A metal’s ductility and tensile strength are good indicators of its strength and toughness. However, these two qualities alone are not enough to determine if the material is ideal for use in specific applications. Of equal importance is knowing how the material would react when going through sudden impact. This is known as the metal material’s toughness, which is determined through an impact test.
Read on to know more about impact testing, what it is used for, and how it is done.
Resilience and Toughness
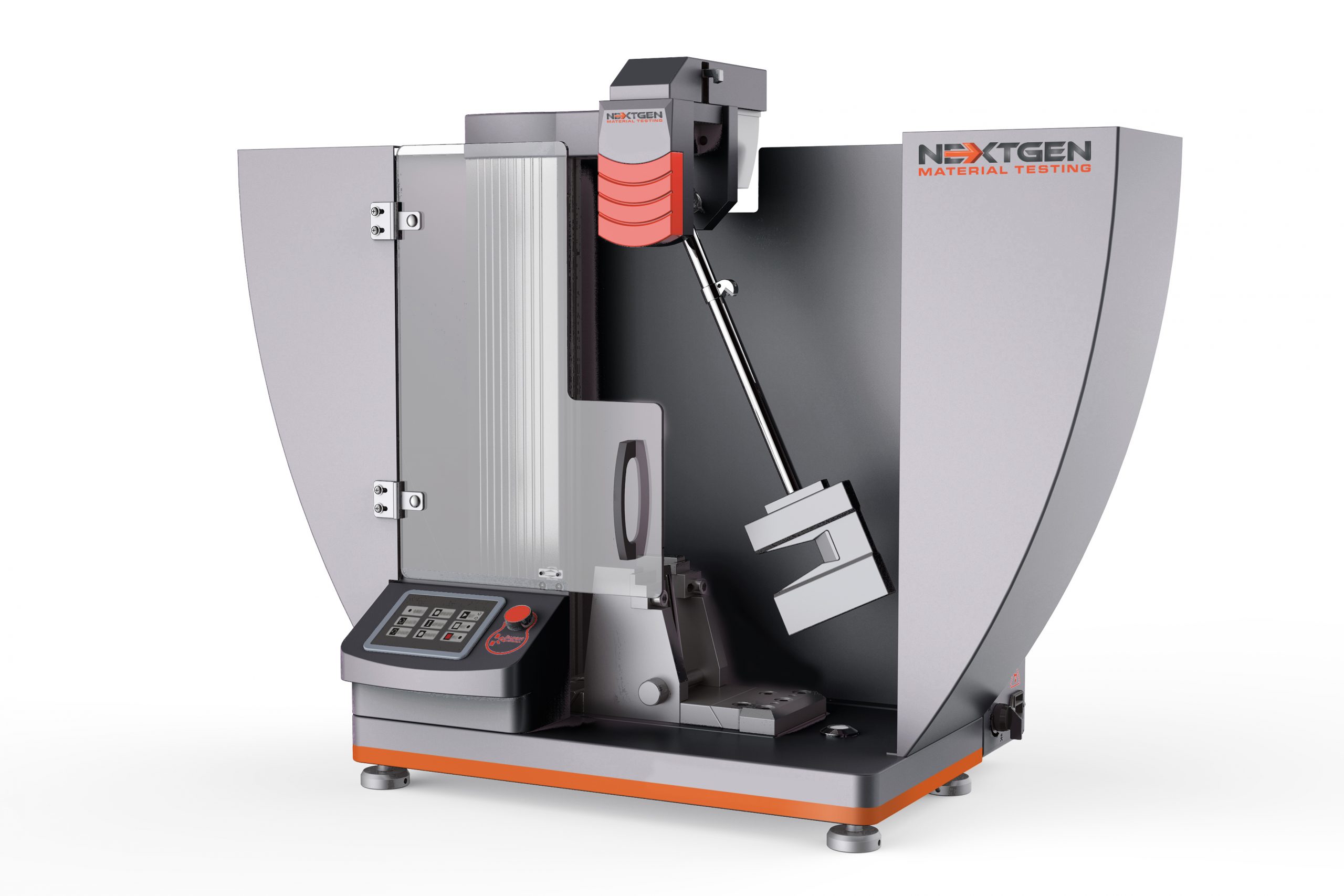
Imagine a plastic material. It will deform when exposed to stress or impact. The point where it is about to deform because of stress or impact indicates the material’s ductility. You can say that the material is ductile when it doesn’t deform easily, and will only start to show signs of wear or tear after a considerable amount of time.
