U-notched and V-notched specimens are common types of samples tested in impact testing, namely Charpy and Izod tests. These specimens feature specific notch shapes that introduce controlled flaws into the material. This allows for precise assessment of toughness and ability to absorb energy upon impact. The Charpy impact test is a standardized method for determining material resistance to sudden stress. On the other hand, the Izod impact test is a standardized method for assessing the material’s ability to withstand impact forces, providing data on its toughness and durability under sudden loading conditions.
The primary purpose of including U or V notches in specimens is to create a localized stress concentration, which affects the material’s fracture behavior. The V-notch, characterized by its sharp angle, induces a higher stress concentration. It is ideal for testing the toughness of ductile materials like steel used in welding. In contrast, the U-notch, with its rounded profile, is better suited to brittle materials such as cast iron. These notches help simulate real-world conditions where materials face abrupt and intense stress.
At first glance, it may seem that preparing U- or V-notched specimens for impact testing is straightforward. However, like all material testing specimens, these samples undergo a fabrication process governed by stringent standards and testing requirements. We will discuss the process of creating U and V-notched specimens for impact testing in this blog, taking into consideration all the necessary details to be able to understand the whole process in detail.
Importance of U and V Shapes in Impact Specimens
In impact notches, the U and V shapes are intended to create a controlled stress concentration point. This has a significant effect on the fracture response of the material and the energy absorption characteristics of the material over time.
Why Use U and V Shapes?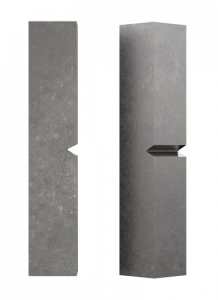
-
Stress Concentration
-
V-Notch: The V-notch, with its sharp angle (typically 45°), generates a high-stress concentration. This is ideal for testing ductile materials such as metals. In metals it is necessary to measure the material’s ability to withstand and absorb high energy impacts before fracturing. This notch shape is predominantly used in both Charpy and Izod tests for materials requiring a higher stress concentration.
-
U-Notch: The U-notch, with a rounded base and typically a 1 mm radius, creates a lower stress concentration than the V-notch. This is suitable for fragile materials such as cast iron and certain plastics, which might fail prematurely at higher stress concentrations. U-notches are commonly used in Charpy tests to evaluate the impact resistance of more brittle materials.
-
-
Fracture Mechanics
-
The notches help replicate real-world situations where materials might have imperfections or sharp flaws.
-
The presence of a notch guarantees that the fracture initiates at a specific point. This allows for consistent and reproducible results between different tests and materials.
-
- Material Behavior Analysis
-
-
Charpy Test: The Charpy test uses both U and V notches to measure the energy absorbed during fracture. The test specimen is placed horizontally, and the pendulum strikes the side opposite the notch. The test can be conducted at a range of temperatures to detect materials’ ductile-to-brittle transition.
-
Izod Test: The Izod test, typically using V-notched specimens, positions the specimen vertically. The pendulum strikes the specimen on the same side as the notch, measuring the material’s ability to resist impact and propagate cracks. This test is also useful for materials like plastics and composites.
-
The Process of Preparing U- and V-Notched Specimens
There are several steps that must be followed when creating impact specimens with U and V shapes. The steps involved in this process include the following:
-
Material Selection: Selecting the appropriate material based on the testing requirements.
-
Cutting the Specimen: Cutting the material into standard dimensions specified by relevant testing standards.
-
Machining the Notch Using Precision Machinery: Creating notches (V-shaped or U-shaped) using notching and broaching equipment.
-
Specimen Conditioning: Creating a controlled environment for specimen conditioning.
Step 1: Material Selection
When preparing U- and V-notched specimens for Charpy and Izod impact testing, choosing appropriate material is crucial. This step involves choosing materials that meet the specific requirements of the test standards. The selected material must be representative of what will be used in real-world applications.
Material Selection Criteria
-
Material Type: Impact testing can be performed on many materials, including metals, plastics, composites, and alloys. The choice of material often depends on the industry and the specific application for which the material is intended. For instance, metals are commonly tested for structural components, while plastics might be tested for automotive parts or packaging materials.
-
Ductility and Brittleness: The material’s inherent properties, such as ductility or brittleness, influence the type of notch used and the test method. Ductile materials like steel are often tested with V-notches, while brittle materials such as cast iron or certain plastics may be tested with U-notches to evaluate their impact resistance under stress concentrations.
-
Standards Compliance: The material must comply with the relevant testing standards to provide consistency and comparability. Standards like ISO 148-1 and ASTM A370 for metals, and ISO 179 and ASTM D6110 for plastics, specify the dimensions, preparation, and conditioning of specimens for impact testing.
