Our access to natural resources is directly affected by mining operations, which require a thorough understanding of soil behavior. There are specially designed tools that can help with this task, offering precise analysis and insights into the earth’s subsurface. Hence, this blog provides an overview of two innovative tools developed by NextGen Material Testing Inc. to increase understanding of soil mechanics: the Dynamic Triaxial Systems 1000 kPa and AUTOTRIAX Automatic Triaxial Test System.
This discussion explores the specific features and specifications of these systems and highlights their significance in assessing soil stability and response in different situations, with a focus on mining. In addition, we will provide an overview of the standards that these products meet, which is crucial to ensuring their reliability and accuracy. It will also discuss how software management systems facilitate their operation, offering streamlined and efficient handling of complex data, as well as how these tools integrate advanced technology with practical applications in the field of soil mechanics.
Why is Soil Mechanics So Significant in Mining?
To begin with, it is necessary to understand why mining is one of those industries that requires a comprehensive understanding of soil mechanics. The study of soil mechanics focuses on the behavior of soils under force or changes in moisture, pressure, and temperature. Mining, where operations often occur beneath the ground level, requires an understanding of soil properties in order to ensure the stability of mine structures as well as the safety of mining operations. An in-depth knowledge of soil mechanics allows us to understand how different soil types respond to different conditions, such as load-bearing capacity and potential shifts or collapses. The application of this knowledge is key to the design of stable mine shafts, tunnels, and other underground structures.
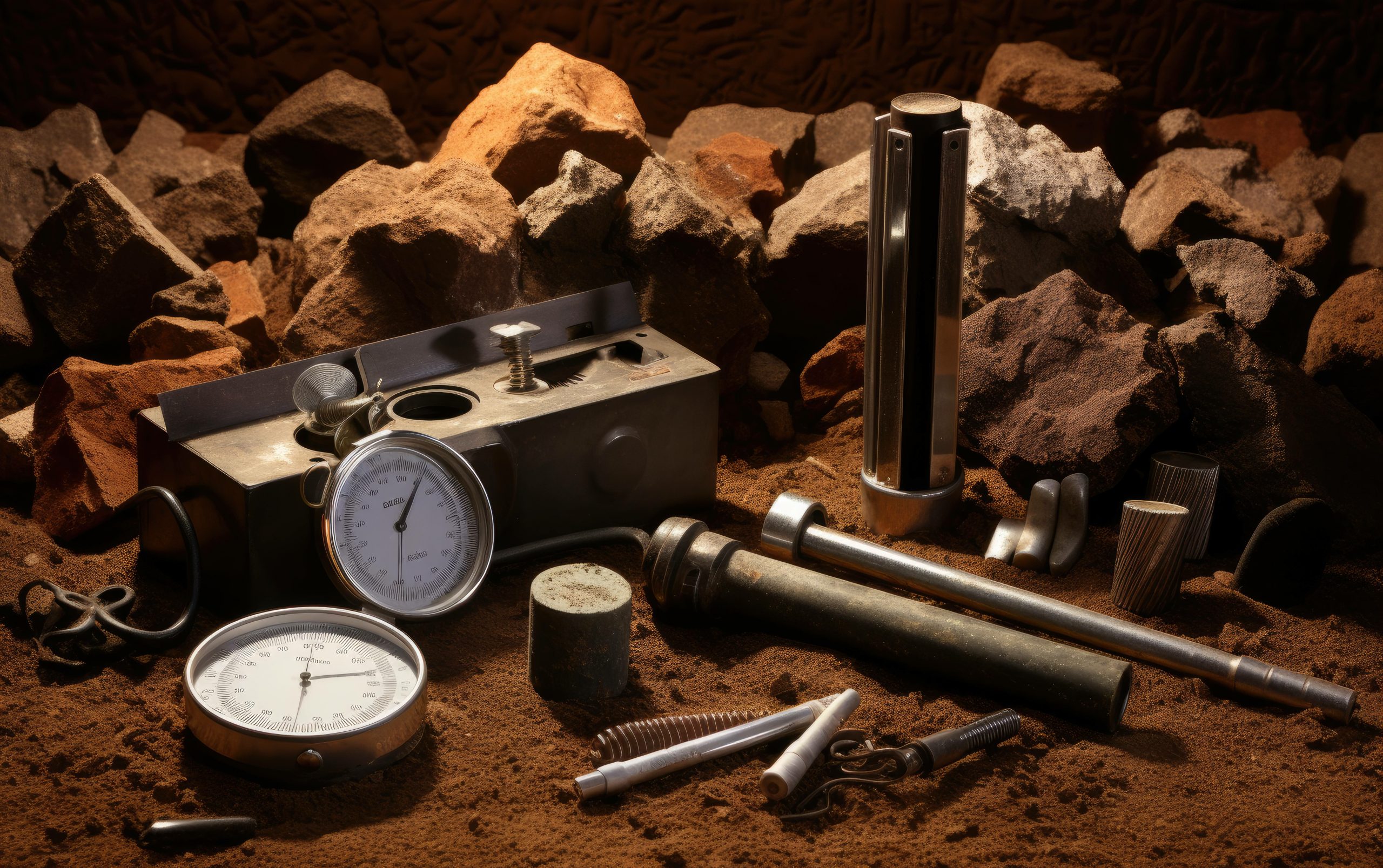
Mining has benefited greatly from soil mechanics, particularly in the area of risk mitigation. By analyzing the soil, it is possible to predict and prevent landslides, sinkholes, and subsidence, which can be catastrophic for mining operations. As an example, engineers can predict the behavior of soils and rocks under mining activities by assessing their porosity, permeability, and shear strength. The prediction of soil mechanics is crucial to preventing mining accidents like the 2010 Copiapó mining accident in Chile, where effective soil mechanics could have prevented the collapse of the mine that trapped 33 miners underground.
In addition to contributing to safety, soil mechanics also contributes to the efficiency and environmental sustainability of mining operations. It is possible for mining companies to optimize their extraction methods by understanding the soil’s physical and chemical properties, thereby reducing the amount of unnecessary excavation and minimizing the environmental impact. Also, a soil mechanics study can help determine the most appropriate locations for waste disposal and tailing ponds in order to avoid contamination of the surrounding environment by these byproducts. In open-pit mines, soil mechanics is used to design slopes to prevent landslides, protecting the surrounding ecosystems in the process.
