.
Such an advantage is especially welcome in the heat treating industry, where metalworking processes are used to alter the physical and chemical properties of materials.
According to the book Common Pitfalls for Hardness Testing, hardness testing is the most common material check performed in the material testing industry.
The test is usually performed to know the failure or success of certain heat-treatment procedures or to reject or accept a material. This type of test is considered one of the easiest tests to apply in the metallurgical laboratory, but arguably one of the hardest tests to perform correctly.
Thus, if you want to know whether your heat-treating procedures suit your production materials, then you can use the universal hardness tester for such a purpose. Adjust your procedures accordingly, depending on the results of hardness test results.
5. Universal hardness tester equipped with a camera
In testing material for hardness, it is sometimes necessary to find the impressions the indenter made on the samples. However, these impressions can be difficult to locate because of their very tiny size.
To help with this problem, universal hardness testers are equipped with a camera. The camera feeds the images to the computer, enabling the operator to view the image he needs to observe more clearly.
The enlarged images presented via the camera and the monitor allow the operator to easily work on the tips of the impressions.
In addition, viewing the impressions with enhanced magnification can be relaxing to the eye compared to observing them through an eyepiece. This reduces operator fatigue.
The NextGen universal hardness tester is equipped with both eyepieces (for Brinell and Vickers) and a camera for enhanced image magnification.
6. Equipped with touch technology
The modern universal hardness testers are equipped with touch technology, as touchscreens have become ubiquitous in people’s lives and the workplace.
Where once it was only seen on GPS devices and ATMs, people now expect any handheld lab devices to respond to the swipe of the finger. This comes with a lot of benefits to the lab tester.
Touchscreens offer a less daunting user interface compared to switches and buttons. This can create an immediate sense of ease among workers in the testing lab.
The ease of use is obviously beneficial to the user, but looking at the organizational level, it can also be beneficial to the management. One, it minimizes the time needed to train the technical staff. Two, it reduces the likelihood of retraining users, and three, it speeds up the productivity of a testing lab.
Touch technology is a flexible technology that allows developers to incorporate their own creativity to improve the software. Developers can then create more visually appealing interfaces with intuitive gestures and icons that can make lab work smoother and easier.
7. Ergonomic testing device
The ergonomic design of the universal hardness tester ensures a positive working experience for the user. The screen is positioned in such a way that the user’s body does not experience strain and is in an upright position.
With this testing device’s correct screen positioning, you can sit with your back straight and your feet flat on the floor. This position encourages safety and improves blood circulation. At the same, it decreases body pains and promotes higher productivity levels.
NextGen’s universal hardness testers come with solid and compact workbenches.
8. Reproducible results
The universal hardness tester guarantees reproducible results to make sure that you get the same results no matter who is operating the device.
With its software-controlled focus, shading correction capacity, regulated light source, and image cleaning capacity, you can obtain reproducible results no matter the number of indents measured.
To further ensure accurate and reproducible results, the tester needs to account for the effects of the environment, preparation, and sample size every time.
Material samples should fit the sample stage and must be placed perpendicular to the tip of the indenter. The test surface must also be smooth and free from foreign matters. In addition, the tester itself should be free from vibrations during testing.
9. Multiple material testing types
Apart from the Vickers, Brinell, and Rockwell tests, the NextGen universal hardness testing machine can also do heat treatment, nitriding, hardening, cementation, and hard facing. Knoop tests on glass and ceramic materials are also possible with this device.
You can check the NextGen website for information on available scales for the Vickers, Rockwell, and Brinell hardness tests. The website also provides information on the test forces available for each of these three types of hardness tests.