However, just because a material is ductile means it is tough. To be tough, a healthy combination of ductility and strength is necessary. A material possessing a high level of strength and high ductility is considered tougher than one with a lower level of ductility and strength.
One ideal way to measure the true toughness of a material is to calculate the area beneath the stress strain curve using a tensile test. The value is referred to simply as the material’s toughness. This is expressed in the number of energy units per volume. The material toughness is equal to a slow energy absorption by the material.
Let’s take a stress-strain diagram for example to represent a material’s elasticity limit. Divide the diagram into two parts. The left side is referred to as the elastic range. The plastic range is found on the elastic limit’s right side. The area beneath the elastic range’s curve OP measures the energy/unit volume that the material can absorb without sustaining permanent deformation.
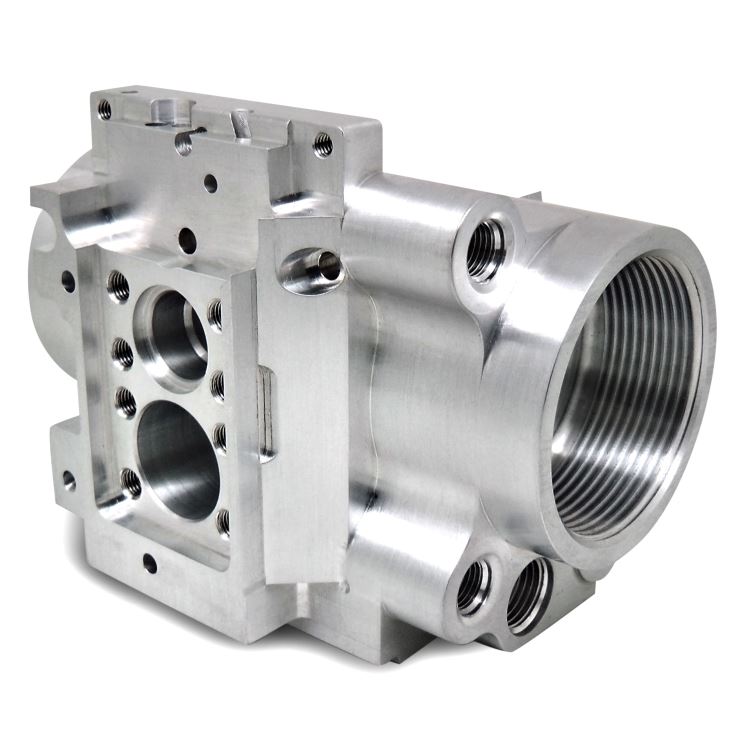
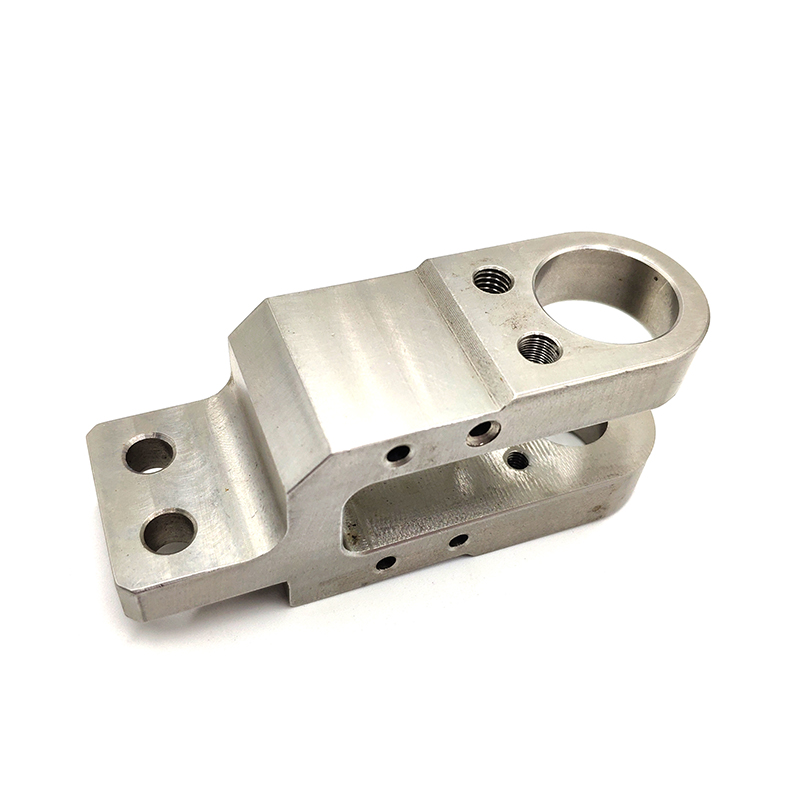
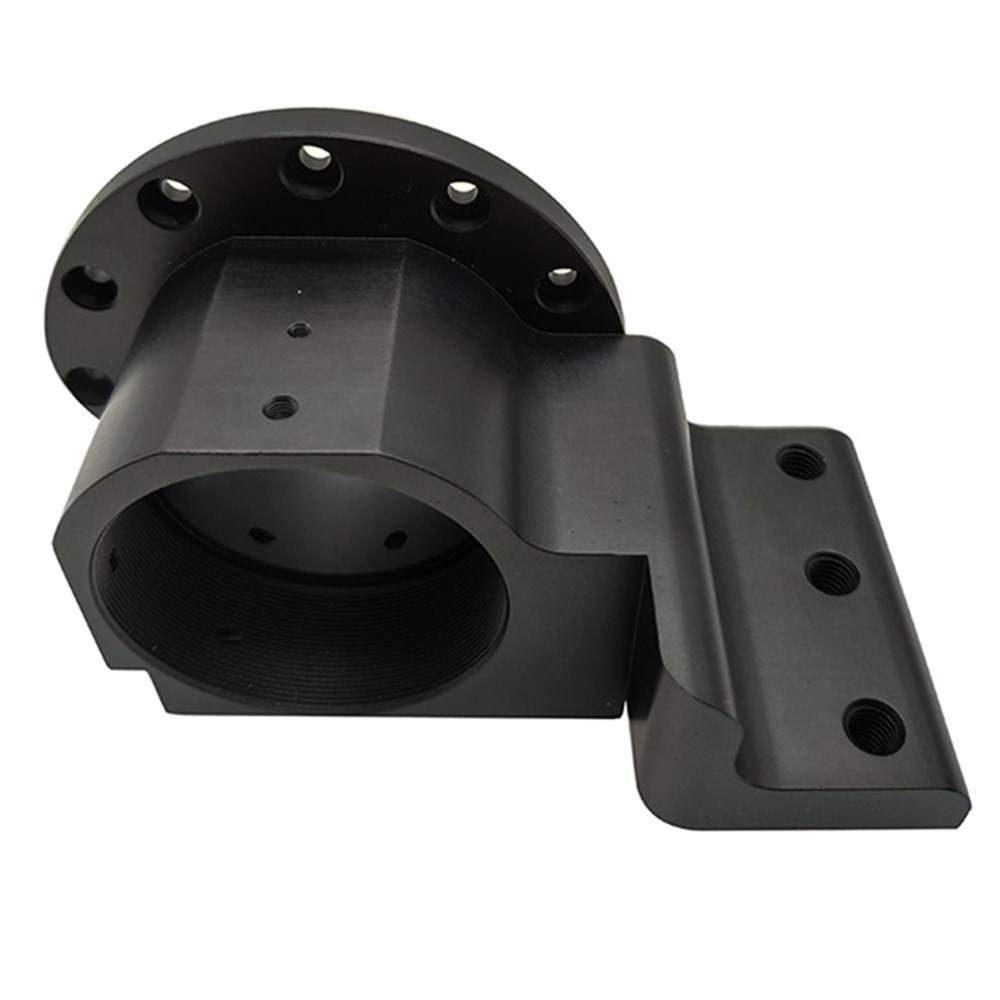
The value is called the resistance modulus. The energy/unit of volume that the material can absorb (or the area under the whole diagram) up to the fracture point is the toughness level. This property mainly belongs in the plastic range. Only a minimal portion of the total absorbed energy can be considered elastic energy.
