The aerospace industry, which includes the design, manufacturing, and maintenance of aircraft and spacecraft, continues to grow at a rapid pace. In 2023, the global aerospace and defense market size expanded significantly, forecasting further growth from $884 billion in 2023 to $985.56 billion in 2024, at an impressive compound annual growth rate (CAGR) of 11.5%. This expansion is propelled by a resurgence in air travel demand, increased military spending, and technological advancements in aircraft manufacturing and materials​​.
A key driver behind this growth is the demand for commercial aircraft. Companies like Airbus and Boeing have seen substantial increases in business revenues, underscoring the sector’s recovery post-pandemic and the industry’s importance in global connectivity and defense​​. For instance, Airbus delivered 661 commercial aircraft in 2022, marking an 8% increase from the previous year, reflecting the growing demand for commercial aviation​​.
In this article, we will discuss the aerospace material testing innovations, which have become a cornerstone of this dynamic industry. As it continues to evolve with digitalization and the adoption of emerging technologies, material testing is fundamental to validating the suitability and integrity of materials used in aircraft and spacecraft construction.
Introduction to Aerospace Material Testing
Material testing transcends the aerospace industry, holding great importance across all sectors that impact our daily lives. From the construction of the offices where we work to the vehicles we use for daily transport, material testing guarantees the safety, durability, and performance of the products we rely on. This foundational process plays a crucial role not just in the development of cutting-edge aerospace technologies but also in the engineering of everyday items.
The Significance of Aerospace Material Testing
Aerospace material testing consists of a number of techniques and methodologies aimed at evaluating the properties of materials used in aerospace component construction. The purpose of this process is to ensure that materials can withstand the extreme conditions they will face during flight, such as high velocities, temperatures, and pressures.
A Brief History and the Evolution of Material Testing in Aerospace
Material testing in the aerospace sector has evolved significantly since aviation’s early days. Initially, the focus was on basic materials like wood and fabric, which were used in the construction of the first aircraft. As aviation technology advanced, the industry shifted towards more durable and lighter materials such as aluminum and titanium. This transition necessitated the development of more advanced testing methods to analyze the mechanical properties of these materials under various conditions.
The advent of the jet age and space exploration era marked a significant milestone in material testing evolution. The need for materials that could withstand outer space harsh environments led to the development of advanced composites and alloys. Testing these materials required innovative techniques, including stress and thermal analysis, non-destructive testing (NDT), and computational simulations to predict how materials would behave in untested situations.
Today, the aerospace industry continues to push material science, exploring materials like carbon fiber composites and ceramic matrix composites. These materials offer superior strength-to-weight ratios, high-temperature resistance, and improved efficiency for next-generation aircraft and spacecraft. Consequently, aerospace material testing has become more complex, incorporating modern technologies such as digital imaging, ultrasonic testing, and 3D scanning.