Soil mechanics provides insights beyond selecting the appropriate drilling equipment. Mining operations’ overall strategy depends on them. As a result of this knowledge, a range of equipment is deployed and operated in a way. This ensures that each piece is not only appropriate for the soil conditions in question but also performs to its highest potential. Heavy machinery is placed and moved in accordance with the load-bearing capacities of the soil, reducing the risk of sinkholes and uneven settlement, which could compromise safety and efficiency during mining operations.
As well, soil mechanics is vitally important in the planning of mining operations in sequence. The mining engineer can schedule excavation and drilling in a manner that maintains the integrity of the mine site by understanding the sequential impact of different types of soil disturbance. Using this approach minimizes the risk of unexpected soil shifts or collapses, which is particularly important in areas prone to seismic activity or where geological formations are complex.
Exploring Soil Mechanics in Other Industrial Sectors
It is worth noting that soil mechanics plays a critical role in a number of other industries in addition to mining. In the same way that Dynamic Triaxial Systems 1000 kPa can greatly benefit mining operations, soil mechanics has become an integral part of construction, agriculture, and environmental engineering.
Construction Industry
In the construction industry, soil mechanics is crucial to ensuring the stability and safety of structures. In order to determine whether a site is suitable for construction, soil testing must be conducted prior to the start of any project. It involves assessing the soil’s ability to support structures, its drainage properties, and its potential for settlement and expansion. During the construction of skyscrapers, soil mechanics guides the design of deep foundations, which are essential to support the enormous weight of such structures. Advanced soil analysis tools can be used to provide critical data to ensure that the foundation design is robust and appropriate for the specific soil conditions.
Agriculture
Understanding soil mechanics is essential for understanding soil health and fertility in agriculture. As a result of soil analysis, farmers and agricultural engineers are able to determine the best crops for specific soil types, optimize irrigation systems, and prevent soil erosion. A soil mechanics study can provide information regarding the soil’s ability to retain water and nutrients, which is crucial for crop growth. Analysis of soil composition and structure can assist in planning sustainable farming practices, as well as ensuring the long-term health and productivity of soils.
Environmental Engineering
Soil mechanics is also an important component of environmental engineering, particularly when it comes to projects involving the remediation of soil and the management of waste. Effective soil cleanup operations require an understanding of the interaction between soil and contaminants. A soil mechanics study can, for example, prove helpful in the design of remediation strategies that will prevent further deterioration of the environment in areas affected by industrial pollution. The use of advanced soil testing tools, like ours, can help assess the extent of contamination and monitor the success of remediation efforts.
