Freezing Tester – GenFreeze Cold Climate Rubber Testing
This review is part of a series of blog articles in which we look at NextGen Material Testing equipment in the context of its application for quality control of manufacturing products and innovative developments to improve quality. In particular, we will talk about Freezing Tester.
Paradoxical Quality
From a business perspective, there is a paradox between product quality and profitability. If a manufacturer ensures that its products are of high quality and have a long service life, customers will not buy new products as often because the old ones work well and do not require replacement. Therefore, sales will decline, and thus the company’s profitability will suffer. But this view is superficial, because it does not take into account the significant impact of deeper factors that can regulate the commercial success of manufacturers at the strategic level.
First, the level of customer loyalty will always be higher for those companies that produce quality goods for a long time and ensure the long-term use of their products. Loyal customers tend to repeatedly buy products from the same manufacturer and recommend it to their friends and family, which increases the demand for products and maintains it through generations. It is this longevity that makes a brand’s reputation famous for the high quality of its products.
Secondly, manufacturers strive to constantly improve and refine their products. Even if they are of high quality and retain their functionality for a long time, they may simply become obsolete. Therefore, innovations and new features can stimulate new demand for updated models.
So, while high quality products may reduce the frequency of purchases, they also create significant benefits that offset the impact of this effect and contribute to the company’s success in the long run. On the contrary, companies that try to exploit the fleeting effect of increased demand by reducing product quality quickly lose consumer loyalty and become a thing of the past.
That’s why high quality is a critical aspect of any product and is always at the center of manufacturers’ attention. Let’s take a closer look at how the quality of manufactured goods affects the success of manufacturing companies.
High Quality Freezing Tester as the Key to Success
High quality products primarily bring satisfaction and comfort to customers, creating loyalty to the manufacturer’s brand in their minds. Satisfied people usually come back for more purchases and recommend products to their friends, which helps to increase sales and brand reputation. Product reliability ensures the safety of users and reduces the risks of claims and complaints and returns, reducing warranty and repair costs.
For brands, recognized high quality is an important competitive advantage. Excellent product quality can attract more customers than competitors who offer inferior products. This is the most important part of a brand’s reputation. It is those brands that are famous for the impeccability of their products that gain consumer trust and succeed in the market.
Overall, quality is a key success factor for manufacturers, as it affects customer satisfaction, safety, reputation, competitiveness, and production efficiency. Continuously striving to improve products helps ensure sustainable development and market success.
Freezing Tester Testing will Help Improve Product Quality
Making a product of high quality also means that it can be used for a long time. Manufacturers of footwear, textiles, rubber and plastic products are interested in knowing how external factors will affect their products during use. Therefore, they subject their products to tests at high and low temperatures, humidity, and ultraviolet radiation. This requires them to invest in special textile, rubber and leather testing equipment, to set up and maintain the relevant laboratories, and to employ specialists. But in return, they gain invaluable knowledge about the behavior of their products during use.
Different materials may react differently to extreme temperatures, humidity, and ultraviolet radiation. These conditions can cause changes in the structure and properties of materials, which can affect their strength, flexibility, color, and other characteristics. Footwear and clothing are used in different climatic conditions. For example, winter footwear must have cold climate suitability, and sportswear must be resistant to humidity and ultraviolet radiation. Testing helps to ensure that materials can withstand extreme conditions, and that products made from them meet safety requirements and can provide comfort and protection to users in cold environments.
Many industries, such as the textile and footwear industry, have standards and regulations that manufacturers must follow when developing products. These standards include requirements for the resistance of materials to various conditions with a description of the tests that must be performed.
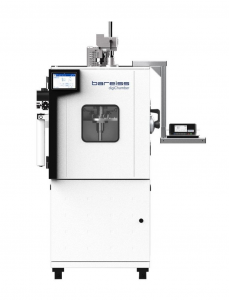
The desire to improve product quality drives developers to study and implement new materials – they are constantly looking for those that are more resistant to extreme conditions and have better performance. Testing helps to study new materials and determine their capabilities and limitations in order to implement them in production and product development.