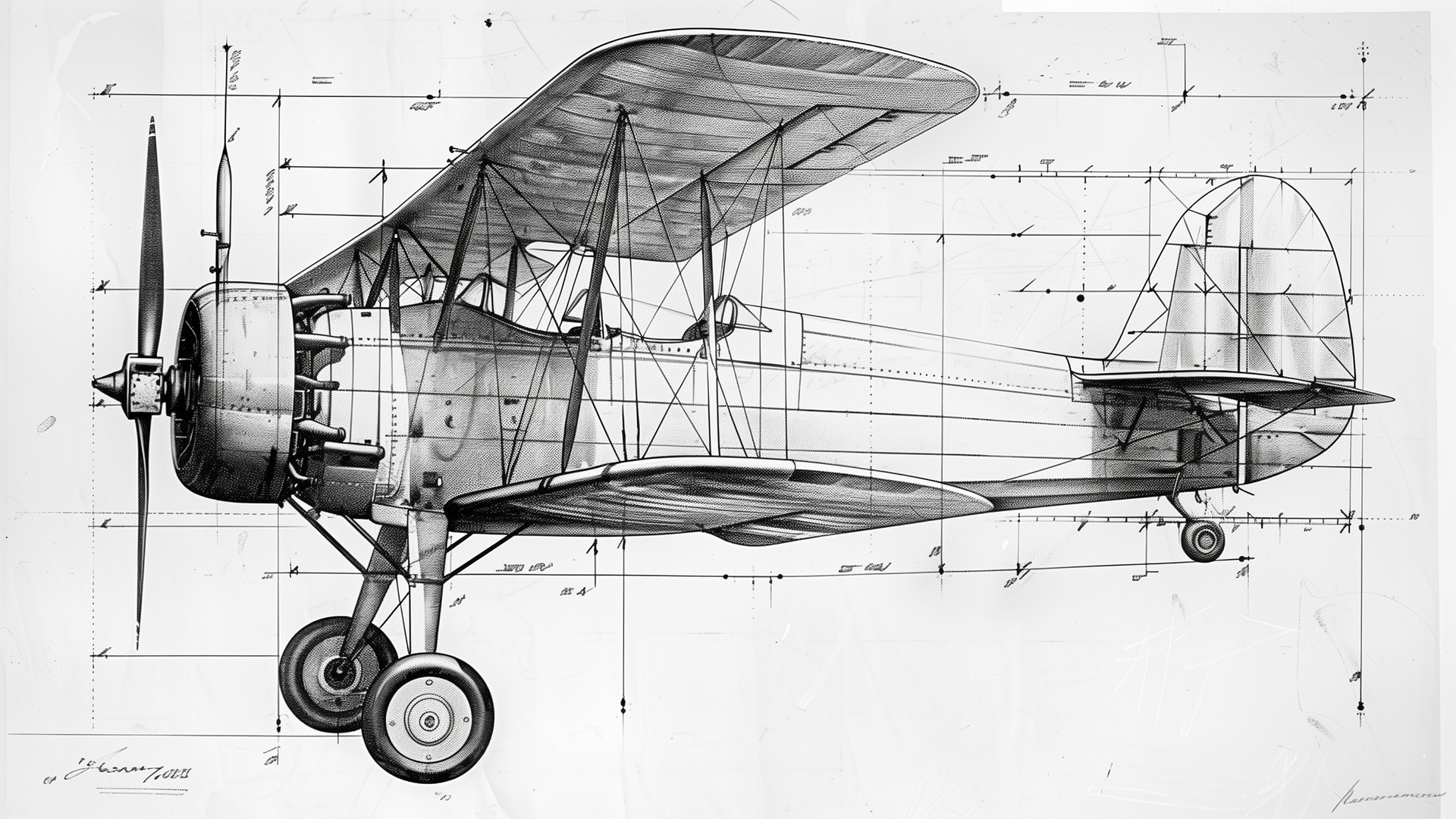
The Importance of Advanced Materials in Aerospace
The relentless quest for advancement in aerospace engineering has continually driven humanity not to stand still but to evolve, pushing the boundaries of what’s achievable in space exploration. At the heart of this evolution is the development and application of composites and alloys. These materials are fundamental to constructing lighter, stronger, and more heat-resistant aerospace structures, offering unprecedented improvements in performance, safety, and efficiency.
The Role of Advanced Composites
Advanced composites, including carbon fiber reinforced plastics (CFRPs), have become cornerstone materials in aerospace due to their lightweight yet durable nature. For instance, Airbus has integrated composites extensively into their aircraft, with the Airbus A220 consisting of 70 percent advanced materials, including 46 percent composite materials. This integration results in significant reductions in fuel usage and CO2 emissions.
The Boeing 787 and the Airbus A350 XWB are notable examples of where advanced composite materials have been revolutionary. This marks a significant shift in aircraft design towards more fuel-efficient and cost-effective solutions. These aircraft feature constructions that extensively utilize composites, leading to remarkable achievements such as a 25% reduction in operating costs, fuel burn, and CO2 emissions for the A350 XWB, due to its 53 percent carbon-composite construction​​​​.
