The Significance of DIN Abrasion Testing
One way of measuring the wear resistance of rubber is through DIN Abrasion Testing. The main samples used for this test are tires, soles, and conveyor/drive belts. Tires, conveyor and transmission belts undergo a lot of stress in actual service.
These materials must be able to endure abuse and resistance to wear in their service life. The DIN Abrasion test is also useful in evaluating hoses and rubber floor coverings.
The DIN Abrasion Tester ensures that these materials are safe before mass production. Durable materials are also a sign of better quality. The DIN Abrasion test is by no means an exact determinant of a rubber material’s actual wear resistance. But, it offers a close approximation of it.
Description of the Mechanism
This Rubber Abrasion Tester is a contraption with only a few components:
It has a drive system; a rotating cylindrical drum; and a moving test piece holder.
The drive system contains switches for turning on the machine and switching it off. Some testers have a counter for the number of rotations the drum makes. Some also have reset and adjust switches as well.
The cylindrical drum has a length of 20 inches and a diameter of about 5.91inches. An abrasive sheet covers the entire length of the cylindrical drum. This abrasive medium is grit 60 Corundum, bonded to the drum with strong adhesive tapes. The abrasive sheet will scrape off material from a test piece and should provide a mean of mass loss (mg) of 180 to 220 mg.
The test piece holder attaches to a swivel arm and sledge. The test piece holder can also carry calibrated weights. These weights put a downward force to the test piece and cylindrical drum.
The test piece holder can slide in a lateral direction across the entire length of the drum. It can also rotate in its own axis at the same time that the cylindrical drum rotates.
These features set the DIN Abrader apart from other abrasion testers. Other machines will have a fixed specimen holder pressed against the rotating drum.
A tray at the bottom of the DIN Abrader collects debris from the Rubber Abrasion Test.
DIN Abrasion Testing Operation
Standards
The operator must follow the requirements stated in the following standards during testing:
ASTM D5963, DIN 53516, ISO 4649 and BS-903
These standards contain test methods for determining abrasion resistance of rubbers and elastomers. The Rubber Abrasion Tester must also conform to the specifications in these standards.
The German DIN 53516 is an older standard superseded by the ISO 4649 Abrasion Standard. But the DIN 53516 Abrasion Standard is still valuable and referenced for compliance.
Some of these standards contain similar test methods and specifications. But there are also differences in the requirements and materials used for the test.
The ASTM D5963 Abrasion Standard and DIN 53516 require only 10N to press the test piece against the drum. But the ISO 4649 Abrasion Standard allows for a reduction of 5N of force or an increase of 20N of force in special cases.
The BS-903 Abrasion Standard is a British standard. It contains test methods and guides for selecting vulcanized and other rubber products.
The Rubber Abrasion Test Procedure
An operator prepares the specimen using a test piece cutting tool. The specimen is cylindrical in shape and must fit well into the test piece holder.
Before testing begins, the operator cleans the adhesive sheet. This is to ensure for uniform testing.
The operator turns on the machine and uses a brush to clean the surface of the cylindrical drum as it rotates. This will also remove debris from previous tests. Sometimes the operator uses a safety blow gun to clear out the debris.
The operator now raises the swivel arm to mount the test piece into the holder and secures it in place. He or she may add calibrated weights if needed. Sometimes, test pieces need more weight to put a greater amount of force over the rotating drum. Testing can begin once the abrasive sheet is clean and the test piece is in place.
The operator begins the test by moving the test piece holder back to the starting position. Once set, the operator starts the machine. The test piece then slides through the rotating drum. The operator must ensure that there is no vibration in the test piece holder. Any vibrations may render inaccurate results.
The machine stops after the test piece completes an abrasion distance of 40 meters. This is about 84 revolutions for the rotating cylindrical drum.
The operator performs a series of tests using a test rubber compound and a standard rubber. The operator also needs to perform tests using rotating and non-rotating test pieces.
The Standards contain the exact number of tests that the operator needs to perform. The Abrasion Standards also contain information on how to prepare the test pieces.
After the test, the operator then measures the volume lost in the test and standard compounds. He uses the information to compute the abrasion resistance index. Smaller volume loss values signify better resistance to wear. But a smaller index means poor resistance to rubber abrasion. For a complete system operation, please refer to the DIN Abrasion Tester Operational Manual.
Industries Most Commonly Using the DIN Abrasion Testing Metho
The DIN Abrasion method is used by a variety of industries including:
- Textile
- Leather
- Clothing
- Rubber
- Automotive
- Aerospace
- Bearings and Seals
- Rubber Rollers
- Plastic and Rubber Manufacturers
- R&D Facilities
These industries typically break into sub-industries ranging from small to medium to large size enterprises using the DIN Abrasion method consistently in their quality control practices.
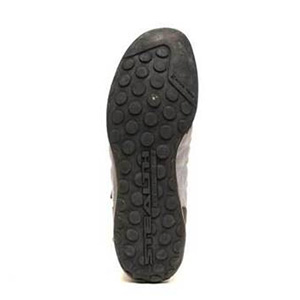
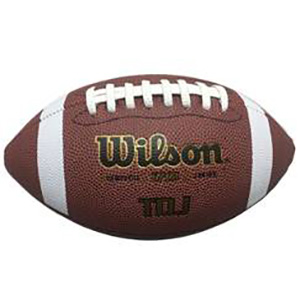
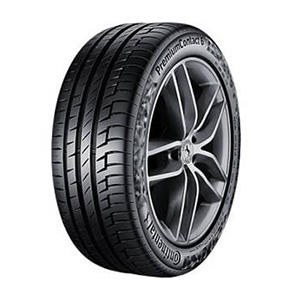
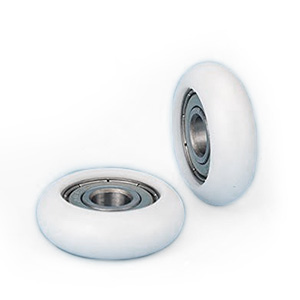
Significance and Benefits of DIN Abrasion Testing
The test results are useful to users, designers and manufacturers of rubber products. The Rubber Abrasion Test is a good indicator of the material’s quality and performance. Designers can use the data in their research. They can also use the information to check for the product’s efficiency. Manufacturers can use the test results to develop better products. And consumers will have the assurance that the materials are superior in quality.