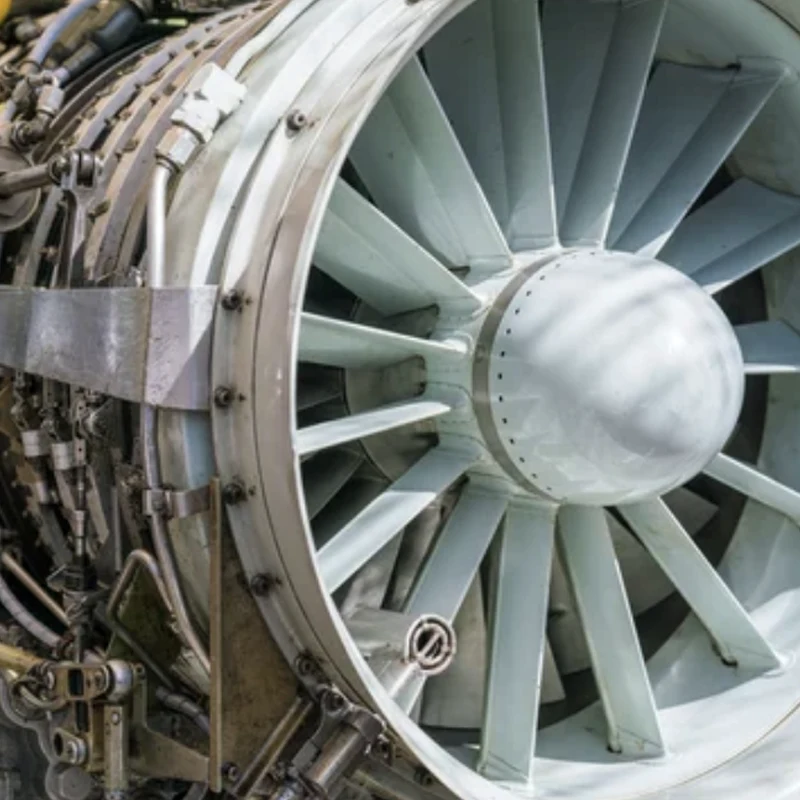
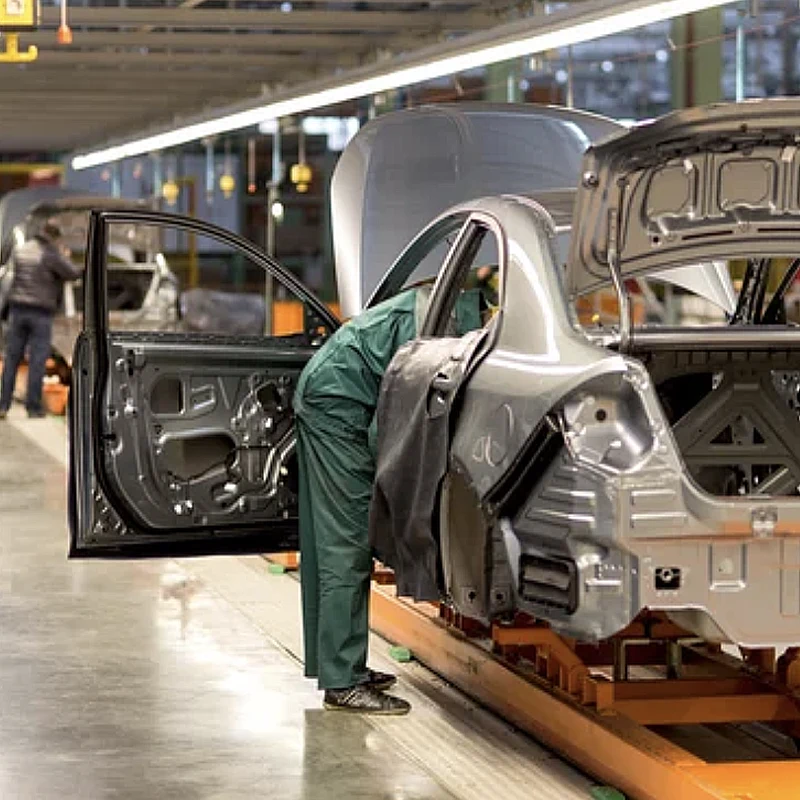
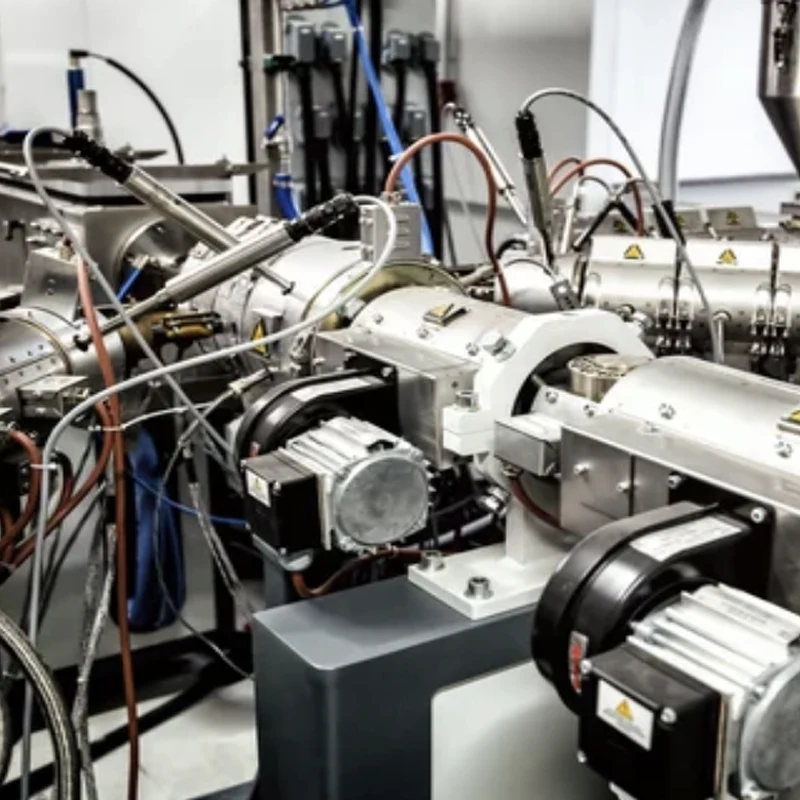
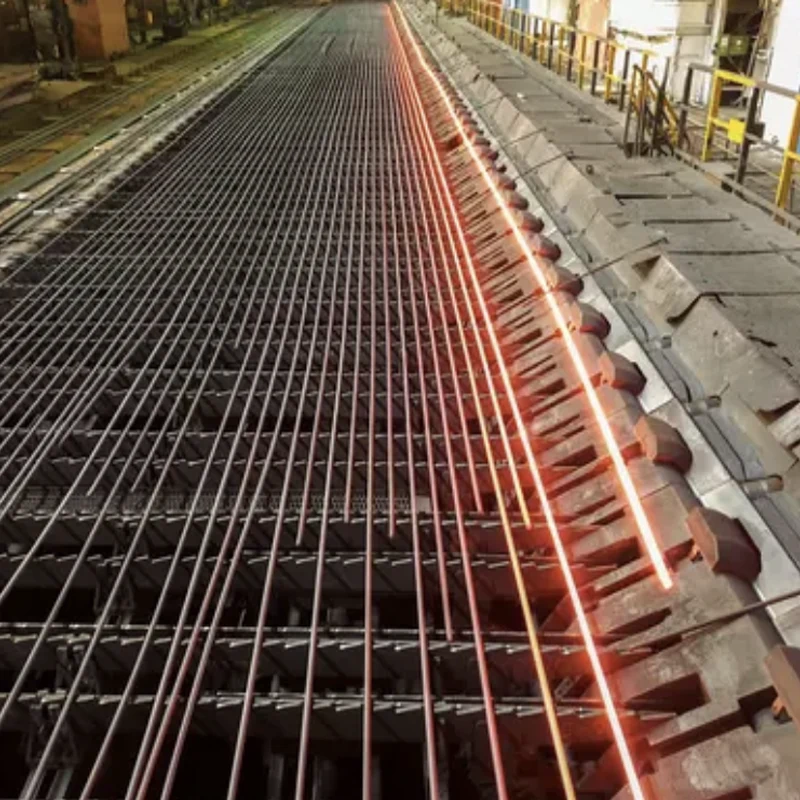