Through the information above, it is clear that in each of these industries, soil mechanics provides invaluable insights that guide decision-making processes. Whether it is the construction of a building, the planning of a farm, or cleaning up a polluted site, understanding the behavior of soil under different conditions is crucial to success and sustainability. In these industries, tools that provide detailed soil analysis, such as the AUTOTRIAX Automatic Triaxial Test System, are indispensable, enabling professionals to make informed and effective decisions.
Introduction to Advanced Triaxial Testing Systems
Having recognized the importance of soil mechanics across various industries, we are pleased to introduce our advanced systems designed to simplify soil analysis. The Dynamic Triaxial Systems 1000 kPa and the AUTOTRIAX Automatic Triaxial Test System are two of NextGen Material Testing’s exceptional systems in this regard. They are not simply tools, but game-changers in soil mechanics, designed to enhance soil analysis. We will now explore them more closely.
Dynamic Triaxial Systems 1000 kPa are designed for both commercial and research applications. It provides a comprehensive capability for assessing soil behavior under various conditions, such as liquefaction potential, strength degradation due to cyclic loading, shear modulus, damping ratio, and the effects of blasting in mines and quarries. Three-axis closed-loop control, a frequency of up to 10 Hz, and the ability to perform both static and dynamic triaxial tests are among the features of this system. As a result of its versatility, it is ideal for a wide range of applications, ranging from understanding the effects of seismic activity to evaluating the effect of ocean waves on coastal and offshore structures.
On the other hand, the AUTOTRIAX Automatic Triaxial Test System can be expanded in modular steps to provide effective stress, stress path, permeability, and unsaturated soil testing. With this tool, soil samples are able to undergo stress path measurements that are accurate and reliable, which is crucial for replicating changes in stress conditions in soil samples as a result of excavations, construction, or natural events. Due to the automatic control of the system, environmental discrepancies and operator errors are eliminated, which ensures consistent and repeatable results. The system is capable of controlling up to three independent systems, and it can be upgraded to accommodate existing triaxial systems.
In order to review these products more closely, we will begin with a closer examination of the Dynamic Triaxial Systems 1000 kPa, examining its capabilities and applications in more detail.
Dynamic Triaxial Systems 1000 kPa
As we already said, Dynamic Triaxial Systems 1000 kPa are suitable for both commercial and research laboratories. By assessing factors such as shear modulus, damping ratio, and blasting impact, our system analyzes soil behavior in scenarios such as mining operations and coastal engineering. Due to its three-axis closed-loop control and ability to conduct static and dynamic triaxial tests, it is an ideal choice for examining soil responses to seismic activity and oceanic effects.
System Capabilities and Standards of Dynamic Triaxial Systems
Designed to comply with ASTM D 5311 standards, the Dynamic Triaxial Systems 1000 kPa meets established procedures for cyclic triaxial soil testing. Under this standard, the system is guaranteed to be suitable for determining soil resilience and deformation under repeated loading conditions. It is important to note that ASTM D 5311 compliance ensures that the system produces reliable and consistent results, which are crucial to accurate soil behavior analysis in a variety of geotechnical engineering applications. The control system effectively manages three closed-loop axes, encompassing vertical load/displacement (up to 15 mm with a 5 kN actuator or 25 mm with a 5 kN actuator), cell pressure, and back pressure, each up to 1000 kPa.
The base system consists of either a Tritech 50 or Tritech 100 Triaxial load frame, the actuator, and the CDC Compact Dynamic Controller for data acquisition, control, and processing. To accommodate different frame capacities and actuator strengths, this setup is available in four variations: NG-WF7005, NG-WF7006, NG-WF7010, and NG-WF7015.
As a result of the recent upgrade with a Dynatriax PID control, the system has been enhanced in terms of sensitivity and accuracy. This upgrade features an efficient algorithm with a larger gain range, manual and automatic amplitude controls, which allow the user to compensate for system changes during cycling, and an improved tuning panel with a user-friendly interface. Both static and cyclic test stages require these features for optimum system control.
Technical Features and Flexibility of Dynamic Triaxial Systems 1000 kPa
There is a static load capacity of 50 or 100 kN and a static vertical displacement of up to 100 mm for these frames. The double-acting pneumatic actuators, which are integral to the system, are equipped with an integrated LVDT displacement transducer. There is a dynamic load capacity of 5 kN or 14 kN and a dynamic vertical displacement of 25 or 15 mm available with the actuators. In terms of operating frequency, the system can reach up to 10 Hz, depending on the test conditions, with a maximum servo-valve frequency of 70 Hz, and it requires a minimum air supply of 800 kPa.