The following variables have a strong impact on a material’s toughness level:
- Strain rate (or the rate of loading)
- Notch effect
- Temperature
A particular metal may possess a decent amount of toughness under a static load, but it may fail when made to undergo impact or a dynamic load. Both ductility and toughness tend to decrease when the rate of loading gets higher.
Another variable is called the notch effect. This arises from stress distribution. A particular material that may display decent toughness when made to undergo stress that is uniaxial. However, when stress in multiaxial state is generated because of the existence of a notch, the specimen may not be able to endure the concurrent plastic and elastic deformation coming from different directions.
The third variable with a significant influence on material toughness is temperature. You will note that the material’s toughness and ductility will go down as the temperature gets lower.
What Are the Differences between Tough and Strong?
A material that can endure a significant force before rupturing or deforming can be considered a strong material. You can therefore say that a particular material that possesses a high level of tensile strength is strong.
On the other hand, toughness is the property that allows a particular to repel damage from impact. It can be measured through the proper testing procedure. In a stress-strain diagram, it can be seen at the bottom of the diagram that leads up to the fracture point.
The strongest material is one that has the highest tensile strength. On the other hand the material that occupies the biggest area under the diagram can be considered as the toughest material.
So, the strongest material is not necessarily the toughest, and vice versa. Simply put, strength does not always equate to toughness.
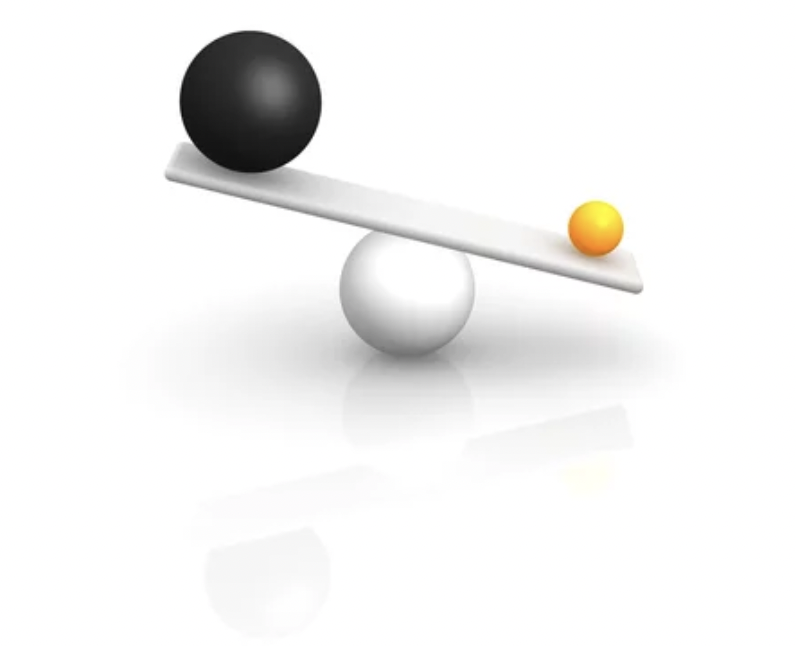
Impact Testing
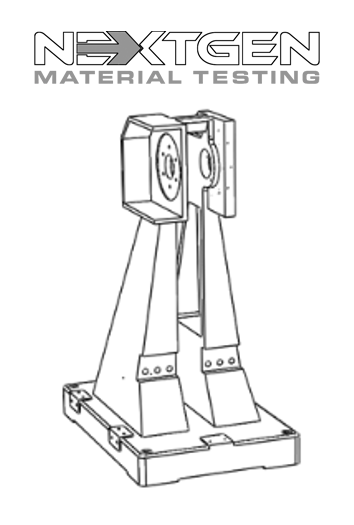
The relative toughness of a material is determined by using either the Izod or Charpy test methods. The two are obviously named after the inventors who started the testing methods.
The impact test is done using a notch-type specimen. In general, two kinds of notches are used. One is the more common V notch, and the other is the keyhole notch. Both types of specimens can be used with Charpy or Izod.
When performing the Charpy impact test, the specimen is positioned on an anvil in a way that it appears like a simple beam with supports at the ends. Meanwhile, in an Izod test, the specimen is held in place by a vice. This way, one of the ends is free and appears as a cantilever beam.