-
Temperature Considerations: The testing conditions, including the temperature at which the tests will be conducted, must be considered during material selection. Some materials exhibit different impact strengths at varying temperature.
Step 2: Cutting the Specimen
Cutting the specimen is the second step in preparing U- and V-notched specimens for Charpy and Izod impact testing. The material is precisely cut into standardized dimensions during this process.
Standard Dimensions
Charpy Test Specimens:
-
Length: 55 mm
-
Width: 10 mm
-
Thickness: 10 mm
Izod Test Specimens:
-
Plastic Specimens: 64 mm x 12.7 mm x 3.2 mm
-
Metal Specimens: 127 mm x 11.43 mm (round bar).
These dimensions are specified by relevant standards such as ASTM E23 for metals and ASTM D256 for plastics.
Cutting Process
-
Material Preparation: Before cutting, the raw material needs to be prepared. This may involve cleaning the material to remove any surface impurities that could affect the cutting process or the test results.
-
Marking: The material is marked according to standard dimensions. Specimens must be marked correctly to verify they meet all specifications.
-
Cutting Equipment: The cutting process requires specialized equipment. Common tools include:
-
Band Saws: Used for initial rough cuts. Band saws cut large sections of material down to approximate dimensions.
-
Precision Cutters: Used for final cuts to achieve exact dimensions. These machines can make fine and precise cuts.
-
CNC Machines: Computer Numerical Control (CNC) machines are often used for highly accurate cuts. These machines are programmed with exact dimensions and cut multiple specimens consistently.
-
-
Cooling and Lubrication: During cutting, it is important to use cooling and lubrication fluids to prevent overheating and reduce friction. Overheating can alter material properties, which might affect test results.
-
Inspection: After cutting, each specimen is inspected to make sure it meets the specified dimensions. This can involve using calipers, micrometers, and other precision measurement tools. Any specimens that do not meet the standards are discarded or re-cut.
-
Deburring: The specimen edges are smoothed and any burrs or sharp edges are removed. This step makes sure that the specimens are safe to handle and have no imperfections that could affect test results.
Step 3: Machining the Notch Using Machinery
Machining the notch is the next step in preparing specimens for Charpy and Izod impact testing. During this process, a controlled stress concentration point is created on the specimen through precise notches.
Types of Notches
-
V-Notch: Typically 2 mm deep with a 45° angle and a 0.25 mm radius at the base.
-
U-Notch: Typically 1 mm radius with 2 mm or 5 mm depth.
Equipment and Machinery
A specialized piece of equipment is required when it comes to machining notches. The primary machines used for this purpose are:
-
Notching Machines: These machines are specifically designed to cut precise notches into specimens using linear knife cutting. This method avoids overheating and stress during notching operations. Notching machines are available in manual, motorized, and fully automatic models.
-
Broaching Machines: Broaching machines use a toothed tool (broach) that is pulled or pushed through the material to cut the notch. This method is highly precise and often used for U-shaped notches, especially in harder materials where consistent notch dimensions are crucial.
Machining Process
-
Specimen Preparation: Before machining the notch, specimens are prepared by making sure they meet the required dimensions (e.g., 55 mm x 10 mm x 10 mm for Charpy tests).
-
Setting Up the Machine: The notching machine is set up with the appropriate tools and parameters. For instance, the cutting speed may be adjusted depending on the material’s sensitivity to avoid overheating.
-
Cutting the Notch: The specimen is securely placed in the machine, and the notch is cut precisely. Automatic machines can handle multiple specimens on a single cycle.
-
Inspection: After machining, each specimen is inspected to verify that the notch dimensions meet the specified standards. This may involve using precision measurement tools like calipers and micrometers.
Step 4: Specimen Conditioning
Specimen conditioning is the last step in the process of preparing U and V notched specimens for Charpy and Izod impact testing before they are ready for testing. This process makes sure that the specimens are in a consistent state. Conditioning involves exposing specimens to a controlled environment to stabilize their properties before testing.
Purpose of Specimen Conditioning
Specimen conditioning is used to maintain a uniform temperature and humidity level. This is very important for materials that exhibit different mechanical properties under varying environmental conditions, such as plastics and certain metals.
Conditioning Procedures
-
Temperature Conditioning:
-
Specimens are often conditioned at a specific temperature to simulate real-world operating conditions. For instance, Charpy impact tests can be performed at both ambient and reduced temperatures, sometimes as low as -425°F (-254°C) for metals.
-
Temperature conditioning involves placing specimens in a temperature-controlled chamber for a specified period. In this way, the entire specimen reaches the target temperature uniformly.
-
-
Humidity Conditioning:
-
Plastics, for example, can have mechanical properties affected by humidity. Specimens are conditioned in a controlled humidity environment (typically 23±2°C and 50±5% relative humidity) for at least 40 hours before testing.