Defence Sector
In the defense sector, the importance of advanced composites becomes even more pronounced, especially in the design and manufacturing of military aircraft. These materials not only contribute to fighter jet stealth capabilities, making them less detectable on enemy radar but also increase their survivability against environmental threats like lightning strikes. This is achieved through the electrical conductivity of carbon composites, which can potentially eliminate the need for additional protective measures such as copper mesh, traditionally used to dissipate lightning strikes​​.
Computational Materials Design and Simulation
Integrated Computational Materials Design (ICMD) represents a breakthrough in aerospace materials testing and development, drastically cutting down the timeframes for novel materials creation, testing, and certification. In addition to reducing time, this significantly lowers the cost by millions of dollars, removing the need for extensive experimentation that characterized previous approaches. ICMD enables aerospace manufacturers to design, develop, qualify, and deploy novel materials for critical flight components, leveraging computational physics-based modeling alongside powerful toolkits for materials design and simulation​​.
A notable example of ICMD’s impact is its application in alloy design, which has been indispensable for developing materials with previously non-existent properties. For instance, the quest for alloys that can withstand high-pressure oxygen environments in space launch vehicles has led to the identification of potential metallurgical concepts through ICMD.
ICMD has also proven instrumental in material qualification, where it saves significant development time and cost by using modeling to predict properties. It also quantifies uncertainties in those predictions. This process has been applied successfully in the aerospace sector, enabling the use of modeling to ensure the appropriateness of process and material specifications to achieve desired properties. The ability to guide changes at an early stage of development helps avoid the exhaustive effort of material production and testing that might not meet the intended goals​​.
Innovative Non-Destructive Testing Techniques
Advances in NDT technologies have significantly boosted the capability to detect even the smallest imperfections or damages in materials and components used in aerospace applications, ranging from aircraft and missiles to satellites and other defense systems.
NDT technologies include computed tomography (CT) scanning and digital radiography. CT scanning, for instance, is particularly effective for inspecting composite materials used in aerospace, providing 3D images that can reveal defects like water ingress, crush damage, and the integrity of metal inserts in hybrid structures. This technology has become a go-to in the development and inspection of composite structures, aiding in the acceleration of new composite fabrication processes and the validation of critical components​​.
Ultrasonic testing stands out as the primary choice for examining composite parts, thanks to its ability to reveal hidden flaws using sophisticated imaging techniques. This method’s integration with robotic systems and suitability for automated defect recognition highlights its modern applications. Innovations like laser ultrasound and air-coupled systems have broadened their use by addressing previous sound coupling challenges.
Radiographic testing, including X-ray, gamma ray, and CT scanning, has also seen widespread application in the aerospace sector. These methods are invaluable for detecting internal flaws, with CT scanning offering advantages in flaw orientation sensitivity due to its ability to produce 3D images of components. Fast acquisition systems have reduced data acquisition times, although analyzing scan results remains time-consuming​​.
Other notable NDT methods used in the aerospace and defense industry include eddy current testing, which uses electromagnetic induction to detect eddy currents in materials; and Magnetic particle testing, which reveals flaws in ferromagnetic materials like iron, nickel, and cobalt. These methods are essential for inspecting conductive materials commonly incorporated into aerospace components​​.
Advanced Material Testing with the UH200 Ultrasonic Hardness Tester
While discussing ultrasonic testing, we must mention our leading product – the UH200 Ultrasonic Hardness Tester. Designed with the aerospace sector’s stringent requirements in mind, this device easily integrates into the innovative non-destructive testing field, providing exceptional precision and efficiency.
The UH200 uses ultrasonic contact impedance (UCI) technology to offer non-invasive hardness measurement of metals, making it an essential tool for aerospace applications. Its ability to perform rapid assessments without leaving any marks or indentations on the parts helps ensure that critical components remain structurally intact.