In an impact test, a freely swinging pendulum strikes a notched specimen with a single blow. The pendulum starts to swing from a fixed height upon release. Because the height where the pendulum is coming from is raised before it swings, as well as the pendulum mass are both known, you can pre-determine the energy spent from the blow.
In the case of the specimen used in Charpy testing, the pendulum strikes the sample from behind the V notch. In an Izod test, meanwhile, the specimen with V notch fronting the pendulum is struck above the notch.
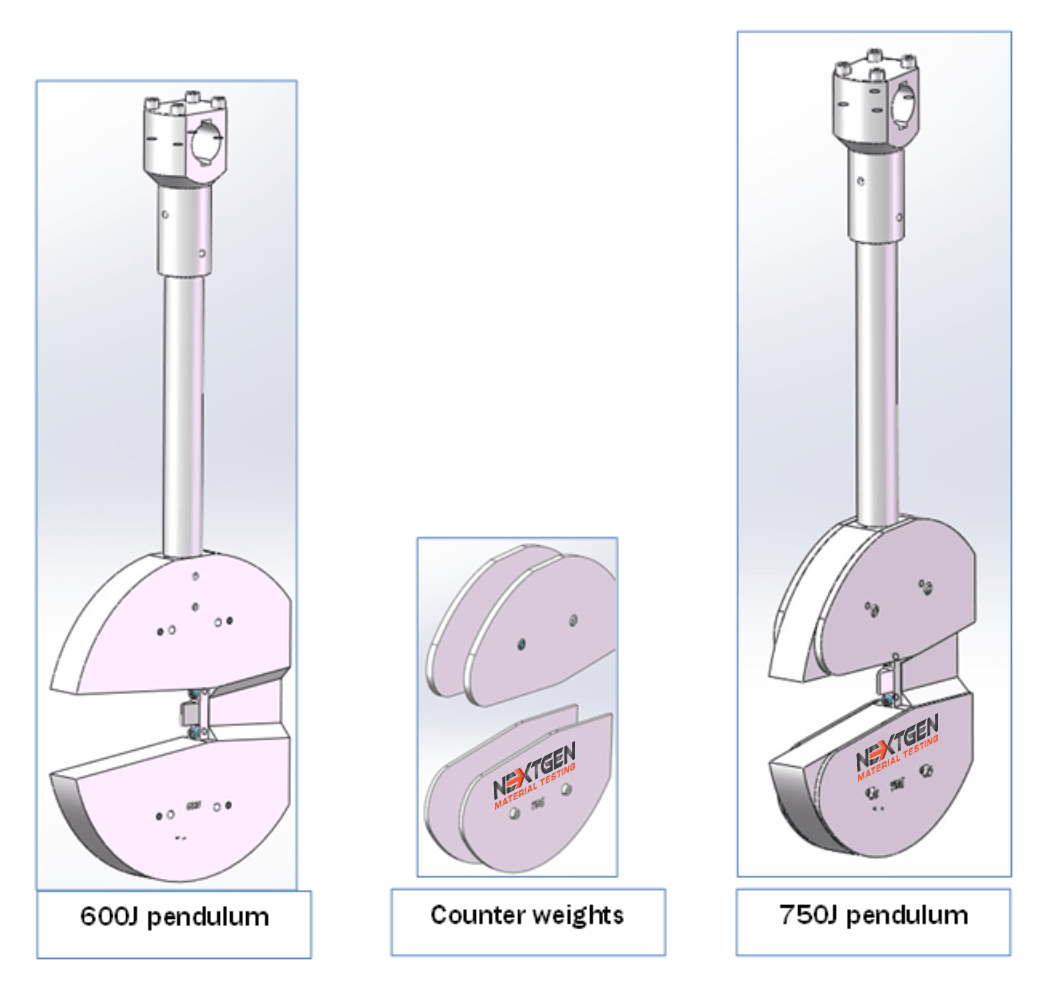
In both tests, some energy from the pendulum is employed to rupture the sample material. This way, the pendulum rises to a particular height that is lower than the original height on either side of the device.
There is a way to indicate the amount of absorbed energy to break the sample material. A Charpy machine, for instance, has a capacity in the energy rage of 220 – 330 ft. lbs. (or 300 – 400 J).