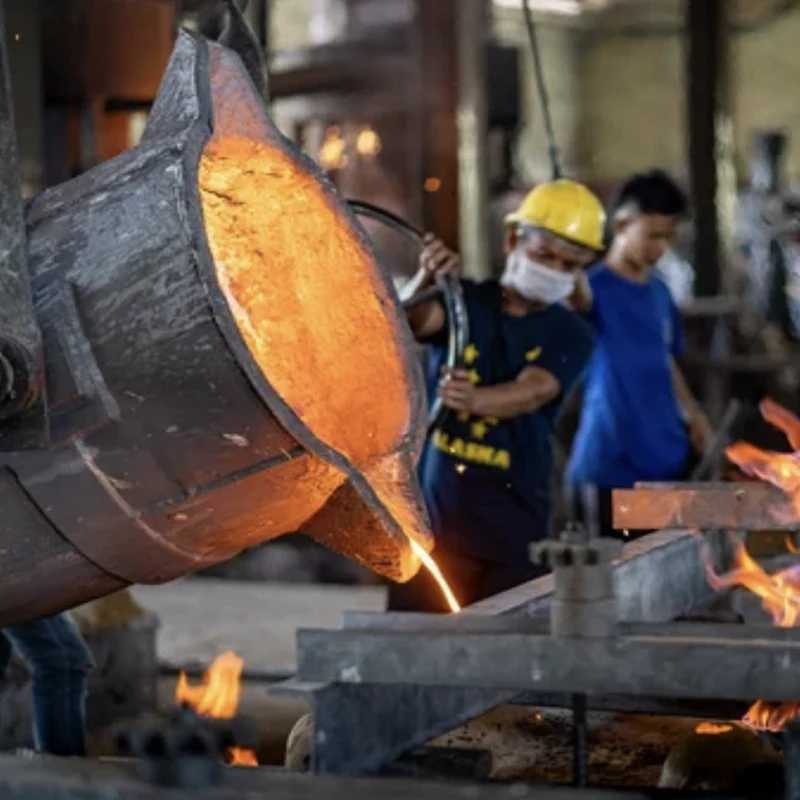
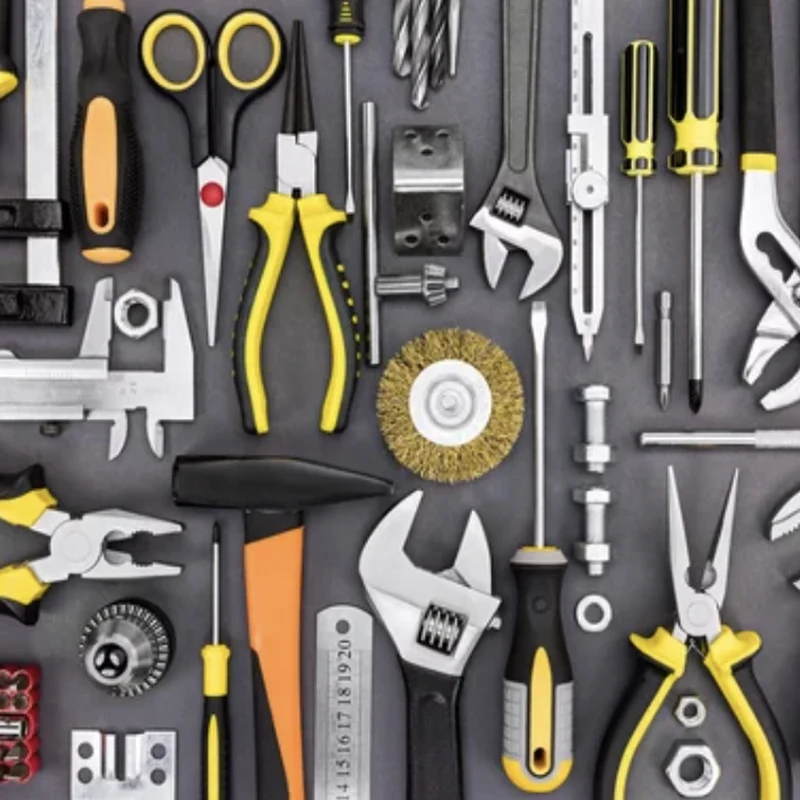
10. PC-based testing system
The universal hardness tester comes equipped with a PC-based testing system. A PC-based testing system comes with an auto-read feature with the help of a high-resolution camera.