With its advanced single-chip technology and highly accurate sensing system, the UH200 stands out by delivering more accurate and faster results than conventional ultrasonic hardness testers. It supports different value conversions among HV, HB, HRC, etc., allowing for versatile application across different materials and components. The capability to calculate the average of multi-point measurements further enhances its accuracy.
Moreover, the UH200 is designed for practicality and durability. Its large LCD screen, sealed housing with rubber protective strips, and frost-resistant display ensure reliable operation under challenging workshop or field conditions, including high humidity, dust, and extreme temperatures. The built-in camera and PC software with an intuitive interface simplify the process of documenting and analyzing the hardness of tested areas, enabling aerospace engineers to maintain rigorous quality control easily.
Advancements in SiC/SiC Ceramic Matrix Composites
The development of Silicon Carbide (SiC) Fiber-Reinforced SiC Ceramic Matrix Composites (SiC/SiC CMCs) represents a significant leap forward in materials technology, particularly within the aerospace sector. These composites, developed at NASA’s Glenn Research Center, aim to redefine high-temperature and high-stress applications in aerospace engineering.
SiC/SiC CMCs are distinguished by their exceptional durability and resistance to extreme temperatures, capable of withstanding environments up to 2,700 degrees Fahrenheit. This remarkable temperature resistance, coupled with their lightweight and reusable nature, makes them ideal for use in high-performance machinery such as aircraft engines. These components can last months or even years between maintenance cycles, significantly reducing downtime and enhancing aerospace operations efficiency.
NASA’s patented technologies for SiC/SiC CMCs involve innovative design and processing techniques that yield composites capable of enduring adverse structural and environmental conditions for extended periods. The use of non-oxide SiC fibers and matrices results in materials that offer superior benefits to traditional options like metallic superalloys, monolithic ceramics, carbon fiber composites, and oxide/oxide ceramic composites. These benefits include lower density, higher temperature capability, lower thermal expansion, and greater oxidative durability​​.
The applications of SiC/SiC CMCs extend beyond aerospace, encompassing the chemical industry, heat transfer industry, and even space vehicles, showcasing their versatility and potential to revolutionize many high-temperature applications. From combustion and turbine section components of aero-propulsion and land-based gas turbine engines to thermal protection systems and turbopump components for space vehicles, SiC/SiC CMCs are set to be key components in advancing the next generation of aerospace technology​​.
Why Impact Testing is So Important in the Aerospace Industry?
Impact testing in the aerospace industry ensures that aircraft and spacecraft can withstand extreme forces without compromising structural integrity. This form of testing includes several key applications, each addressing specific challenges aircraft face during their operational lifecycle. Here are some examples:
-
Projectile impact testing is designed to simulate high-speed collisions with different objects, such as animals, hail, or even debris, which can occur when an aircraft is in flight. By firing materials like aluminum or titanium at test specimens at velocities that mirror those encountered in real-life incidents, engineers can assess the resilience and integrity of aircraft materials and structures.
-
Bird strike testing, mandated by the Federal Aviation Administration’s Wildlife Hazard Mitigation Program, focuses on birds’ risks to aviation technology and life. It aims to determine how well components, particularly engine casings, can withstand bird ingestion. Such incidents not only pose significant safety hazards but can also cause extensive damage to aircraft.
-
Hail impact testing, while similar to bird strike testing, concentrates on the aircraft’s ability to endure hail impacts. This is especially true for exterior components like windshields, radomes, antennas, and pitot tubes, which are directly exposed to such weather phenomena.
Dual Column Charpy Impact Tester – Top of the Line
The Class D – Dual Column Charpy Impact Tester is specifically designed to meet the high demands of testing materials under high-energy impact conditions. This tester is ideally suited for Charpy Impact testing, complying with ASTM E23, ISO 148, and EN10045 industry standards.