There are times when a machine with less capacity is used. However, it is necessary that the machine always has a substantially higher capacity than the specimen’s absorbed energy. Likewise, in many instances, the testing procedure specifies a temperature other than ambient or room temperature.
Why the Test Temperature Is Significant
Since the temperature has a significant effect on toughness, an Izod or Charpy test is often done repeatedly, testing the specimen under a different temperature with each pass. The results are used to generate an impact toughness graph for a particular material as a temperature function. The impact toughness of the material is then compared vis a vis the temperature graph.
The specimen is more brittle under low temperatures. You can conclude that it has a low impact toughness level. On the other hand, in warm or high temperatures, it has more ductility and a higher impact toughness. The transition temperature can be defined as the limit that separates ductile and brittle behavior. This temperature is usually a very important consideration when choosing the material to use for a particular application.
Ferritic or body centered cubic materials manifest a considerable transition in behavior when undergoing impact testing over widely varying temperatures. Under temperatures above transition, the impact specimen fracture caused by ductile mechanisms (typically microvoid convalescence), absorb a significant amount of energy.
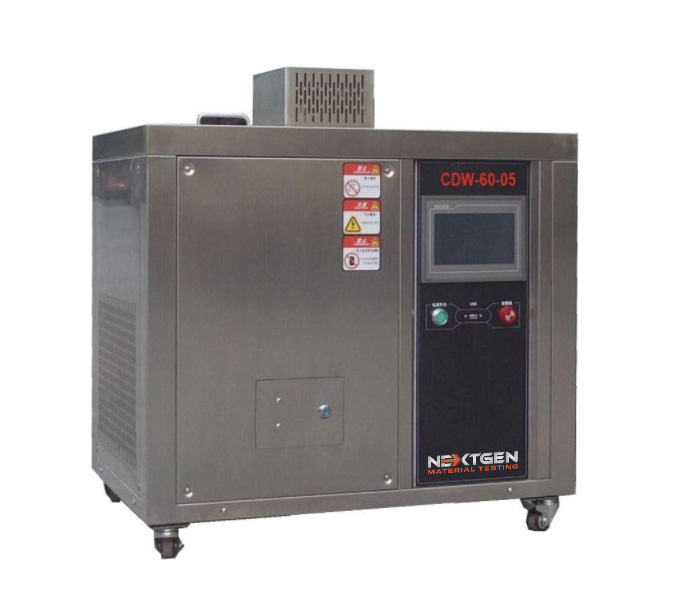
Under lower temperatures, the specimen fractures in a brittle manner (often cleavage type) and absorbs less energy. Within a given transition range, in general, the resulting fracture is often a combination of both brittle and ductile fracture areas.
The transition’s range of temperature from one kind of behavior to another varies, depending on the specimen under testing. As mentioned, different temperatures have varying effects on a specific material’s strength. It is worth mentioning that under room temperature, the specimen manifests characteristics of a ductile material. However, under low temperatures of under -200o C, it tends to act just like a brittle material would.
Based on the above paragraphs, you can conclude that material specification would often require for testing for the amount of energy absorbed, lateral expansion, appearance of fracture, or any combination thereof, at a specific test temperature.
Following is an example to illustrate:
The steel material used in making the hull of the iconic ship Titanic had sufficient strength, but it was low in toughness under cold temperatures. When the gigantic ship struck an iceberg, instead of causing bent steel and small cracks (that show ductile failure) a crack spread quite fast, and became very large within a short period of time (because of brittle failure).
The following ASTM specifications can provide more information about impact testing:
- E23 – These are the standard test methods that use notched bar impact test on metallic materials.
- A370 – These are the standard test methods and definitions used in mechanical testing on steel products.
ASTM A370 also includes requirements of the Charpy impact testing method. However, it solely focuses on steel products.
All of the testing standards offer details for the proper measurement of the absorbed energy by the notched specimen material when facing impact from a swinging pendulum.
Typically, a Charpy test would require that the notched metal sample be resting on the supports at the ends, horizontally, while getting in contact with the vertical anvils that are near the supports. The sample material is then hit opposite the anvils at the center line by a striker attached to a hammer or swinging pendulum.