CDC Compact Dynamic Controller also manages the three closed-loop axes and interfaces with the PC via Ethernet. A 16-bit ADC provides accurate data collection and analysis for the 16 transducer input channels. With the pre-installed Windows-based software on the provided computer, various stages of a cyclic triaxial test can be controlled, from saturation to consolidation, and from stress path to cyclic loading.
Reliability and Modularity of Dynamic Triaxial Systems at 1000 kPa
With its ability to produce standard and custom wave shapes, the Dynamic Triaxial Systems 1000 kPa excels in reliability. Using closed-loop PID feedback, the system ensures complete test automation. Furthermore, it features automatic compensation of cell and back pressure during dynamic stages, as well as software-managed calibration and verification of transducers. Additional safety and reliability are provided by the automatic and manual emergency air shut-off functions.
The modular design of the system allows for a unique, programmable multi-stage test procedure. This feature allows users to adjust and modify test stages in response to the behavior of the soil specimen during the test run. As well as this, the design of the system facilitates easy integration with existing static systems, demonstrating its versatility and adaptability to a variety of testing requirements.
Automatic Triaxial Test Systems
Further reviewing our second key product, our AUTOTRIAX Automatic Triaxial Test System, which is yet another tool for optimizing soil mechanics testing. With its ability to perform a variety of crucial tests, this system is particularly renowned for its Effective Stress and Stress Path Triaxial Tests. It is designed to simulate the changing soil stress conditions under a wide range of conditions, including excavation and construction. Furthermore, the AUTOTRIAX is equipped with the capability of automatically conducting tests for permeability and unsaturated soil.
Main Features of Automatic Triaxial Systems
One of the main features of the AUTOTRIAX system is its AUTOMAX control system, which allows the operator to operate and control several triaxial tests using a personal computer. The system can be expanded in modular steps, allowing for great flexibility in test configurations. The automated control system ensures consistent and reliable test results by eliminating environmental discrepancies and operator errors.
In addition, the system facilitates uninterrupted testing 24 hours a day, 7 days a week, enhancing test performance and reducing operational costs. It is also possible to upgrade the AUTOTRIAX so that it can be integrated with existing triaxial systems of different standards.
Technical Specifications of Automatic Triaxial Test Systems
Autotriax Automatic Triaxial Test Systems consist of specialized components, each of which plays an important role in automating triaxial testing. Among these components are:
- Triaxial Compression Frame: Models NG-WF4005 and NG-WF4010 cater to different load capacities (50 kN and 100 kN, respectively).
- Triaxial Cell with Vacuum Top Cap: Models like the TriCell plus range (NG-WF4070/P to NG-WF4150/P) are equipped with vacuum top caps.
- Control Unit: The RTC Real-Time Control Box, along with the optional NG-WF4537 Expansion Module, provides the central control system for up to three triaxial systems.
- Data Acquisition Unit: The ATD Automatic Triaxial Data Log, and its optional expansion module.
- Pressure Systems: Including both pneumatic (Servo Flow Electro-pneumatic servo-valve) and hydraulic (Hydromatic servo-controlled hydraulic actuator) options, these components allow for pressure control up to 3500 kPa.
- Test Software: This software module interfaces between the operator and the AUTOTRIAX system, automating all stages of testing.
Three independent triaxial systems can be accommodated by configuring these components together in different ways.
Leading-edge Soil Mechanics Testing from NextGen’s Triaxial Test Systems
Understanding soil behavior is critical for many different applications, from mining to construction. Consequently, the Dynamic Triaxial System 1000 kPa is notable for its comprehensive ability to assess soil behavior under a variety of conditions, making it essential for applications such as seismic analysis and coastal engineering. In geotechnical research and commercial laboratories, its versatility, advanced control features, and conformance with ASTM D 5311 standards make it a valuable tool.
As well, the AUTOTRIAX Automatic Triaxial Test System is highly regarded for its ability to conduct effective triaxial tests for stress and stress paths. Its AUTOMAX control system allows multiple tests to be performed simultaneously, providing flexibility and precision. Because the AUTOTRIAX system is modular, it can be adapted and expanded to meet a wide range of soil testing applications, including permeability and unsaturated soil testing.
If any of these products offered by NextGen interest you, please contact us directly or request a quote online. Feel free to ask our team if you have any questions or for assistance in tailoring solutions to your specific needs.