Thus, this system allows direct and accurate measurement of hardness value using advanced image-processing technology. It also accommodates a wide range of material types, ranging from the softest metals, such as lead, to the hardest types, such as hardened steel.

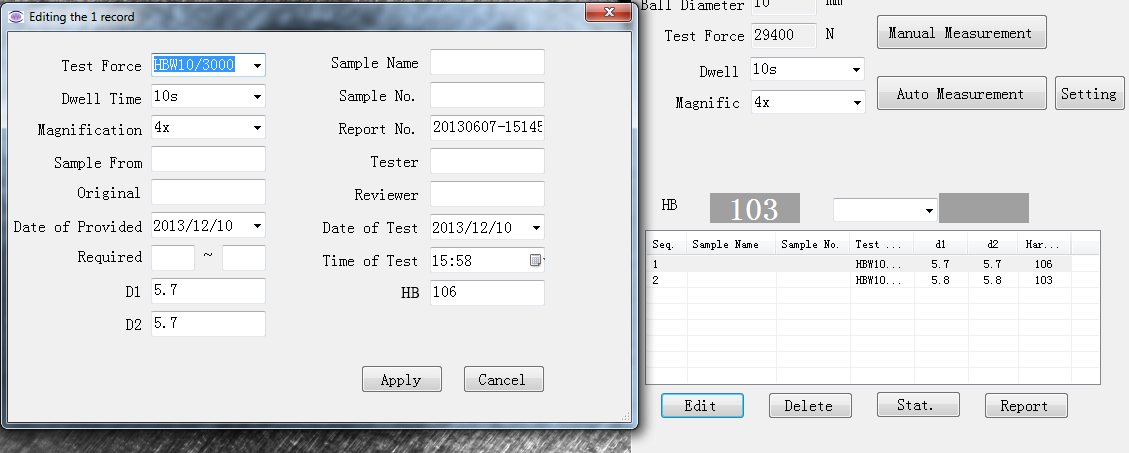
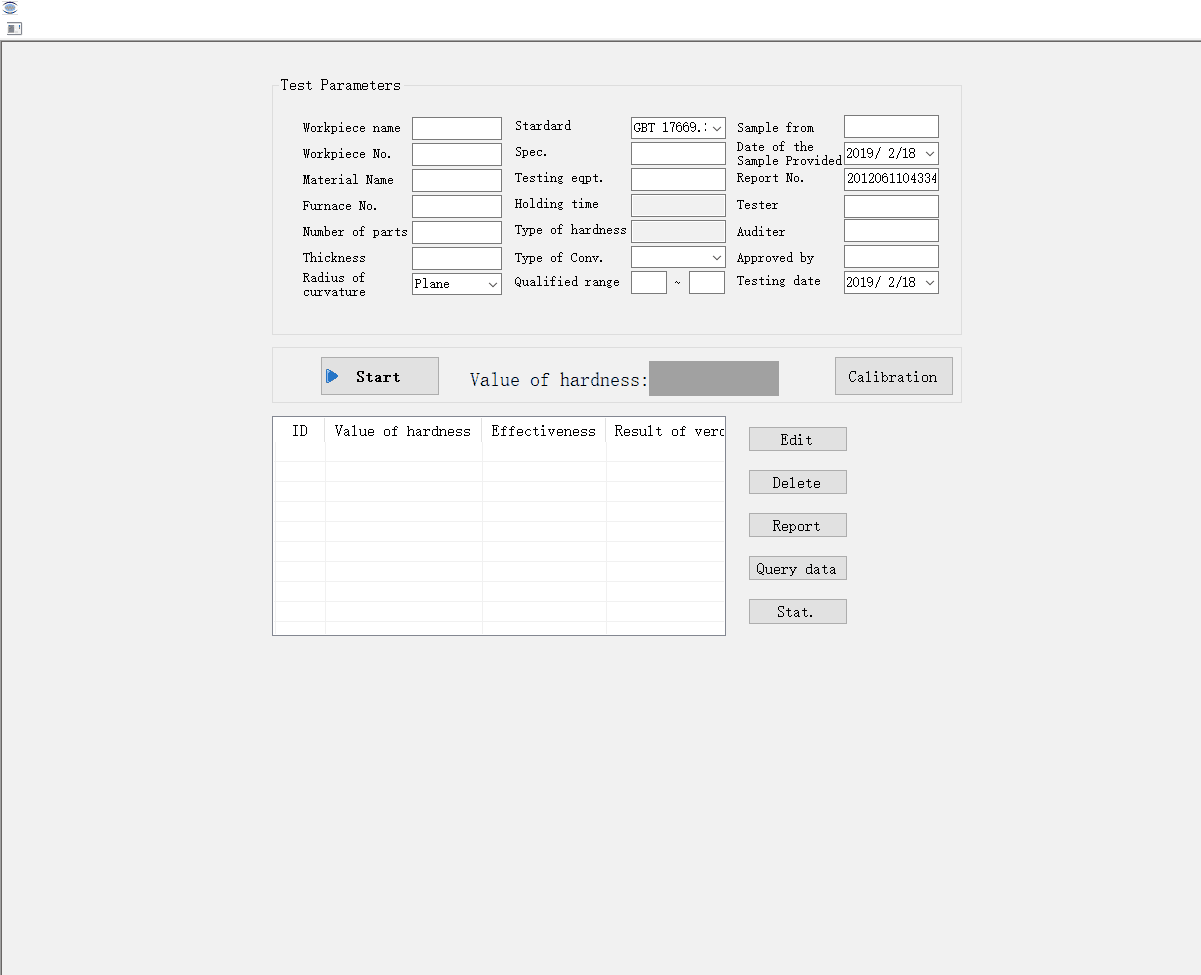
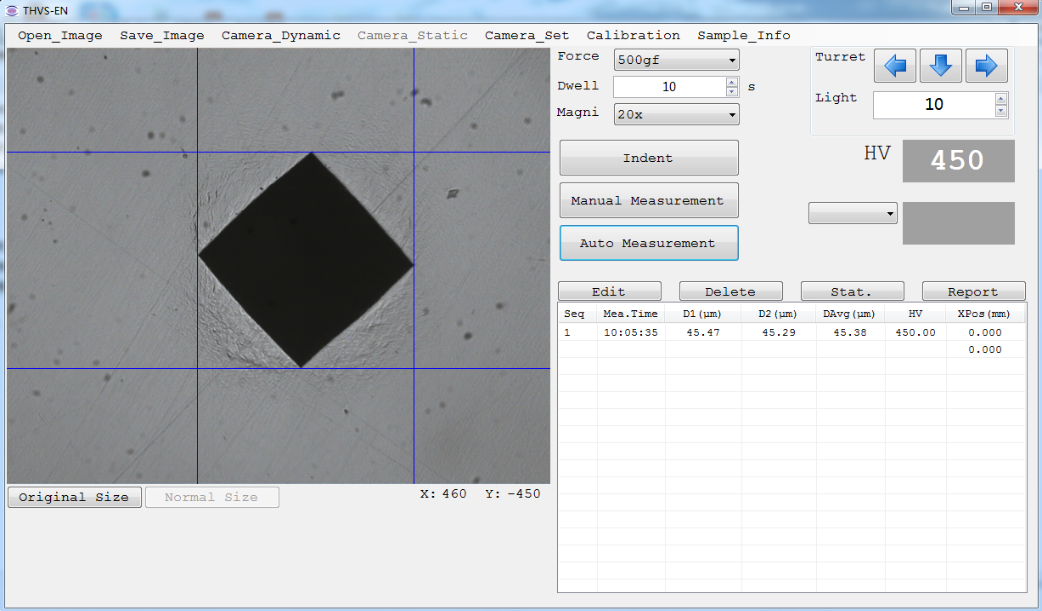
11. Absolute test accuracy
The NextGen universal hardness tester delivers maximum accuracy each time. It only allows a maximum force error of 0.5% and has a very low minimum measuring unit of 0.1 micrometers. Also, it offers a high total magnification level of 75 times the size of the test piece.
This machine can generate and store data with real-time graphs and statistics.
12. Large test space
NextGen’s universal hardness tester comes with a large space for you to place your samples. For the Rockwell test mode, it offers a vertical space of 220 mm, while for the Vickers and Brinell, it offers a maximum vertical space of 150 mm. The horizontal test space is also 200 mm.
This universal hardness tester comes with a sliding spindle that provides sufficient support for the specimen under testing.
NextGen offers an industry-leadingautomatic universal hardness testerwith a turnkey solution package that includes:
- NIST traceable consumables – NIST traceable calibration on consumables certifies that these products pass the standards set by the National Institute of Standards and Technology. It also guarantees that the manufacturer of these products matches NIST-maintained measurement standards.
- Extended warranty – If you need to expand the warranty of your universal hardness tester and get comprehensive information about it, please contact the customer service department of NextGen. Note that you have the choice to extend the warranty any time prior to the expiration of the manufacturer’s guarantee.
- Training videos – The training videos illustrate the use of the universal hardness tester. These training videos are available now on NextGen’s website. You would like to check additional videos posted by NextGen from time to time.
- Lifetime service and support – NextGen offers lifetime product and service support so that you always have technical support available anytime you need it.
- User-friendliness – The universal hardness tester is easy to use so that you will not waste a lot of time, energy, and money training your technical staff in order to learn how to properly use it.
NextGen’s universal hardness tester comes with a large space for you to place your samples. For the Rockwell test mode, it offers a vertical space of 220 mm, while for the Vickers and Brinell, it offers a maximum vertical space of 150 mm. The horizontal test space is also 200 mm.
Universal hardness tester features
NextGen’s universal hardness tester comes with the following features:
- Equipped with Brinell, Vickers, Knoop, and Rockwell test methods
- Easy to operate with a large touch-screen interface
- A closed-loop system with a load cell
- You will not need to install weights with this system.
- Ensures a high level of test accuracy with the system’s automated test for correction feature
- It comes with a modular body that allows for easy maintenance of the device.
- It also features a curvature radius that can auto-correct (for Rockwell tests)
- It comes with large testing and sample information capacity.
- It offers password protection for the user’s setup parameters.
- It comes with a disc for saving data in the EXCEL format. It, therefore, highlights the ease of data processing and editing.
The unit comes standard with an 8-inch LCD screen, automatic measuring software, a CCD camera, and the full scope of certified consumables for all the available testing methods, providing the perfect turnkey solution for your testing requirements.