To make measuring the metal toughness possible using the Charpy impact test, you must get samples from the subject product or material. Typically, samples measure 55 mm in length with a 10×10 mm section as well as a central V notch measuring 2 or 3.3 mm, but may also be a 5 mm U type. The testing standard also provides for reduced section specimens that measure 10×5 or 10×7.5 mm.
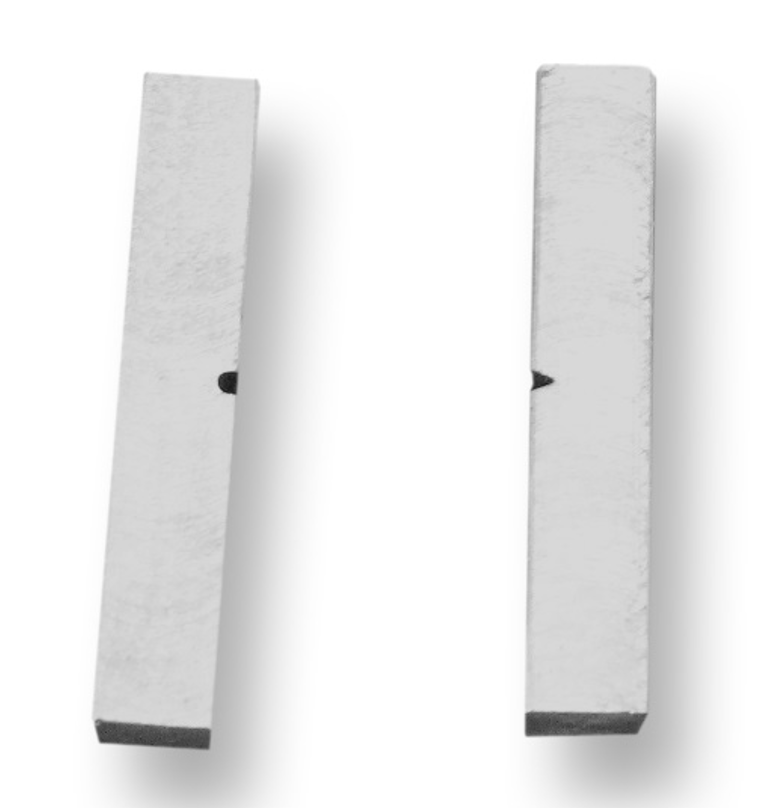
In special cases, the thickness can be interposed between the specimen and the supports to guarantee the perfect strike axiality that has to be provided. The impact is from an instrument that is particularly safe, with solutions that exceed the standard requirements.
For instance, the metal bar that stands mechanically between the armed pendulum bar, and the particular area from where the operator loads the specimen manually.
The wholly interlocked protection guard is likewise available. It has two access doors to allow easy retrieving of the post-test parts of the specimen. The transparent lexan panels allow the operator to witness the impact test. The device comes with a motorized hammer return to the release point. This prevents injuries by eliminating lifting the hammer by the operator.
The ASTM E23 standard specifies the requirements for the Charpy impact testing specimens. In addition, there are applications that require certified results from the NIST or the National Institute of Standards & Technology.
The NIST requires the specimens to be cooled at temperatures of -40° C, and then tested under the same temperature. Thus, it is important to make sure there is a high series energy break cooling bath. Right after the conclusion of the test, it is crucial to send the documentation to the NIST that includes the absorbed impact energy of every specimen, together with the broken pieces of the specimens for the purpose of certification review.
You can expect either a certification (passed) or failure report including recommendations for modifications to pass the succeeding NIST certification attempts. You can submit the procedures to NextGen Service Center who will handle the procedure in its entirety.
Specimens certified by the BCR are likewise available to check the accuracy of the measuring instrument. Charpy pendulums come in various sizes. These are 150, 300, 450, and 750 Joule. Customers can acquire the units with plinth in their pre-compressed form to prevent further foundation works.