Read more in our blog:
- DigiChamber – Temperature Controlled Hardness Tester Review – heating and freezing tester in the temperature range -40° to 180°C (-40° to 356°F)
- Discoloration Meter – Review by NextGen Material Testing – UV wear testing of textile products at temperatures from room temperature to 200°C (392°F)
In general, testing helps manufacturers ensure the quality and reliability of their products, compliance with standards and regulations, and the comfort, safety, and satisfaction of users in various operating conditions.
Freezing Tests
In general, freezing testers help to perform controlled experiments and study the properties of materials and products at low temperatures. This allows manufacturers, researchers, and professionals from various industries to make informed decisions and ensure the high quality of their products even under extreme conditions.
Freeze testing is particularly important for products and materials that are used in cold environments, such as in space or arctic regions. Freezing is also used to preserve food, and thus the plastic packaging of such products is also subject to preliminary testing to ensure food safety and quality. The same applies to medical products and biological samples freezing of which is also used.
Flexibility and Wear Resistance at Low Temperatures
Extreme cold can affect the durability of items made of leather, textiles, rubber and plastics, and other materials, especially if they are subjected to mechanical stress such as bending, tension, and friction.
Freezing testers are the key instrument for determining the resistance of materials to low temperatures. This allows manufacturers to evaluate how materials react to extreme cold environment to check their cold climate suitability, which is critical for products that are used in cold regions or during the winter.
During freeze testing, material samples such as rubber, leather, plastic, polyurethane leather, and others are subjected to controlled cooling to low temperatures, often as low as -30°C or even lower. This allows us to simulate extreme weather conditions that products may encounter in real life, such as cold winter days. Polyurethane leather is also subjected to freezing bending tests, as it is often used as a substitute for natural leather. Such studies are used in optimization of the manufacturing processes aimed to improving frost resistance characteristics of goods.
Materials can become deformed, brittle, or split due to changes in their physical structure when exposed to cold environment. With a use of freezing testers it is possible to find changes in structure, flexibility, strength, and ability to retain shape at low temperatures. Assessing such changes helps determine how a product may behave. This, in turn, helps to expand the geographical scope of product application to regions with low temperatures and extremely cold climates.
An Interesting Fact: Freezing on Guard for Museum Valuables
Interestingly, freezing is also used to control insects that are introduced into natural textiles in museums and private collections. This method has now become very common for the preservation of both large and small collections, because while it is highly effective, it is simple, environmentally friendly, leaves no traces, and can be performed by non-technical personnel. However, at the beginning of its implementation, there was a natural concern about whether freezing would harm museum exhibits. The question also arose as to what kind of freezing conditions should be optimally used to disinfect cultural heritage objects.
Since the second half of the 1980s, research has been conducted on how freezing affects the physical properties of textile materials, in particular antique textiles, in the presence or absence of a humid environment. Using freezing testers both single and repeated freezing effects were carefully studied, with a clear regulation of the rate of temperature decrease and its increase during thawing. The results of such studies have created the basis for low-temperature pest control practices in museums.
GenFreeze – the Ideal Freezing Tester for your Quality Control Lab
GenFreeze is a testing system for determining the flexural resistance of footwear, leather, rubber, plastic, and polyurethane leather samples at low temperatures. Such studies help determine the applicability of such materials or products for use in cold climates.
The equipment is available in two versions: GenFreeze-H and GenFreeze-V, which differ in size and temperature ranges:
GenFreeze-H |
GenFreeze-V |
|
---|---|---|
Interior dimensions |
23.6 x 23.6 x 19.7″ 600 x 600 x 500 mm |
23.6 x 23.6 x 21.6″ 600 x 600 x 550 mm |
Temperature range |
RT to -30°C |
RT to -50°C |
Both variants of the freezing testers have a stainless steel test chamber with a mechanical device for fixing samples and performing vamp flexing testing in a cold environment. The cooling system operates using environmentally friendly refrigerant R404, and is capable of lowering the temperature to -30°C within 60 minutes and maintaining the set temperature throughout the entire volume of the test chamber with an accuracy of ±1°C.
NextGen Material Testing guarantees the high quality and reliability of the GenFreeze series equipment as well as the accuracy of the results of tests of the wear resistance of finished footwear when bending soles, other leather and textile products.
For more detailed information about the freezing tester GenFreeze, make a request on the website, and one of our representatives will be able to answer all your questions.