-
Conditioning Equipment
-
Temperature Chambers:
-
These chambers maintain precise temperatures under a range of conditions. They are necessary for conditioning specimens that require testing at sub-ambient or elevated temperatures.
-
-
Humidity Chambers:
-
Used for conditioning plastic specimens, these chambers maintain controlled humidity levels. As a result, specimens are exposed to consistent environments that mimic the conditions in real-life settings.
-
Standards for Charpy and Izod Specimen Preparation
You must comply with specific standards when preparing U and V-notched specimens for Charpy and Izod impact testing. These standards provide detailed guidelines on specimen dimensions, preparation, and testing procedures. The following are the most common sample preparation standards:
Key Standards for Sample Preparation and Impact Testing
-
ASTM E23: Standard Test Methods for Notched Bar Impact Testing of Metallic Materials
-
Scope: This standard specifies the requirements for notched-bar impact testing using both Charpy and Izod methods. It includes guidelines for specimen dimensions, preparation, and testing procedures.
-
Specimen Dimensions:
-
Charpy V-Notch: 55 mm length, 10 mm width, 10 mm thickness, with a 2 mm deep notch and a 45° angle.
-
Charpy U-Notch: 55 mm length, 10 mm width, 10 mm thickness, with a 1 mm radius and either a 2 mm or 5 mm depth.
-
-
-
ISO 148-1: Metallic Materials – Charpy Pendulum Impact Test – Part 1: Test Method
-
Scope: This international standard describes the method for determining the Charpy impact strength of metallic materials. It covers both V-notched and U-notched specimens.
-
Specimen Requirements: Similar to ASTM E23, with detailed guidelines on dimensions and preparation to guarantee uniformity between different laboratories and applications.
-
-
ASTM D256: Standard Test Methods for Determining Izod Pendulum Impact Resistance of Plastics
-
Scope: This standard outlines the procedures for determining plastic impact resistance using the Izod pendulum test. It also provides detailed guidelines for specimen preparation.
-
Specimen Dimensions: Typically 64 mm x 12.7 mm x 3.2 mm for plastics, with a single V-notch.
-
-
ISO 179-1: Plastics – Determination of Charpy Impact Properties – Part 1: Non-instrumented Impact Test
-
Scope: This standard specifies the method for determining plastic Charpy impact resistance, including detailed guidelines on specimen preparation and notch configurations.
-
Common Issues and Troubleshooting in Preparing Impact Testing Specimens
It goes without saying that the preparation of U- and V-notched specimens for impact testing is a complex and detailed process. If something gets wrong at any step, correcting it can be challenging. There may be a need to carefully rework the specimen to remove existing issues or create a new one entirely. Some of the most common issues encountered during specimen preparation include:
-
Inconsistent Notch Dimensions: Variations in the depth, angle, or radius of the notch can lead to inconsistent test results. To troubleshoot this issue, notching and broaching machines must be regularly calibrated. Additionally, using precision measurement tools like calipers and micrometers to verify the dimensions of each notch can help verify that specimens meet the specified standards. Discarding any specimens that do not meet these standards is also crucial to maintaining consistency.
-
Material Deformation During Cutting: The material may deform during the cutting process, which can affect the specimen’s integrity. To address this issue, appropriate cooling and lubrication techniques should be used to reduce heat generation and friction during cutting. Making sure that cutting tools are sharp and suitable for the material being cut can also help prevent deformation.
-
Overheating During Machining: Excessive heat during notching can alter material properties. To minimize this risk, the cutting speed and feed rate should be adjusted to reduce heat generation. Allowing the material to cool can be achieved by using intermittent cutting techniques. Implementing cooling systems, such as air or liquid coolants, can also help dissipate heat during machining.
-
Incorrect Specimen Dimensions: Specimens may not conform to standard dimensions for accurate testing. CNC machines or precision cutters can achieve the exact dimensions required by standards. Additionally, inspecting the raw material dimensions before cutting can make sure they meet the initial size requirements.
-
Surface Imperfections: Surface defects such as burrs or scratches can introduce stress concentrators that affect test results. To address this issue, carefully deburr the specimens after cutting to remove any sharp edges or surface irregularities. Performing a thorough visual inspection and using surface measurement tools can help detect and address imperfections.
-
Environmental Variability: Variations in temperature and humidity during specimen conditioning can affect material properties. Using environmental chambers to condition specimens at standardized temperature and humidity levels before testing can mitigate this issue. For all specimens, the same conditioning procedure should be followed.
-
Improper Notch Placement: Misalignment of the notch relative to the intended point of impact can lead to inaccurate results. Using alignment fixtures or jigs can ensure that the notch is precisely placed in the center of the specimen. Double-checking the alignment before the impact test guarantees accuracy.