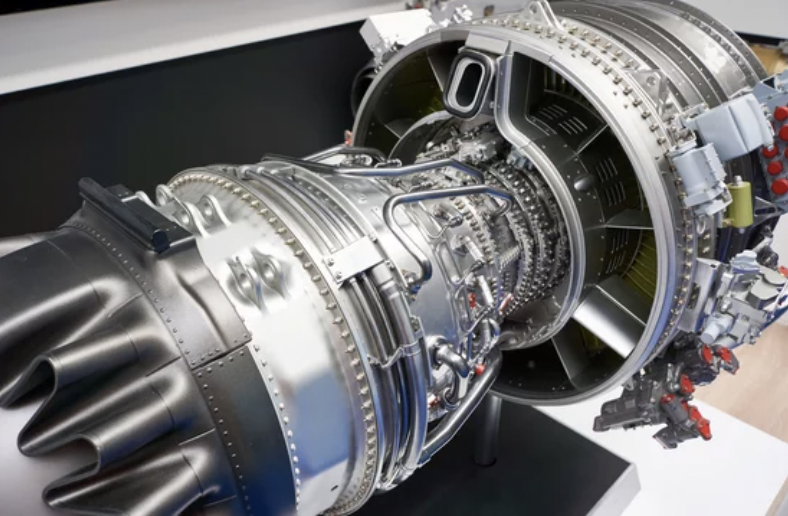
A standard V notch specimen for Charpy tests is 55 mm long, 10 mm square, and with a 2 mm deep notch that has a 0.25 mm tip radius machined on one face.
There are cases when sub-sized Charpy samples with less than 10 mm thickness are tested.
The specimens are supported at the two ends of the anvil, then hit by the pendulum on the opposing face to the notch. The amount of absorbed energy in fracturing the sample is then measured. This indicates the test material’s notch toughness. During the test, the pendulum swings. The swing height is a measure of the absorbed energy in fracturing the specimen.
Traditionally, three specimens are separately tested at a given temperature. The results are then averaged. On the other hand, the tests are performed at various temperatures to produce a transition curve from ductile to brittle.
A Charpy test helps determine the metal classification – whether it is brittle or ductile – which is useful particularly for ferritic steels that manifest a ductile to brittle transition under decreasing temperature.
A metal classified as brittle will absorb a minimal amount of energy on impact testing. A tough and ductile metal, on the other hand, absorbs a big amount of energy. The emergence of a fracture surface likewise provides information on the kind of fracture that occurred – a brittle fracture is crystalline and bright. A ductile fracture is fibrous and dull.
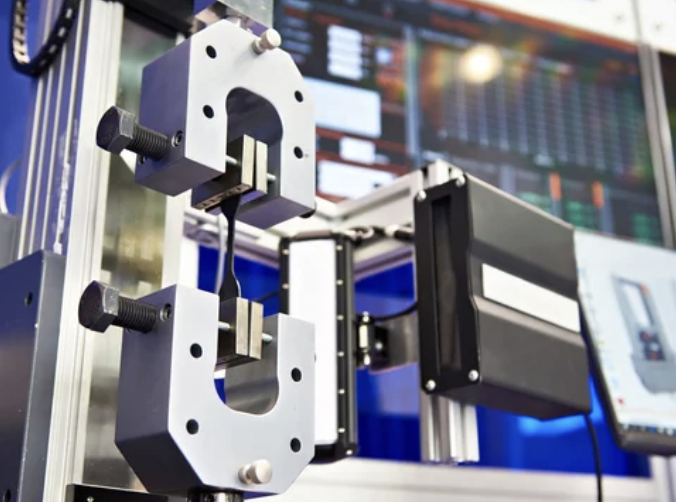
The crystallinity percentage is determined by judging the amount of brittle or crystalline fracture of the broken specimen’s surface. It is a measure of the brittle fracture amount.
Lateral expansion measures the specimen ductility. In tests where a ductile metal is deformed or broken, the test piece shows some deformity before breaking, and the material squeezes out on the compression face’s sides. The amount of energy that forces the specimen to deform is measured in terms of mm of lateral expansion.
To report Charpy test results, the absorbed energy (expressed in J) is always mentioned, while the crystallinity percentage and lateral expansion are both optional in test reports.
It is important to emphasize that Charpy impact tests are qualitative. You can compare the results with each other only or in specified requirements. You cannot use them to compute for the for the fracture toughness of a parent or weld metal.
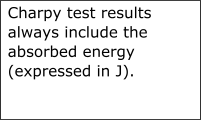
To find an Impact Testing System that best fits your needs, visit NextGen Material Testing, Inc. and request a quotation from a qualified technical consultant.