The Class D Metals Impact Tester is available in two popular models, with peak capacities of 450J and 750J, and offers optional pendulums for a range of energies from 150J up to 600J. This versatility means that the tester can accommodate a broad range of testing requirements, from educational settings to high-level industrial manufacturing. The 450J model finds its place in educational institutions and government facilities, highlighting its applicability in settings focused on learning and experimental research. Conversely, the 750J model caters to the heavy-duty needs of steel production and aerospace industries.
Safety of operation is of utmost importance, and the Class D tester addresses this with a fully enclosed testing area, minimizing risk during the testing process. The precision-engineered pendulum, equipped with an electromagnet for secure locking, is designed for accuracy and repeatability in results, underpinned by a quality PLC controller.
One of the standout features of the Class D tester is its heavy cast iron base, designed to mitigate vibrations and ensure impact testing accuracy. The dual-column impact frame increases the system’s structural integrity, allowing it to withstand and accurately measure high-energy impacts. Additionally, the tester’s design incorporates a standard touchscreen display and offers optional PC connectivity for software analysis, making data analysis both accessible and comprehensive.
Challenges and Future Directions in Aerospace Material Testing
The aerospace industry faces several challenges in material testing, notably adapting to advanced composites and metals. Composite materials, for instance, differ significantly from metallic structures in their failure mechanisms, such as delamination. This poses an especially challenging problem due to its speedy propagation and potentially catastrophic consequences. Unlike isotropic materials such as aluminum alloys, composites require detailed understanding and innovative testing approaches to predict and assess damage tolerance and failure modes accurately​​.
One significant hurdle in aerospace material testing is the search for reliable and accurate equipment capable of handling advanced materials under changing operational and environmental conditions. This challenge highlights the need for comprehensive damage tolerance assessment and fatigue testing, particularly for high-value components designed with a no-growth concept in mind. Such components must withstand operational stresses without allowing undetected manufacturing defects or damage to grow.
Looking forward, environmental regulations and the push for more fuel-efficient and durable components are driving the adoption of Ceramic Matrix Composites (CMCs) and Metal Matrix Composites (MMCs). These materials offer significant advantages in weight reduction and high-temperature performance but require extensive characterization and evaluation to meet aerospace standards. CMCs, for instance, introduce high-temperature testing complexities that challenge existing methodologies and equipment​​.
The aerospace sector continues to evolve, with testing services like Element providing a comprehensive range of testing methodologies for an array of materials, including metals, nickel and titanium alloys, and composites. Their global network of Nadcap-accredited laboratories and expert teams supports the industry’s need for detailed material characterization, R&D support, and production. This level of expertise and infrastructure is necessary for addressing current challenges and preparing for future innovations in aerospace material testing​​.
Concluding Insights on Innovations in Aerospace Material Testing
The aerospace industry’s dynamic evolution is illustrated by significant advancements in material testing, driven by the growing demand for safer, more efficient aircraft and spacecraft. The sector’s robust growth, highlighted by an impressive compound annual growth rate and rising demand for commercial aircraft, sets the stage for continuous innovation. Advanced materials such as composites and alloys are at the forefront of these developments, offering remarkable improvements in strength, durability, and lightweight properties for aerospace applications. Computational materials design and simulation, alongside cutting-edge non-destructive testing techniques, further solidify the industry’s capacity to comply with standards and enhance aerospace component integrity.
Among the noteworthy innovations, the UH200 Ultrasonic Hardness Tester exemplifies the integration of ultrasonic testing principles with practical needs for hardness measurement in metals, making certain components remain structurally sound and perform optimally under flight conditions. Learn more about our innovative products like the UH200 Ultrasonic Hardness Tester and the Class D – Dual Column Charpy Impact Tester on their respective product pages for detailed insights into their functionalities and applications.
NextGen Material Testing Inc. stands at the crossroads of these advancements, offering a range of services and cutting-edge equipment tailored to the aerospace industry’s needs. From facilitating material testing to providing state-of-the-art testing equipment, we are equipped to support evolving requirements. Whether you’re seeking expert services or the latest in testing technology, we invite you to explore our offerings. Request an online quote, or reach out directly for personalized assistance from our team of experts.