The Role of Reliable Equipment in Testing and Specimen Preparation
Impact tests can be divided into two main parts: creating accurate specimens and accurately executing the tests. This is why it is undeniable that reliable equipment is key to the preparation and testing of U- and V-notched specimens.
Having reliable equipment makes sure that the preparation phase, which involves notching and machining specimens, is carried out with the highest precision. For instance, using precision cutting tools like CNC machines helps ensure that the specimens are cut to the exact dimensions required by the standards. Notching machines and broaching machines are required for creating precise notches that meet specific dimensional tolerances. These machines must be regularly calibrated and maintained to produce consistent and accurate notches, which are critical for subsequent tests’ reliability.
Once the specimens are prepared, testing is the next step. Charpy and Izod impact testers measure the energy absorbed by a specimen during fracture, providing data on the material’s toughness.
Both phases require reliable equipment. Regular calibration and maintenance prevent inaccuracies and inconsistencies that compromise test results. This guarantees specimen preparation and testing under standardized conditions.
At NextGen Material Testing Inc., we specialize in material testing and understand the importance of high accuracy and reliability in this field. We supply advanced equipment for specimen preparation, such as broaching machines, and testing, including Charpy and Izod impact testers.
GenNotch 4000 Series – Specimen Notching/Broaching Machine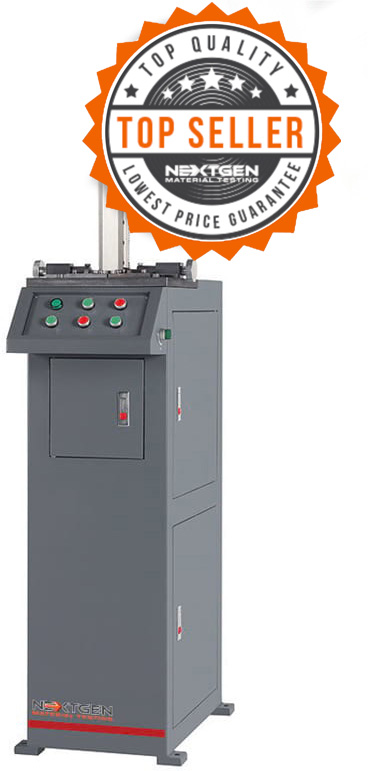
The GenNotch 4000 Series is a dual-chamber motorized broaching/notching machine specifically designed for preparing Charpy and Izod V-type and U-type notch specimens. This floor-mounted, self-contained unit features a user-friendly interface that simplifies operation, making it ideal for high-precision notching tasks.
Key features of the GenNotch 4000 include its dual broaching system, which allows two specimens to be broached at once within seconds. This machine offers exceptional accuracy and repeatability, providing high-quality notching equivalent to milling machines. It is equipped with state-of-the-art broaching knives, available for both V- and U-type specimen preparation needs, capable of handling specimens up to 60 HRC.
Class D – Single Column Charpy Impact Tester
The Class D – Charpy Impact Tester is a dual-column system specifically designed for Charpy Impact testing in compliance with ASTM E23, ISO 148, and EN10045 standards. It offers two models with peak capacities of 450J and 750J, and optional pendulums for 150J, 300J, 450J, and 600J.
The Class D tester is a fully enclosed system that can be equipped with optional automatic specimen feeding or automatic cooling cycles. It features both analog and digital readouts for higher accuracy, with the option to connect to a computer for advanced analysis using NextGen’s software. This robust solution supports high-energy pendulum impact requirements and allows future upgrades.
Summarizing The Preparation of U- and V- Notched Specimens
U- and V-notched specimens for impact testing require precision and compliance with standards. It starts with selecting the appropriate material, taking into account its properties and the specific parameters of the test standards. The material is then cut to exact dimensions using advanced tools like CNC machines and precision cutters.
Following the cutting process, the notches are machined using specialized equipment such as notching and broaching machines. These machines are necessary for creating accurate and consistent notches. The notches must meet specific dimensional tolerances. Moreover, regular calibration and maintenance of the equipment are needed to achieve this precision.
Specimen conditioning is another important step, involving specimen stabilization under controlled environmental conditions. Conditioning typically involves maintaining specific temperature and humidity levels to mimic real-world conditions.
Accurate testing is conducted using Charpy and Izod impact testers, which measure the energy absorbed by specimens during fracture. The reliability of these results hinges on the precision of both specimen preparation and testing equipment.
At NextGen Material Testing Inc., we are dedicated to supporting your material testing needs with our advanced equipment for specimen preparation and impact testing. Whether you require high-precision notching machines, broaching equipment, or reliable Charpy and Izod impact testers, we offer solutions that provide high-quality results. For more information, you can request an online quote or contact us directly, and we will help you achieve the best results in material testing.